فرایندهای تولید ناب (Lean Manufacturing) بر کاهش ضایعات، ارائه ارزش به مشتریان و خلق بهبود مستمر تمرکز دارد.
تولید ناب چیست؟
تولید ناب یک فلسفه تولید است که به دنبال به حداقل رساندن ضایعات و در عین حال به حداکثر رساندن بهرهوری و رضایت مشتریان است. «ناب شدن» ممکن است شامل اجرای تعدادی از روشها و ابزارهای مختلفِ افزایش بهرهوری برای دستیابی به بهبود مستمر باشد.
تاریخچه مختصر تولید ناب
اصول پشت تولید ناب ریشه در کمپانی تویوتا دارد. اقدام تایایچی اونو (Taiichi Ohno) برای توسعه سیستم تولید تویوتا به این شرکت خودروسازی کمک کرد تا خود را از رقبایش در ژاپن و سراسر جهان متمایز کند. در سال ۱۹۹۰، کتاب جیمز وومک با عنوان «ماشینی که دنیا را تغییر داد» (Machine that Changed the World) روششناسی تویوتا را به مخاطبان بیشتری معرفی کرد و اصطلاح تولید ناب را رواج داد.
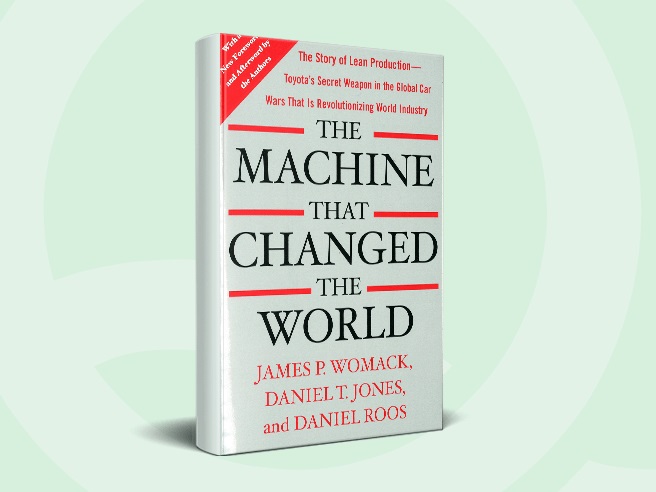
تویوتا بعدها اصول پشت فرهنگ منحصر به فرد و رویکرد خود به تولید را تدوین کرد. این اصول در کتابی با عنوان «راه و روش تویوتا» (Toyota Way) منتشر شدهاند که شامل موارد زیر میشود:
- مدیران باید در تصمیمگیریها، حتی به قیمت فدا کردن سود کوتاه مدت، بر بازهٔ زمانی بلندمدت اولویت دهند.
- از طریق بهبود مستمر (کایزن kaizen) ، فرایندها باید منابع اتلاف (مودا – Muda) مانند تولید بیش از حد و توقفها را حذف کنند.
- متعادلسازی حجم کار (هیجونکا – heijunka) به جلوگیری از سطوح تولید ناهموار (مورا – Mura) و افراد یا تجهیزاتی که بیش از حد کار میکنند، کمک میکند.
- در حالی که باید برای تصمیمگیری وقت بگذارید و تمام گزینهها را در نظر بگیرید، اما باید به سرعت بر اساس تصمیمات خود عمل کنید.
- برای ایجاد تیمهای موثر و پرورش یک فرهنگ عالی، باید بر توسعه حرفهای تأکید کنید.
- به جای دنبال کردن آخرین روندهای فناوری، باید تنها روی استفاده از ابزارهای آزمایش شده و قابل اعتماد تمرکز کنید.
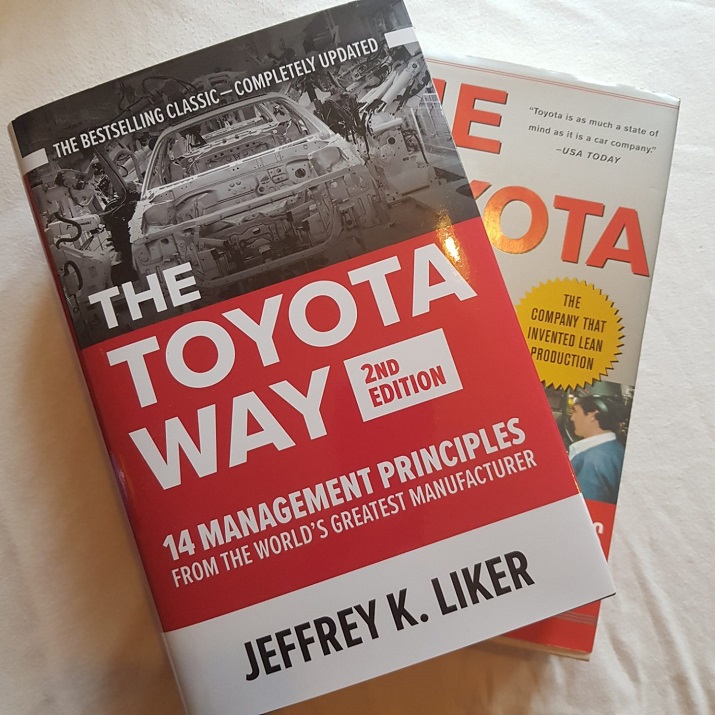
اصول تولید ناب
اصول تولید ناب مجموعهای از اصول و روشهایی است که نقشهٔ راهی را برای سازمانها جهت متحول کردن عملیاتشان فراهم میکند. این اصول شامل موارد زیر است:
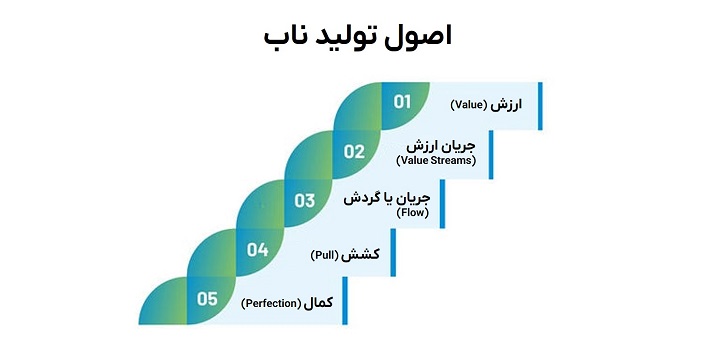
ارزش (Value)
هستهٔ اصلی تولید ناب، تعهد به ارائه ارزشی استثنایی به مشتریان است. سازمانها با درک نیازها، ترجیحات و خواستههای مشتریان، میتوانند فرایندهای خود را برای برآورده کردن آن انتظارات تنظیم کنند. رویکرد مشتریمحور، نوآوری را تقویت میکند و امکان ایجاد محصولات و خدماتی را فراهم میسازد که با مخاطبان هدف هماهنگ باشد. در نهایت، هدف، فراتر رفتن از انتظارات مشتری، ایجاد روابط بلندمدت و وفاداری است.
جریان ارزش (Value Streams)
تولید ناب رویکردی جامع برای تجزیه و تحلیل کل چرخه عمر یک محصول یا خدمت، از ایده اولیه تا از رده خارج کردن، در پیش میگیرد. با ترسیم جریانهای ارزش و بررسی دقیق تک تک مراحل فرایند، سازمانها بینش ارزشمندی در مورد زمینههای ناکارآمدی و اتلافها به دست میآورند. این امر به آنها امکان میدهد تا گردشکارها را سادهسازی کنند، فعالیتهای بدون ارزش افزوده را حذف کنند و منابع را به شکلی استراتژیک تخصیص دهند. نتیجهٔ این رویکرد، عملیاتی کممصرفتر و کارآمدتر است که زمان، مواد و منابع را بهینه میسازد و در نهایت ارزش بیشتری برای مشتری ایجاد میکند.
جریان یا گردش (Flow)
جریان یا گردش روان و بدون وقفهٔ مواد، اطلاعات و فرایندها، یک اصل اساسی در تولید ناب است. سازمانها میتوانند با حذف گلوگاهها، بهینهسازی توالی تولید و کاهش اختلالات، زمان تامین و تدارک (lead time) را به طور قابل توجهی کاهش و کارایی را افزایش دهند. این جریان سادهشده، محیط تولیدی هماهنگی ایجاد میکند که در آن منابع به شکل مؤثرب مورد استفاده قرار میگیرند و تیمها میتوانند انرژی خود را بر وظایف ارزشآفرین متمرکز کنند. در نتیجه، سازمانها میتوانند به سرعت به تقاضای مشتریان پاسخ دهند، بهرهوری را بهبود بخشند و به برتری عملیاتی دست یابند.
کشش (Pull)
رویههای سنتی تولید به پیشبینیها و تولید مبتنی بر فشار (Push-based) متکی هستند که منجر به تولید بیش از حد و مازاد شدن موجودی میشود. در مقابل، تولید ناب از یک سیستم مبتنی بر کشش (Pull-based) پیروی میکند که در آن تولید با تقاضای واقعی مشتری آغاز میشود. با همگامسازی تولید با تقاضا، سازمانها میتوانند سطح موجودی را به حداقل برسانند، اتلاف را کاهش دهند و پاسخگویی به تغییرات بازار را افزایش دهند. این رویکرد ناب به کسبوکارها امکان میدهد تا به طور کارآمدتری عمل کنند، با نیازهای در حال تغییر مشتریان سازگار شوند و استفاده از منابع را بهینه کنند.
کمال (Perfection)
تولید ناب، دربرگیرندهٔ فرهنگ بهبود مستمر و رسیدن به کمال است. این شیوه، همه کارکنان را از بخش تولید تا مدیران ارشد تشویق میکند تا به طور فعال در حل مسئله، نوآوری و یادگیری مشارکت کنند. سازمانها با تلاش برای بهبودهای تدریجیِ کوچک در فرایندها، محصولات و خدمات، میتوانند به طور مداوم تکامل یافته و با فضای پویای کسبوکار سازگار شوند. تعهد به کمال، سازمانها را به چالش کشیدن وضع موجود، حذف اتلافها و ارائه مداوم ارزش بیشتر به مشتری ترغیب میکند.
درمجموع، تولید ناب در مورد کاهش اتلافها در قالب کارکنان کمبازده، مواد استفادهنشده و فرایندهای بیکیفیت است. هدف از اجرای این روش میتواند دستیابی به رشد بالای درآمد یا ارائه خدمات بهتر به مشتری باشد. و کسبوکارها میتوانند با بهرهمندی از مزایای تولید ناب، به همه این انتظارات برسند.
تولید ناب و حذف ۸ نوع اتلاف
تفکر ناب، هر فرایند یا وظیفهای را که نتواند برای مشتری ارزش ایجاد کند، اتلاف تلقی میکند. برخی اتلافها اجتنابناپذیر هستند. شما نمیتوانید منابع اتلاف ضروری را حذف کنید، اما اصول ناب خواستار آن است که تمام منابع اتلاف غیرضروری را از بین ببرید.
۱. حملونقل غیر ضروری:
حملونقل غیر ضروری میتواند منجر به آسیب دیدگی اقلام در حین جابجایی، ایجاد گلوگاه در جریان تولید و برقراری ارتباط ضعیف شود. یکی از راههای حذف حملونقلهای غیر ضروری، ترسیم مسیر مواد خام و قطعات در سراسر تاسیسات شماست. اطمینان حاصل کنید که جریان مسیر بر اساس محصول باشد، کل مسافت طی شده به حداقل برسد و تیم شما درگیر کارهای بدون ارزش افزوده نباشد.
۲. تولید بیش از حد:
نگهداری مازاد مواد اولیه خوب است، اما تولید بیش از حد میتواند منابع ضروری را تحلیل ببرد، و برای شما ایجاد هزینه کند. تولید ناب خواستار تولید دقیقاً همان چیزی است که مشتری تقاضا میکند.
۳. تحرک و جابهجاییهای غیرضروری:
تحرک و جابهجاییهای غیرضروری و تکراری میتواند بر سلامت و بهرهوری کارکنان تأثیر بگذارد. زمانی که تیم شما احساس راحتی نکند، به احتمال زیاد با محصولات به درستی رفتار نمیکند و در نتیجه مشکلاتی در کیفیت به وجود میآید. سعی کنید وظایف مورد نیاز برای هر فرایند را ترسیم کنید تا منابع خم شدن، کشش، بلند کردن یا راه رفتن غیر ضروری را شناسایی کنید. با اپراتورهای خود صحبت کنید تا نظر آنها را در مورد چگونگی ایمنتر کردن، راحتتر کردن و کارآمدتر کردن کارشان جویا شوید.
۴. اضافه موجودی انبار:
برنامهریزی ضعیف، زمانهای نادرست تغییر خط تولید و فرایندهای نامتعادل تولید، همگی میتوانند منجر به موجودی اضافی در انبار شوند. نگهداری موجودی بیش از حد ضروری، منابع را راکد میسازد و میتواند هزینههای اضافی زیادی به همراه داشته باشد. شما میتوانید با سادهسازی جریان تولید و معرفی سیستم تحویل به موقع (Just-in-Time) برای مواد اولیه، از اضافه موجودی انبار اجتناب کنید.
۵. زمان بیکاری یا انتظار:
زمانی که رویدادهای تولید به طور ضعیفی همگامسازی شوند، زمان انتظار افزایش مییابد. این امر باعث کاهش توان عملیاتی و منجر به بروز هزینههای غیر ضروری میشود. برای رسیدگی به زمان انتظار اضافی، باید ریشهٔ مشکل را پیدا کنید. نگهداری و تعمیرات ضعیف تجهیزات، کمبود ابزار یا عدم ثبات فرایند میتواند باعث ایجاد مشکل شود.
۶. افراط در فرایندها:
شما باید تلاش کنید تا هرگونه کار تکراری که به ایجاد ارزش در محصول شما کمک نمیکند را حذف کنید. نقشه فرایند شما باید کارهای تکراری، غیرضروری یا نامشخصی را که میتواند به اتلاف منجر شود، برجسته سازد.
۷. عیوب:
زمانی که محصولات نتوانند مشخصات لازم را برآورده کنند، باید برای دور ریختن، بازسازی یا تعمیر آنها وقت و هزینه صرف کنید. تولید ناب به دنبال تولید بدون نقص است. تحلیل علل اصلی میتواند به شناسایی دلایل بروز عیوب کمک کند تا بتوانید اقدامات اصلاحی انجام دهید.
۸. استعدادهای بدوناستفاده و کماستفاده:
بهرهگیری ضعیف از استعدادها میتواند منجر به هزینههای نیروی کار اضافی شده و باعث شود تیم شما در رسیدن به اهداف خود با مشکل مواجه شود. نگاشت منظم از استعدادها و گفتگوهای مکرر با کارکنان میتواند به شما در سنجش رضایت آنها و شناسایی موارد کماستفاده از استعدادها کمک کند. سرپرستان همیشه باید به دنبال فرصتهایی برای بهبود فرایندها و بهرهمندی بهتر از استعدادهای تیمهای خود باشند.
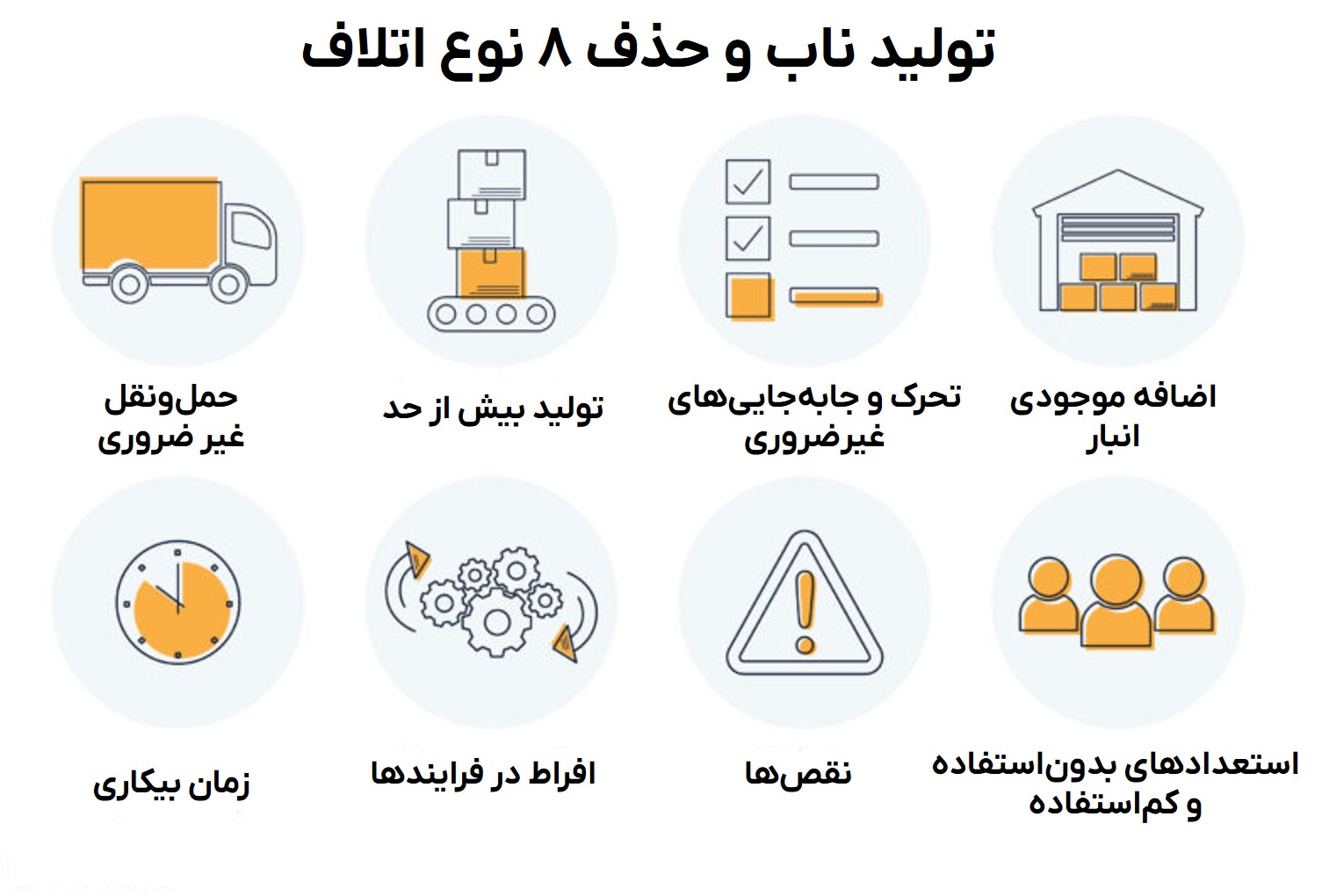
ابزارها و تکنیکهای تولید ناب
با روی آوردن بیشتر و بیشتر صنایع به تفکر ناب، آنها مجموعهای گسترده از ابزارها و تکنیکها را برای اعمال اصول ناب در فرایندهای تولید منحصر به فرد خود توسعه دادهاند. اینها تنها چند مورد از روشهایی است که میتوانید از طریق آنها بهبود فرایند را معرفی کرده و فرهنگ بهبود مستمر را ایجاد کنید:
نظام آراستگی 5S
نظام آراستگی 5S روشی سازماندهی است که به داشتن تاسیسات ایمن و بدون درهمریختگی کمک میکند. بعد از جنگ جهانی دوم، تویوتا به دنبال روشی برای کاهش اتلافها در تاسیسات خود بود. روشی که در این شرکت اجرا و به عنوان سیستم تولید تویوتا شناخته شد، شامل اصولی برای خلق نظمی منطقی در محل کار بود. این اصول بعد از ژاپن در غرب هم مورد استقبال قرار گرفت و به نام نظام آراستگی 5S شناخته شد. علاوه بر جلوگیری از حوادث، این روش باعث افزایش کارایی و بهرهوری میشود.
تعویض تکدقیقهای قالب (SMED)
اگر زمانهای راهاندازی بر روی اثربخشی کلی تجهیزات (OEE) شما تأثیر میگذارد، اجرای SMED میتواند کمک کند. این فرایند شامل تقسیم کردن هر مرحله از فرایند راهاندازی به اجزا میشود. اجزای خارجی مواردی هستند که اپراتورها میتوانند در حالی که تجهیزات در حال کار است انجام دهند. از طرف دیگر، اجزای داخلی مواردی هستند که به خاموشی نیاز دارند. هنگامی که فرایند را تجزیه و تحلیل کردید، اجزای آن را بررسی کنید. با شناسایی فرصتهایی برای انتقال اجزای داخلی به اجزای خارجی، به طور بالقوه میتوانید فرایند را سادهسازی کنید.
کانبان
کانبان که توسط تویوتا در اوایل روزهای تولید ناب توسعه یافته است، به تجسم گردشکارها برای بهینهسازی کنترل کیفیت، تخصیص منابع و بهرهوری کمک میکند.
تکنیک پوکایوکه (Poka-Yoke)
تکنیک پوکایوکه (Poka-Yoke) اصطلاحی ژاپنی به معنای «جلوگیری از اشتباهات سهوی» است. این مفهوم به عنوان یک فلسفه، به معنای شناسایی و اصلاح خطاها در زمان وقوع آنها به جای بازرسی برای آنها پس از وقوع است.
نحوهٔ پیادهسازی تولید ناب
معرفی یک سیستم مدیریت ناب برای عملیات تولید شما، لزوماً به معنای بازنگری کل سازمان شما نیست. تولید ناب فراتر از مجموعهای از ابزار و تکنیکها است؛ باید توجه کرد که تولید ناب یک طرز فکر است.
مراحل زیر میتوانند به شما کمک کنند تا فرایندهای ناب را به دقت و به شکلی استراتژیک برقرار کنید و اصول تولید ناب را در سراسر سازمان خود پیادهسازی کنید:
۱. استراتژی خود را تدوین کنید:
با انتخاب چند فرایند تولید با قابلیت بهبود شروع کنید. برای هر فرایند مجموعهای از معیارها و اهداف مرتبط را توسعه دهید. به طور واضح مشخص کنید که چگونه اصول ناب را به کار میگیرید، چگونه موفقیت را اندازهگیری میکنید و چگونه بر اساس دادههای عملکرد تکرار میکنید.
۲. جریان ارزش را ترسیم کنید:
فرایندهای فعلی خود را تجزیه و تحلیل کنید و منابع اتلاف را شناسایی کنید. سپس، یک نقشه از حالت آینده ترسیم کنید تا آنچه را که دوست دارید ببینید، نشان دهید. سپس، یک برنامه اجرایی برای رسیدن به این حالت آینده تدوین کنید.
۳. محلهای کار خود را سازماندهی کنید:
نظافت و سازماندهی مجدد، یافتن اقلام ضروری و روان نگه داشتن فرایندهای کلیدی را آسانتر میکند. این همچنین تیم شما را ایمنتر نگه میدارد!
۴. جریان فرایند خود را مرور کنید:
گلوگاهها و اتلاف را در جریان فرایند خود شناسایی کنید. سپس، طراحی فرایند را برای تسهیل بهبودها تغییر دهید.
۵. هدفگذاری بر زمان توقف فرایند:
علل توقف فرایند ممکن است شامل اعمال تغییرات، خاموشی فرایند برای انجام نگهداری و تعمیرات دورهای، زمان انتظار یا خرابی تجهیزات باشد. این علل بالقوه را تجزیه و تحلیل کنید و یک فرایند تکرارشونده برای اصلاح آنها تدوین کنید.
۶. اجرای سیستم کششی:
تنها تقاضای ایستگاه فرایند و تقاضای مشتری را محرک جریان مواد خود قرار دهید.
۷. سطحبندی گردشکارها:
برای تدوین یک حجم کاری متعادل که در آن مقادیر تولید متوسط با نیازهای مشتری مطابقت دارد و در عین حال از فراز و نشیبها جلوگیری میکند، تلاش کنید.
۸. فرایندهای کاری خود را استاندارد کنید:
در کنار کارکنان خود، بهروشها را با مستندات و رویههای عملیاتی استاندارد (SOP) مناسب تدوین کنید.
۹. فرایندهایی برای بهبود مستمر معرفی کنید:
تیم خود را در مورد ارزش بهبود مستمر آموزش دهید و شروع به معرفی فرایندهایی برای ترویج آن کنید.
۱۰. با تامین کنندگان و مشتریان خود مشارکت کنید:
با تامین کنندگان و مشتریان خود برای نابتر ساختن کل زنجیره تامین خود همکاری کنید.
به خاطر داشته باشید که بهبود تدریجی اساس تولید ناب است. شما نیازی نیست که فرایندهای خود را یک شبه برای ایجاد یک محیط تولید نابتر بهینه کنید.
مزایای تولید ناب برای کسبوکارها
تولید ناب مزایای متعددی را ارائه میدهد که میتواند تأثیر قابل توجهی بر کسبوکارها داشته باشد. در ادامه به برخی از مزایای کلیدی اشاره کردهایم که کسبوکارها میتوانند از طریق اجرای تولید ناب تجربه کنند:

۱. کاهش هزینهها:
با شناسایی و حذف اتلافها در کل فرایند تولید، تولید ناب به کسبوکارها کمک میکند تا هزینههای مرتبط با مازاد موجودی، تولید بیش از حد، نقصها، حملونقل و زمان انتظار را کاهش دهند. بنابراین، عملکرد مالی را بهبود بخشیده و سودآوری را افزایش میدهد.
۲. بهبود بهرهوری عملیاتی:
اصول ناب، باعث بهبود مستمر و حذف گلوگاهها در فرایندها میشود. کسبوکارها میتوانند از طریق کار استاندارد، مدیریت بصری و تولید به هنگام (JIT) برای بهینهسازی استفاده از منابع و سادهسازی گردشکارها، بهرهوری عملیاتی را افزایش دهند، زمان چرخه را به حداقل برسانند و بهرهوری را افزایش دهند.
۳. بهبود کیفیت محصول:
کنترل کیفیت یکی از محورهای اصلی تولید ناب است. کسبوکارها میتوانند با رسیدگی به عوامل زمینهای موثر بر نقصها و اجرای اقداماتی برای بهبود کیفیت محصول، کاهش شکایات مشتریان، برگشت و دوبارهکاری، و ایجاد حسن شهرت، محصولاتی با کیفیت بالا ارائه دهند که انتظارات مشتری یا فراتر از آن برآورده کند.
۴. افزایش انعطافپذیری و پاسخگویی:
تولید ناب انعطافپذیری و چابکی را در فرایندهای تولید ترویج میکند. روشهایی مانند تولید سلولی و آموزش متقابل کارکنان، کسبوکارها را قادر میسازد تا به سرعت با تغییرات تقاضای مشتری و شرایط بازار سازگار شوند. این چابکی به کسبوکارها اجازه میدهد تا به سرعت به نیازهای مشتری پاسخ دهند، از فرصتها استفاده کنند و از رقبا پیشی بگیرند.
۵. کارمندان توانمند و مشارکتکننده:
تولید ناب مشارکت، توانمندسازی و تعامل کارکنان را تشویق میکند. کسبوکارها از طریق آموزش، ابتکارات حل مسئله و فرهنگ بهبود مستمر، دانش و خلاقیت نیروی کار خود را به کار میگیرند. کارکنان درگیر در ارائه ایدههای بهتر، نوآوریها و محیط کاری مثبت، باعث افزایش بهرهوری و رضایت کارکنان میشوند.
۶. کاهش زمان تامین و تدارک:
تولید ناب با حذف اتلافها و بهبود جریان، زمان تامین و تدارک را به حداقل میرساند. اجرای سیستمهای کششی و کاهش زمان راهاندازی، به کسبوکارها امکان میدهد تا زمان مورد نیاز برای تبدیل مواد اولیه به محصولات نهایی را کوتاه کنند. این امر به پاسخ سریعتر به سفارشات مشتری، کاهش هزینههای نگهداری موجودی و افزایش کارایی کلی کمک میکند.
۷. بهبود رضایت مشتریان:
تولید ناب با حذف اتلافها و ارائه محصولات باکیفیت، ارزش را برای مشتریان به ارمغان میآورد. کسبوکارها با برآورده کردن مداوم انتظارات مشتریان، میتوانند رضایت و وفاداری آنها را افزایش دهند. مشتریان راضی به احتمال زیاد به مشتریان دائمی تبدیل شده و از کسب و کار حمایت میکنند که به رشد و موفقیت آن کمک میکند.
با پذیرش اصول و روشهای تولید ناب، کسبوکارها میتوانند این مزایا را آشکار کنند و راه را برای بهبود عملکرد عملیاتی، رضایت مشتری و رقابتپذیری در بازار هموار کنند. اکنون که مزایای تولید ناب را درک کردیم، در ادامه، اجازه دهید عمیقتر به بهروشهایی برای اجرای مؤثر تولید ناب بپردازیم.
بهروشهای اجرای تولید ناب
اجرای تولید ناب نیازمند برنامهریزی دقیق و اتخاذ بهروشها برای به حداکثر رساندن اثربخشی است. در ادامه به برخی از بهروشهای ضروری برای اجرا هنگام پیادهسازی تولید ناب اشاره کردهایم:

۱. ایجاد فرهنگ بهبود مستمر
- فرهنگی را پرورش دهید که در همه سطوح سازمان، بهبود مستمر را ارزشمند بداند.
- کارکنان را تشویق کنید تا فرصتهای بهبود را شناسایی کنند، پیشنهاد دهند و در ابتکارات حل مسئله شرکت کنند.
- ذهنیت یادگیری و نوآوری را برای پیشبرد پیشرفت مداوم ترویج دهید.
۲. تعهد و پشتیبانی رهبری
- حمایت و پشتیبانی فعال از ابتکارات ناب، ارائه منابع، آموزش و راهنماییها.
- تعهد به اصول ناب را نشان دهید، تعامل کارکنان را تشویق کنید.
- منابع، آموزش و راهنمایی لازم را برای اجرای موفق ناب ارائه دهید.
۳. آموزش و توسعه کارکنان
- برای مجهز کردن کارکنان به دانش و مهارتهای لازم برای اجرای موثر تولید ناب، بر برنامههای آموزشی سرمایه گذاری کنید.
- در مورد اصول ناب، تکنیکهای حل مسئله، بهینهسازی فرایند و سایر زمینههای مرتبط، آموزش ارائه دهید.
- کارکنان را توانمند کنید تا مالکیت کار خود را بر عهده بگیرند و در بهبود مستمر مشارکت کنند.
۴. ترسیم جریان ارزش
- برای تجسم جریان مواد، جریان اطلاعات و فرایندها، شناسایی اتلافها، گلوگاهها و فرصتهای بهبود، نقشهبرداری کاملی از جریان ارزش را انجام دهید.
- از نقشه جریان ارزش به عنوان الگویی برای اجرای استراتژیهای ناب استفاده کنید.
- از نقشهبرداری جریان ارزش برای بهینهسازی کارایی، سادهسازی عملیات و هدایت بهبود مستمر استفاده کنید.
۵. مدیریت بصری
- از ابزارهای بصری مانند نمایشگرهای بصری، تابلوهای کانبان و علائم بصری برای نمایش اطلاعات لحظهای و شفافیت فرایند استفاده کنید.
- مدیریت بصری امکان نظارت بر عملکرد، شناسایی مسائل و اقدام سریع برای تیمها را فراهم میکند.
- با اجرای تکنیکهای مدیریت بصری، ارتباط، همکاری و پاسخگویی را ارتقا دهید.
۶. تولید به هنگام (JIT)
- اصول تولید به هنگامJIT را برای به حداقل رساندن سطح موجودی و بهینهسازی جریان تولید اجرا کنید.
- برای کاهش اتلافها و حذف تولید بیش از حد، فقط در پاسخ به تقاضای مشتری اقلام تولید کنید.
- با تامین کنندگان برای تحویل به موقع و کارآمد مواد و قطعات هماهنگ کنید.
۷. جریان مستمر
- با حذف یا کاهش وقفهها، زمان انتظار و حرکت غیرضروری، برای یک گردشکار مستمر تلاش کنید.
- ایستگاههای کاری و چیدمانها را برای پشتیبانی از جریان روان و بدون وقفه مواد و اطلاعات طراحی کنید.
- فرایند دستهای را به حداقل برسانید و توالی عملیات را بهینه کنید.
۸. نگهداری و تعمیرات بهرهور فراگیر (TPM)
- برای نگهداری و تعمیرات و کارایی بهینه تجهیزات، شیوههای نگهداری و تعمیرات بهرهور فراگیر یا TPM را اجرا کنید.
- نگهداری و تعمیرات پیشگیرانه منظم را انجام دهید و اپراتورها را برای مراقبت از تجهیزات آموزش دهید.
- کارکنان را برای بهبود عملکرد در ابتکارات بهبود تجهیزات مشارکت دهید.
۹. توانمندسازی و مشارکت کارکنان
- کارکنان را تشویق و توانمند کنید تا در اجرای تولید ناب مشارکت داشته باشند.
- آنها را در حل مسئله، بهبود فرایند و تصمیمگیریها مشارکت دهید.
- فرصتهایی برای همکاری بین عملکردی و به اشتراک گذاری دانش ایجاد کنید.
- برای حفظ انگیزه و مشارکت، مشارکت کارکنان را به رسمیت شناخته و پاداش دهید.
۱۰. تصمیمگیری مبتنی بر داده
- برای به دست آوردن بینش در مورد عملکرد فرایند و شناسایی زمینههای بهبود، دادههای مرتبط را جمع آوری و تجزیه و تحلیل کنید.
- از شاخصهای کلیدی عملکرد (KPIs) برای سنجش پیشرفت و تصمیمگیری آگاهانه استفاده کنید.
- سیستم نظارت و بررسی منظم عملکرد را ایجاد کنید.
تولید ناب و نگهداری و تعمیرات ناب
در ارتباط تولید ناب و نگهداری و تعمیرات ناب رویکرد شما به نگهداری و تعمیرات و رویکرد شما به تولید، دست به دست هم میدهند.
نگهداری و تعمیرات ناب استراتژیای است که هدف آن کاهش ضایعات و ناکارآمدیها در مدیریت داراییهای فیزیکی است. این استراتژی متکی بر کاربرد روششناسی ناب (Lean) در حوزه نگهداشت داراییهای فیزیکی است.
هرچند خیلی از تولیدکنندگان بیشتر بر روی بهینهسازی تولید با استفاده از اصول ناب تمرکز میکنند اما اصول ناب قطعاً در نگهداری و تعمیرات اهمیت بیشتری نسبت به تولید دارد. زیرا اغلب حوزهٔ نگهداشت تجهیزات و داراییهای فیزیکی پاشنهٔ آشیل کارخانههای تولیدی است و هزینههای آن تا ۴۰ درصد از کل هزینههای تولید را دربرمیگیرد.
اتلافها و ناکارآمدیها در نگهداری و تعمیرات به دلیل انبوهی از اقدامات ناکارآمد مانند موارد زیر رخ میدهد:
- نگهداشت افراطی و بیش از حد
- حمل و نقل غیرضروری قطعات
- رفتوبرگشتها به دفتر مرکزی پس از هر کار برای دریافت دستورکارهای جدید
- اتلاف وقت در جستجوی ابزار و قطعات جایگزین
- انباشته شدن دستورکارها به دلیل مدیریت ضعیف موجودیها
- تعویض زودرس قطعات گرانقیمت
- تأخیر و خرابی ناشی از پردازش کند یا پردازش بیش از حد
- صرف هزینههای اضافی برای اصلاح خطاهای سرویس و تعمیر نواقص
استفاده از یک نرم افزار نگهداری و تعمیرات (CMMS) میتواند انتقال به فرایندهای پیشگیرانهتر را تسهیل کند و فرهنگی را ایجاد کند که تفکر ناب را بپذیرد.
مجهز بودن نرم افزار نگهداری و تعمیرات پگاه آفتاب به ماژولهای مدیریت تجهیزات، مدیریت برنامههای نگهداشت، مدیریت درخواستکار و دستورکار، ورک پرمیت، مدیریت گردشکار فرایند، مدیریت منابع انسانی نگهداشت، مدیریت ایمنی، سلامت و بهداشت محیط کار HSE، پروژههای نگهداری و تعمیرات و داشبورد و گزارشهای تحلیلی و همچنین بهکارگیری فناوریهای روزآمدی چون موتور مدیریت فرایند، باعث شده تا این راهکار ابزارهای لازم جهت مدیریت فراگیر، یکپارچه و هدفمند برای نگهداشت ماشینآلات و تجهیزات را فراهم و امکان بهرهمندی از استراتژیهای نوین نت را میسر سازد.