پایش وضعیت تجهیزات دوار و تکنیکهای نوین آن
مقدمه
پایش وضعیت که به اختصار با CM (Condition Monitoring) نشان داده میشود؛ فرآیندی حیاتی در صنعت است که به منظور ارزیابی وضعیت سلامت تجهیزات و پیشبینی قابلیت عملکرد آنها در محیطهای خاص انجام میشود.
وضعیت سلامت آنها حین عملکرد تجهیزات ارزیابی میشود و خرابیهای احتمالی در مراحل ابتدایی شناسایی میشوند. انگیزههای نظارت بر پایش وضعیت (CM) در اتوماسیون صنعتی شامل کاهش زمان توقف تجهیزات، فعالیتهای نگهداری و تعمیرات و خطاهای مرتبط، و همچنین افزایش کارایی انرژی، بازدهی و کیفیت میشود. تشخیصهای پیشبینیکننده مبتنی بر پایش وضعیت (CM) امکان انجام نگهداری و تعمیرات واحد صنعتی با اطلاعات دقیق را فراهم میکند.
نگهداری و تعمیرات مبتنی بر وضعیت (CBM) یا همان نت اقتضایی با استفاده از ارزیابی وضعیت تجهیزات، مزایایی نسبت به نت دورهای یا واکنشی دارد، خصوصاً در کاهش زمان توقفات و هزینۀ جایگزینی تجهیزات. روشهای به کار رفته در ارزیابی سلامت سیستم، به زیرساختهای واحد صنعتی، اهمیت عملیاتی، گردشکار فرآیند و سهولت تعمیر و سرویس تجهیزات وابسته است. در برخی موارد، میتوان با استفاده از تجهیزات پایش وضعیتِ مقرونبهصرفه، نت مبتنی بر وضعیت را به صورت مؤثر انجام داد. به عنوان مثال، به رغم عدم قطعیت اندازهگیریها یا آستانههای فعالسازی خطا با استفاده از روشهای آماری میتوان تعداد نتایج مثبت و منفی کاذب را کاهش داد.
موفقیت سیستم نت مبتنی بر وضعیت (CBM) به هزینه کلی سیستم پایش وضعیت در کارخانه یا واحد صنعتی ما، ترتیب آن و مزایای نسبی آن نسبت به هزینههای عملیاتی و نگهداشت در طول عمر واحد وابسته است. با توجه به این عوامل حتی از نظر اقتصادی CBM باید بهبود عملکرد کلی سیستمها را نیز به همراه داشته باشد.
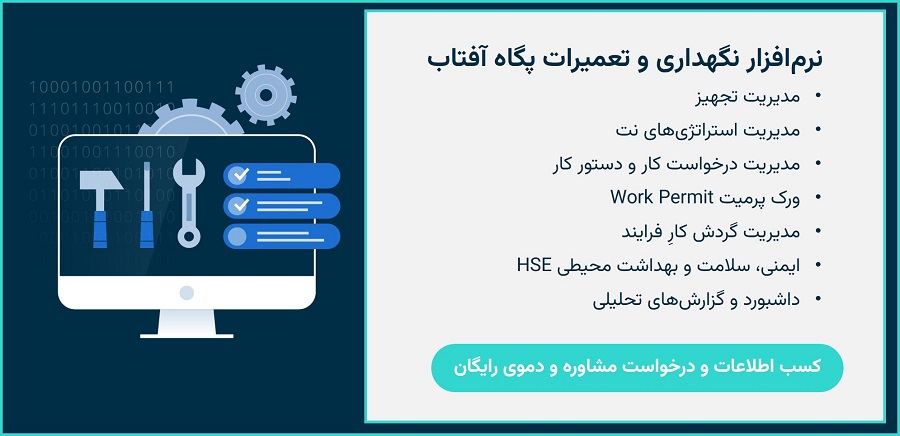
زنجیره زیرساخت در صنایع تولید برق و فرایندهای مشابه معمولاً شامل تولید برق، پست برق الکتریکی، توزیع برق، کنترل فرآیند و تجهیزات عملیات نیروگاه است. اکثر این زیرسیستمها با سیستم کنترل توریع شده (DCS) یکپارچه شدهاند و میتوانند وضعیت سلامت خود را به صورت دورهای منتشر کنند تا برای تشخیصهای پیشبینی کننده مورد استفاده قرار گیرند.
استقرار موفقیتآمیز پایش وضعیت (CM) در صنایع دارای فراوری و پردازش و تولید برق نیز به تحلیل ترکیبی از عوامل مرتبط، مانند ساختاری، تصادفی، منابع، اقتصادی و غیره، وابسته است. ژنراتورها، موتورها، توربینها و سایر ماشینهای الکتریکی دوار معمولاً به تعداد انبوهی در سراسر نیروگاه وجود دارند. نظارت بر ماشینهای دوار توزیع شده مانند موتورهای هوشمند که اطلاعات خطا را به صورت بیسیم ارسال میکنند، ممکن است نیاز به اصلاح شیوههای CM قدیمی داشته باشد.
این مقاله به بررسی تکنیکهای سنتی پایش وضعیت، فعالیتهای اخیر و استقرار ماشینهای هوشمند در یک سیستم اتوماسیون صنعتی میپردازد. این مقاله روند تکامل و روندهای اخیر در مورد ماشینهای الکتریکی دوار، و همچنین مواردی از استقرار پایش وضعیت در عملیاتهای اصلی نیروگاه و جهتگیریهای آینده این فناوری را پوشش میدهد.
روند تکامل پایش وضعیت تجهیزات
یکی از اولین اشارات به پایش وضعیت ماشین آلات را میتوان در سال 1924 توسط واکر یافت. او سیستم اندازه گیری را پیشنهاد کرد که از دادهها و تحلیلهای مبتنی بر تئوری برای تشخیص عیب موتور استفاده میکرد.
از سال 1950 آنالیز ارتعاشات برای تشخیص و پیشبینی وضعیت ماشینآلات شروع شد. در این تکنیک، دادههای ارتعاش جمعآوری و پردازش میشوند تا مشکلات مختلفی مانند عدم تعادل، مشکلات در جریان، مشکلاتروانکاری، رزونانس، مشکلات دنده، لغزش، روغنریزی، مشکلات بلبرینگ و … شناسایی شوند.
این تکنیک به شناسایی خرابی در ماشینآلات کمک میکند تا از خرابیهای ناگهانی و تعویض هزینهبر ماشینآلات جلوگیری شود. هر نوع خرابی در ماشینآلات، الگوی ارتعاش خاصی ایجاد میکند و فرکانس ارتعاش توسط هندسه ماشین و سرعت عملیاتی آن تعیین میشود. از دیگر پیشنهادات مهم در زمینه آنالیز ارتعاشات، بهکارگیری حسگرهای بدون تماس برای کاربردهای پایش وضعیت ماشینآلات بود. این حسگرها به دلیل محدودیتهای فنی در حسگرها، کابلها و جمعآوری داده، محبوبیتی نداشتند.
اندازهگیری تخلیه جزئی که به اختصار PD گفته میشود به منظور تشخیص خرابیهای عایق در ماشینآلات بالاتر از سطح ولتاژ پایین استفاده میشود. تخلیه جزئی که توسط خرابیهای ناشی از نقص در سیستم عایق ایجاد میشود، به عنوان یکی از بهترین نشانگرهای خرابی عایق مورد توجه قرار گرفته است و اطلاعات «هشدار آنی» در مورد خرابیهای عایق را ارائه میدهد که اجازه میدهد قبل از وقوع خرابی ناگهانی اقدامات اصلاحی انجام شود.
در طول دهۀ 1980، تیمپرلی نشان داد که ترکیبی از اندازهگیری «تداخل الکترومغناطیسی» در نول یک ماشین در حال کار و آنالیز طیف وسیع آن، میتواند اطلاعات تشخیصی قابل توجهی را با زمان پیشبینی طولانی قبل از خرابی کامل آن ارائه دهد. این آنالیز میتواند به تشخیص مشکلات داخلی در عایق ماشینآلات کمک کند تا پیش از خرابیهای ناگهانی اقدامات اصلاحی انجام شود.
سیستمهای نظارتی که بدون قطع کار ماشین (به عبارت دیگر، آنلاین) عمل میکنند، اهمیت بسیاری دارند. در واقع، نظارت آنلاین به ما امکان میدهد تا به طور مداوم عملکرد ماشینآلات را پیگیری کنیم و در صورت لزوم اقدامات مناسبی را انجام دهیم.
نظارت آنلاین بر روی ماشینآلات از طریق اندازهگیریهای فرکانس رادیویی (RF) در حالت نول یا خنثی ماشین با استفاده از حسگرهای RF دائمی نصب شده، مزایای مختلفی دارد. پیشرفت فناوریهای مرتبط در دورۀ 2000 تا 2010 در زمینۀ حسگرها، جمعآوری دادههای دیجیتال و یکپارچهسازی تجهیزات ارتباطی، بلوغ روشهای نظارت پیوسته را نشان دادهاند. این تکنولوژیها به ما امکان میدهند تا به طور مداوم عملکرد ماشینآلات را پایش کنیم و از خرابیهای ناگهانی جلوگیری کنیم.
متخصصان تلاش کردهاند ثابت کنند که تشخیص مداوم با بهروزرسانی لحظهای وضعیت ماشینآلات در کل واحد صنعتی، سود کسبوکار را از طریق تصمیمگیریهای آگاهانه در مورد نگهداری و تعمیرات افزایش میدهد. توسعۀ یک سیستم یکپارچه، صنایع را ترغیب به استفاده از نت مبتنی بر وضعیت از طریق ارزیابی پیوسته سلامتی تجهیزات در سراسر واحد صنعتی کرده است.
در طول سه دهه گذشته، به دلیل اهمیت آن در رابطه با ایمنی کارخانه و بحرانی بودن ماموریت، فناوریهای پایش وضعیت تجهیزات به طور پیوسته رشد کرده است. روشهای پایش بالغ شدهاند که منجر به استفاده از سیستمهای CM قابل اعتماد برای پیشبینی خطا، تشخیص و شناسایی محل خطا برای انواع مختلف ماشینهای دوار در زنجیره حیاتی سیستم واحد صنعتی شده است.
عمر طولانی، هزینه کم و نشانگرهای اخطاردهندهٔ مناسب، برخی از مهمترین جنبههای تکامل سیستمهای پایش وضعیت هستند. عوامل تاثیرگذار در این تکامل به شرح زیر هستند:
- نگهداری و تعمیرات کارآمد و عملکرد مؤثر: تشخیص دقیق عیوب ناشی از خرابیهای ابتدایی با مهلت کافی، بهبود کارایی و کاهش هزینههای نگهداشت را تحت تاثیر قرار میدهد.
- حداکثر ساختن سودآوری کلی: فناوریهای نظارتی باید کمهزینه باشند؛ تا جایی که با بهبود بیشتر کیفیت نظارت هزینههای آن نیز کاهش یافته است.
- ساختن کسبوکاری پایدار: که بر اساس سیستمهای پایش وضعیت قابل اعتماد ساخته شده است و عمر خدمت آن با تجهیزات پایششده برابر است و در عین حال هزینه کل عملیاتی کمتری دارد.
تصویر ۱ نشاندهندۀ روند فناوریهای پایش وضعیت است که در طول سالها با توجه به عملکرد چرخۀ عمر واحدهای صنعتی تکامل یافتهاند.
چرخه عمر واحد صنعتی شامل پنج مرحله مهم است: 1. برنامههای نگهداشت و خدمات: برای توسعه بخشیدن استفاده از پایش وضعیت در واحد 2. راهاندازی: برای استقرار برنامههای پایش و مانیتورینگ 3. مهندسی: برای پیکربندی و تنظیم عناصر سیستم با یکدیگر 4. عملیات: تنظیمات نمای رابط انسان-ماشین (HMI)، تعیین آستانهها و تولید اقدامات مرتبط با نگهداشت 5. فعالیتهای نگهداشت و خدمات: نگهداری و تعمیرات تجهیزات اصلی نیروگاه در شرایط سالم و دقیق.
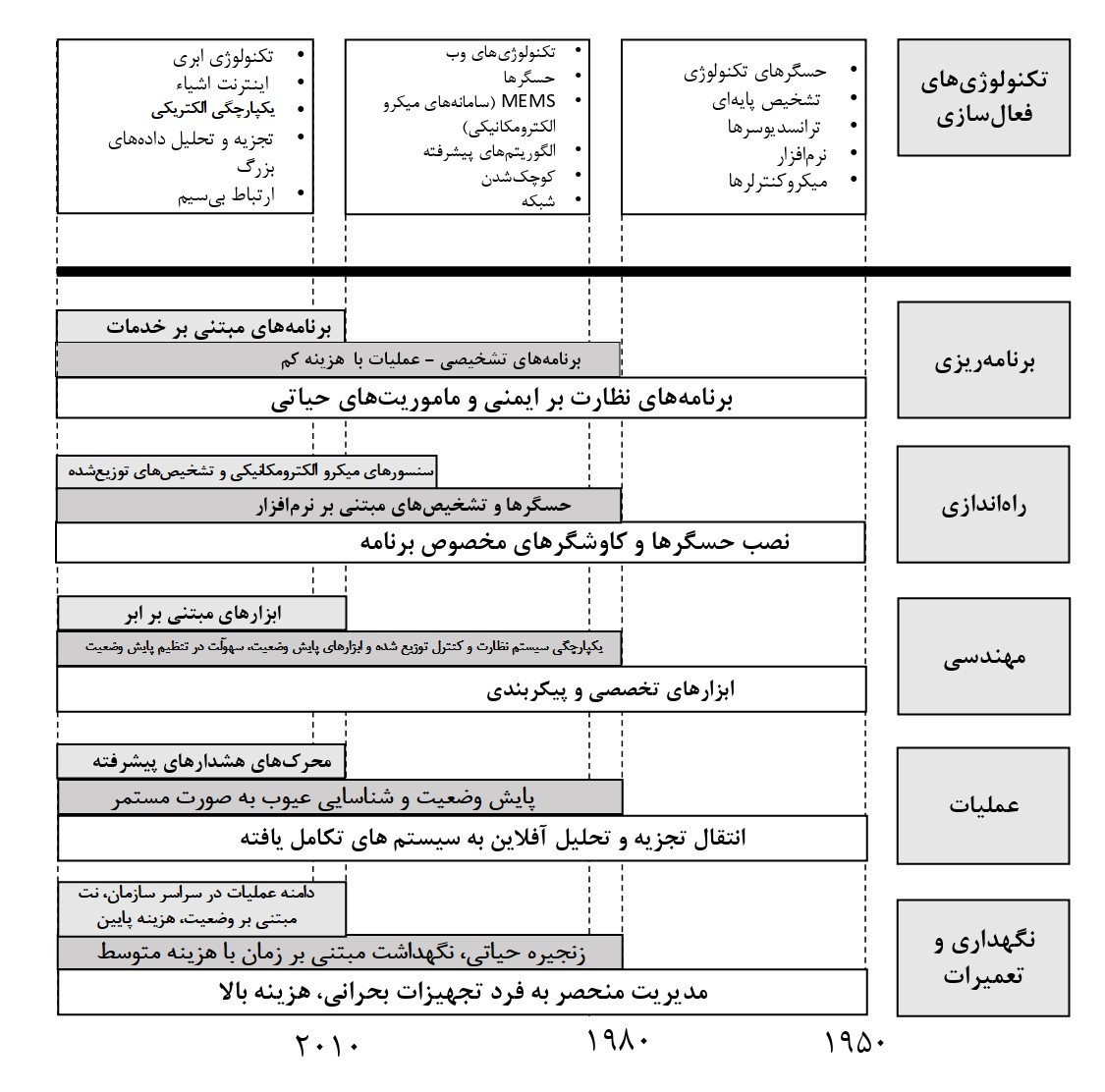
هر مرحله دارای چالشهای فنی خود برای استفاده از راهکارهای پایش وضعیت در دستگاههای الکتریکی دوار است.
در مرحله برنامهریزی، انتخاب برنامههای پایش وضعیت و تشخیصی بر اساس نیازهای نهایی کاربر انجام میشود. کاربردهای تشخیصی در ماشینها و تجهیزات دوار به طور عمده بر روی تشخیص خرابیهای بلبرینگ و عایق با استفاده از سنسورهای حرارتی، ارتعاشی، صوتی، مغناطیسی و تخلیه جزئی تمرکز دارند.
یکی از بزرگترین چالشها، شناسایی ترکیب صحیح حسگر و الگوریتمهای تشخیصی مربوطه است که بتواند به طور کامل نیازهای نهایی را برآورده سازد. چالشهای مرتبط با این عناصر، مانند نصب و کالیبراسیون سنسور، جبران خطاهای اندازهگیری، جمعآوری دادهها و قابلیت محاسباتی، با توجه به کاربردهای پایش وضعیت ارزیابی میشوند. به عنوان مثال استفاده از سنسورهای میکرو الکترومکانیکی (MEMS) میتواند هزینهها را کاهش دهد، به شرطی که در طول عمر خدمت دستگاه، پایداری بلندمدت و عملکرد قابل اعتمادی داشته باشند.
در زمان راهاندازی، داشتن یک نصب مناسب برای سختافزار و نرمافزار بسیار مهم است: این شامل نصب یک سیستم اندازهگیری است که شامل سنسورها، نگهدارنده سنسور، واحدهای جمعآوری داده، یک واحد ارتباطی و غیره میشود. پیکربندی سیستم و معماری تأثیر زیادی بر هزینه پایش در هر نقطه دارد. بنابراین، بهینهسازی اندازهگیری، ارتباط و توزیع الگوریتمهای پردازش در سطوح مختلف، جهت تطابق با مشخصات کاربرد نظارت، ضروری است.
در مرحله مهندسی، اصولاً به پیکربندی سیستم برای عملکرد آن پرداخته میشود. بزرگترین چالش در این مرحله، به دست آوردن ابزارهای یکپارچهای است که بتوانند با ابزارهای اصلی سیستم اتوماسیون کار کنند.
فعالیتهای مرتبط با عملیات، عمدتاً به نگهداشت سیستم پایش وضعیت، جمعآوری اطلاعات و اجرای سیستم تشخیص خرابی برای پیشبینی خرابیها مرتبط است. این سیستم به طور مداوم اطلاعات مرتبط با خرابیهای ابتدایی در طول عملیات نیروگاه را بهروزرسانی میکند.
نت اقتضایی (CBM) در اتوماسیون صنعتی به منظور کاهش تلاش و زمان نگهداری تکامل یافته است. چالشها شامل بهینهسازی گردش کار نگهداری و تعمیرات، سیستم اطلاعاتی، نگهداشت به موقع و سرویس تجهیزات هستند. عناصر مختلف در فرآیند نگهداری و تعمیرات در شکل 2 نشان داده شدهاند. بهینهسازی فرآیند شامل کاهش فعالیتهای مرتبط با مدیریت سیستم اندازهگیری، سیستم اطلاعاتی و گردش کار نگهداری و تعمیرات است. همچنین لازم است زمان بین تصمیمگیری در خصوص تعمیر و سرویس یا تعمیر یا تعویض تجهیزات کاهش یابد، که به اندازه کافی برای توجیه سرمایه گذاری در پایش وضعیت کارآمد باشد.
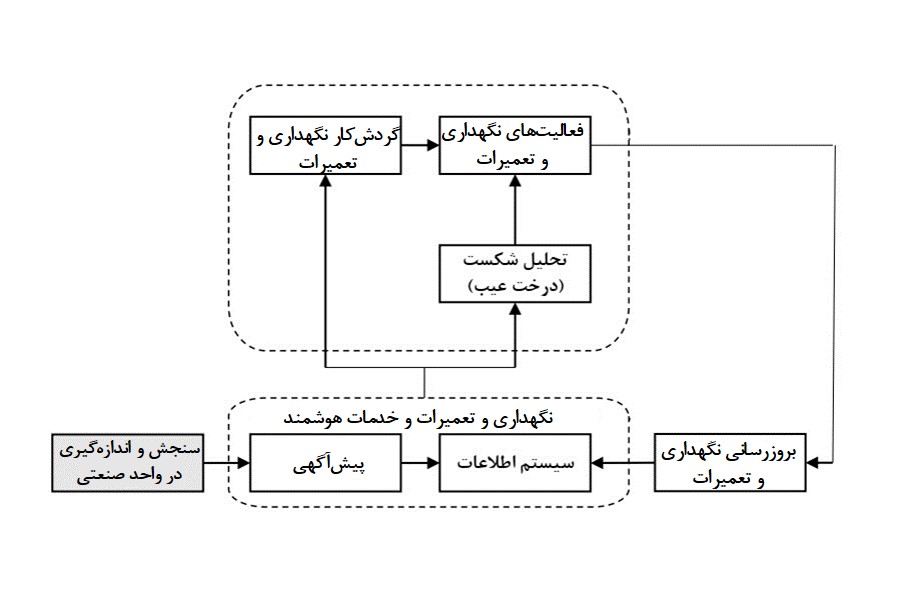
مدلهای کسب و کار برای پایش وضعیت از پایش انتخابی تجهیزات به تشخیصهای کلیه زیرسیستمهای وابسته در واحد، یعنی ناوگان ماشینآلات سراسر واحد صنعتی، تکامل یافته است. تصمیم در مورد استفاده از یک سیستم پایش وضعیت در واحد صنعتی یا کارخانه اغلب بر اساس تعادل بین ریسکهای مرتبط با خرابی تجهیزات و تعداد نقاط کنترل گرفته میشود. روندهای اخیر نشان میدهد که تجزیه و تحلیل توابع پایش با کنترل فرآیند ترکیب میشوند، که منجر به توسعه پلتفرمهای مناسب، به ویژه سنسورهای هوشمند و نرمافزارهای کاربردی مرتبط میشود.
تصویر سه یک نمودار جریان فرآیند معمولی برای سیستم نظارت بر دستگاههای کل واحد صنعتی را نشان میدهد. این نوع استقرار نیاز به اندازهگیری چند نقطهای دارد که مقیاس اقتصادی سنسورهای مورد نیاز برای پایش وضعیت دستگاه را تغییر میدهد. اگر دستگاه نظارت شده در زنجیرهی بحرانی تجهیزات قرار داشته باشد، تصمیم برای استفاده از پایش سلامت تجهیز ممکن است آسان باشد؛ اگر نه، هزینه برای هر نقطۀ نظارتی باید با توجه به بازده تجاری مرتبط با نگهداری و تعمیرات دستگاه، درآمد خدمات، کیفیت محصول و عملکرد آن توجیه شود.
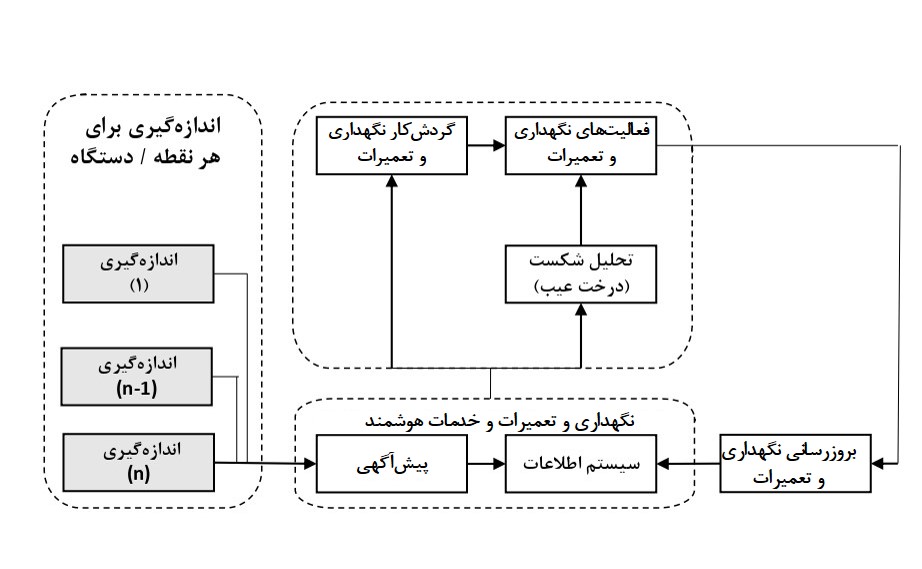
روشهای جدید بررسی عیبیابی در تجهیزات دوار
زمینههای تشخیص خرابی در ماشینآلات الکتریکی شامل:
- یکپارچه سازی سیستم نظارت و کنترل توزیع شده (DCS)
- الگوریتمهای تشخیصی
- الگوریتمهای تشخیصی پیشرفته
۱. یکپارچهسازی سیستم نظارت و کنترل توزیع شده (DCS)
یکپارچهسازی سیستم پایش وضعیت با سیستم نظارت و کنترل توزیعشده (DCS) برای بهبود قابلیت مشاهده و عملیات واحد صنعتی یا کارخانه بسیار حیاتی است. بیایید به انواع رویکردهای یکپارچهسازی که در شکل 4 نشان داده شده است، نگاهی بیندازیم: این یکپارچهسازی میتواند به سه شکل انجام شود: بر بستر تجهیزات، زیرساخت سنتی، و زیرساخت ابری.
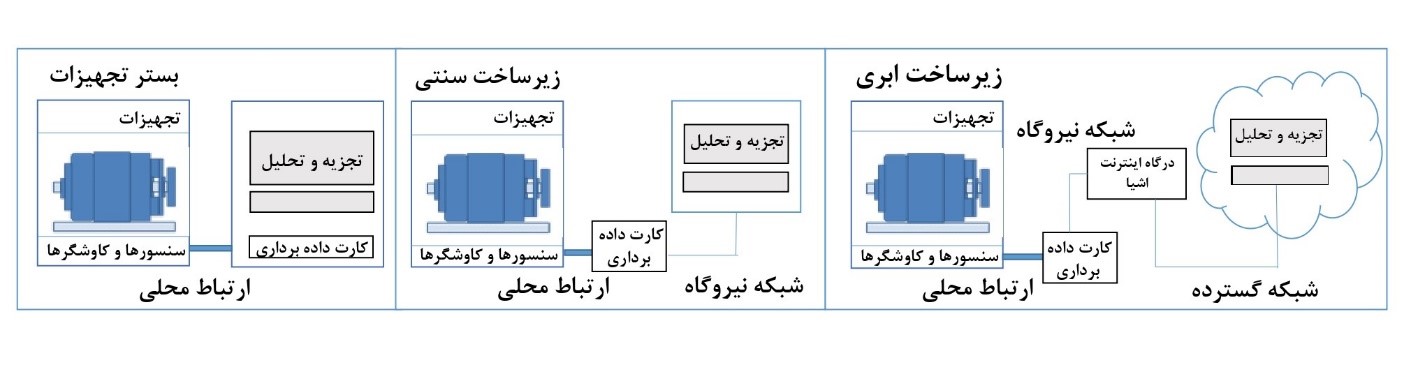
ادغام به صورت زیرساخت سنتی یا (On-Premise Integration) شامل یک واحد جمعآوری داده است که اطلاعات سنسورها را جمعآوری کرده و اطلاعات سنسور را به الگوریتمهای تشخیصی اجرا شده در قسمت عملیات واحد ارسال میکند. به طور معمول، اطلاعات مربوط به تشخیصها از طریق شبکه سازمان منتقل میشود و ممکن است محدودیتهایی در نرخ داده داشته باشد. با این حال، این سیستمها منابع محاسباتی کافی برای الگوریتمهای تشخیصی فراهم میکنند. یکپارچهسازی در زیرساخت ابری یا (On-Cloud Integration) قابلیت انعطافپذیری مورد نیاز برای دادهها و منابع محاسباتی را فراهم میکند. در این رویکرد، یک سیستم ابری اطلاعات پایش وضعیت را جمعآوری کرده و الگوریتمهای تشخیصی پیشرفته را برای تحلیل آفلاین و پیشبینی خطاها فراهم میکند.
پایش وضعیت تجهیزات ممکن است نیاز به منابع مختلفی داشته باشد، از جمله نرخ بهروزرسانی، محاسبات، مکانیزمهای اطلاعرسانی و شروع مجدد. نیازهای تکاملی در زمینه پایش وضعیت و تشخیص خطا عبارتاند از بهبود تشخیص خطا با امکان نوسازی آسان، توسعه روشهای جدید برای تشخیص خطا، تشخیص خطا با استفاده از تکنیکهای جدید، سیستمهای پشتیبانی. تشخیص خطا قبل از وقوع یا توقف کامل در موتورهای القایی برای صنایع بسیار حائز اهمیت است. تشخیص خطا بر اساس تکنیکهای پایش وضعیت و استفاده از یادگیری ماشین دارای پتانسیل زیادی است. الگوریتمهای یادگیری ماشین در زمینه تشخیص خطا در موتورهای القایی یک راهکار مطمئن و موثر برای نت پیشگیرانه فراهم میکنند. این الگوریتمها به تشخیص خطا در مراحل مختلفی از تجزیه و تحلیل دادهها، استخراج ویژگیها و پیادهسازی الگوریتمهای یادگیری ماشین برای تشخیص خطا میپردازند. به عنوان مثال، تشخیص خطا در موتورهای القایی میتواند به عنوان یک مسئله طبقهبندی یا مسئله تشخیص الگو مورد نظر قرار گیرد. از این رو، الگوریتمهای یادگیری ماشین میتوانند ابزارهای قدرتمندی برای حل مسائل تشخیص خطا باشند.
۲. الگوریتمهای تشخیصی
در سال 2003، یک بررسی جامع انجام و گزارش شد تا توسعههای جدید در این حوزه مهم را نشان دهد. این گزارش مزایای بالقوه استفاده از پردازش سیگنال پیشرفته و تکنیکهای هوش مصنوعی در توسعه طرحهای پایش وضعیت را مورد توجه قرار میدهد. تجهیزات دوار معمولاً در محیطهای عملیاتی دشواری اجرا میشوند، با بارگذاری نامنظم و بارگذاری بیش از حد ممکن. اگرچه فرآیندهایی دقیق بر ساخت موتورها حاکم است، هر تلرانس کوچک اما محدود با گذشت زمان منجر به تضعیف روزافزون و منجر به خروج از مرکز، تنش پیچشی و انواع دیگر تنشها روی روتورها، استاتورها، گیربکس و سایر اجزای مرتبط و در نهایت موجب خرابی آن میشود. و حتی فرآیندهای فرسودگی طبیعی اجزای موتور تحت شرایط نامطلوب عملیاتی تسریع میشوند.
اثر تراکم مغناطیسی بین استاتور و روتور باعث هماهنگی کار آنها میشود، و هر نقصی در این کار هماهنگ، به معنای عدم عملکرد صحیح روتورها، به طور مداوم بر روی عملکرد استاتور و بالعکس تأثیر میگذارد. موتورهای القایی به دلیل مقاومت، دوام، قابلیت اطمینان، کارآیی و قیمت پایین، رایجترین موتورهای مورداستفاده در صنعت هستند. در این بخش، موتور القایی به عنوان یک مثال مورد استفاده قرار میگیرد تا توسعههای اخیر در زمینه تشخیص خطا و پایش ماشینها را نشان دهد.
رویکرد مشابهی برای سایر ماشینها برای تشخیص بر اساس پارامترهای خاص آنها، مانند ریپلهای گشتاور ناشی از کموتاسیون در ماشینهای جریان مستقیم (DC)، برای آشکار ساختن ناهنجاریهای مکانیکی و الکتریکی ماشینها، گسترش مییابد. ناهنجاریهای خاص در ماشینهای دوار با بارهای صنعتی به طور کلی در زیر دستهبندی میشوند:
- اتصال کوتاه یا مدار باز بین سیمپیچهای استاتو
- عدم توازن در روتورها
- شکسته شدن نوار روتور یا ترک خوردن حلقههای پایانی روتور
- ناهنجاریهای استاتیک و/ یا داینامیک در شکاف هوا
- تغییر شکل شفت
- اتصال کوتاه در سیمپیچ میدان روتور
- خرابیهای بلبرینگ و گیربکس
- حداکثر بارهای الکتریکی و داینامیک آنها (در تاسیسات برقی)
- حداکثر بارهای مکانیکی و داینامیک آنها (در کارخانههای فراوری)
- مقاومت بین نقاط الکتریکی و مکانیکی(SSR)
پالایش دقیقتر لیست ناهنجاریهای بالا منجر به سه دسته عمده ناهنجاری میشود: ۱. ناهنجاریهای ناشی از عیوب مکانیکی پیشرونده، ناهنجاریهای ناشی از عیوب الکتریکی پیشرونده و در نهایت برهمکنش و همزیستی آنها.
در کاربرد صنعتی، این نوع ناهنجاریها منجر به نت بدون برنامه میشوند که منجر به افت تولید و کاهش بهرهوری کلی میشود. خرابیهای روتور به نظر میرسد که متداولترین خرابیها هستند. بنابراین، توسعهٔ حسگر نظارت بر عملکرد روتور که در محیط محدودی کار میکند، برای استفاده از تکنیکهای پیشرفته بسیار حائز اهمیت است. خرابیهای روتور میتوانند در عملکرد موتور تأثیر بگذارند. این خرابیها ممکن است باعث عدم توازن و مدولاسیون جریان استاتور، داغ شدن، گشتاور و نوسان سرعت، افزایش ضایعات و کاهش گشتاور شوند که منجر به کاهش کارایی میشود.
اندازهگیری جریان استاتور، استخراج سیگناتورهای جریان و تحلیل آن به عنوان روشی برای تشخیص برخی از نقصهای روتور بدون حسگرهای مبتنی بر روتور تکامل یافته است. تجزیه و تحلیل سیگناتور الکتریکی (ESA)، به ویژه تجزیه و تحلیل سیگناتور جریان موتور (MCSA)، در سالهای اخیر برای پایش وضعیت موتورهای الکتریکی به عنوان یک جایگزین کارآمدتر و موثرتر از تکنیکهای سنتی مورد توجه قرار گرفته است. ارزیابی جریان باند جانبی پایین و بالا (در اطراف فرکانس اصلی) ممکن است راهکار خوبی نباشد زیرا کاری دشوار باشد. بنابراین، ممکن است توسعه انواع مختلف تکنیکهای پردازش سیگنال، هوش مصنوعی (AI) و روشهای تخمین پارامتر برای استفاده در برنامههای پایش وضعیت ضروری باشد.
ورودی های چندگانه ولتاژ و جریان، امکان محاسبه و تولید دادهها از جمله جریان بردار فضایی، گشتاور شکاف هوا، توانهای لحظهای مختلف و غیره را فراهم میکند. همچنین تحلیل سیگناتور جریان موتور (MCSA) به وسیلهٔ تکنیکهای تجزیه و تحلیل سیگناتور (امضای) الکتریکی، به ویژه تحلیل سیگناتور جریان برداشته شده از موتور، در سالهای اخیر به عنوان روشی مؤثر برای پایش وضعیت موتورهای الکتریکی مورد توجه قرار گرفته است.
این تکنیکهای جدید به نظر میرسند موثرترین جایگزینها برای تجزیه و تحلیل سیگناتور جریان با استفاده از جریان خطی باشند. استفاده از توان فعال لحظهای برای تشخیص نقص باند روتور در موتورهای القایی سهفاز نشان داده شده است.
سیمپیچهای ثابت استاتور و سیستم عایقگذاری آنها دومین منبع احتمالی برای خرابیها هستند. زیرا تنشهای مختلفی که روی موتور وارد میشوند باعث فرسودگی تدریجی عایق استاتور می شوند. خرابیهای مرتبط با استاتور شامل بروز مدار کوتاه و باز در سیمپیچهای استاتور و خرابیهای هستهٔ مغناطیسی هستند. اتصالی فاز به فاز، اتصالی فاز به زمین و انواع مختلف اتصالی حلقه به حلقه همگی از نتایج خرابی عایق هستند که اغلب به دلیل ترکیبی از افزایش دما، تنش الکتریکی و مکانیکی رخ میدهند. از سوی دیگر، نقصهای مدار باز نسبتاً نادر هستند و خوشبختانه زمان بیشتری برای پیشبینی خرابی در اختیار قرار میدهند.
تحقیقات مختلف در مورد قابلیت اطمینان موتورها در طول سالها انجام شدهاند و گزارشها نشان میدهند که درصد خرابی موتورها ناشی از مشکلات عایقگذاری حدود 26% یا حتی 36% است. خرابی اتصال بین سیمپیچها در نهایت منجر به خرابی کامل سیمپیچ میشود و تاخیر زمانی که در این پیشرفت وجود دارد ناشناخته و به سختی قابل تعیین است؛ بنابراین، ممکن است تکنیکهای تشخیص آنلاین برای شناسایی اولیه خطاهای اتصال بین سیمپیچها مورد نیاز باشد.
تشخیص خطاهای پیچهای استاتور بر اساس تجزیه و تحلیل ارتعاش، نشتی جریان محوری و جریان سرگردان گزارش شده است، و این روشها نیاز به نصب حسگر دارند که ممکن است غیرممکن یا هزینهبر باشد. یک تکنیک غیر تهاجمی بر اساس آنالیز طیفی جریان موتور و دمای سیمپیچها معرفی شده است تا عدم تقارن ماشین را تشخیص دهد. تشخیص خطای اتصال بین سیم پیچها از طریق نظارت بر وجود اشباع باقیمانده شیار روتور و هارمونیکهای ولتاژ ترمینال مرتبط پیشنهاد شده است.
تشخیص خطاهای پیچهای استاتور و روتور بر اساس تجزیه و تحلیل طیفی مورد بررسی قرار گرفته است. به طور خاص، تجزیه و تحلیل مبتنی بر سیگناتور توان فعال و توان واکنشی لحظهای که از جریان و ولتاژ اندازهگیری شدهاند، برای شناسایی خطاهای پیچهای استاتور انجام شده است. این روش به خوبی مشکلات را از نوسانات گشتاور بار و از سایر ناهنجاریها که رفتار مشابهی دارند، تشخیص میدهد. اما در مورد خرابیهای هسته، آنها غیرقابل بازگشت هستند و نیاز به خارج کردن موتور از سرویسدهی دارند.
۳. الگوریتمهای تشخیصی پیشرفته
تحلیل سیگنالهای دیجیتال به عنوان بخشی از تجزیه و تحلیلهای ماشینی، نقش مهمی در تشخیص خرابیها دارد. برای پیشبینی دقیق خرابیها، پردازش سیگنالها نیازمند نرخ جمعآوری دادهها و نرخ بهروزرسانی حسگرها است. روشهای پردازش سیگنالهای دیجیتال برای تشخیص خرابی به سه دستهٔ غیرپارامتری، پارامتری و تحلیل طیف با رزولوشن بالا تقسیمبندی میشوند.
روشهای غیرپارامتری، روشهای کلاسیکی هستند که با تخمین دنبالۀ خودهمبستگی از دادهها شروع میشوند، سپس با استفاده از تبدیل فوریه، طیف توان را تخمین میزنند. تبدیل فوریه سریع (FFT) محاسباتی کارآمد است و میتواند به تولید یک تحلیلگر سیگنال سیگاتور جریان موتور (MCSA) به صورت مفهومی ساده منجر شود.
در مقابل، در روشهای پارامتری، یک مدل فرآیند با استفاده از دانش پیشینی کافی انتخاب میشود و سپس پارامترهای مدل از دادههای فرآیند تخمین زده میشوند. در نهایت، با استفاده از پارامترهای محاسبهشده، تخمینی از طیف توان انجام میشود. مدلهای معمولاً استفادهشده شامل اتورگرسیو یا خودبازگشتی (AR)، میانگین متحرک(MA) و خودبازگشتی میانگین میانگین متحرک (ARMA) هستند. با توجه به اینکه پارامترهای تخمینزدهشده تعداد کمی دارند، انتقال یا ذخیرهسازی این پارامترها به جای مقادیر سیگنال، کارآمدتر خواهد بود. سپس سیگنال از پارامترها بازسازی میشود. با این حال، در برخی کاربردها مانند کارخانههای فولاد و فرآیندهای صنعت سیمان، نقطهی عملیاتی ماشین ثابت نیست. این باعث میشود که سیگنالهای جریان، ولتاژ و توان بسیار پویا و متغیر باشند. چنین سیگنالهای غیر ثابتی با استفاده از تبدیل فوریه کوتاه مدت (STFT) مدیریت میشوند. استفاده از STFT ها و تکنیک های تشخیص الگو برای تشخیص عیوب در موتورهای القایی تحت شرایط کاری متفاوت نشان داده شده است. کاربرد STFT سیگنالهای ثابتی مانند سرعت و بار موتور را فرض میکند که ممکن است در تحلیل ثابت در نظر گرفته شوند.
شناسایی دقیق خطاهای مرتبط با فرکانس میتواند با استفاده از یک بانک فیلتر با پاسخ ضربه محدود (FIR) به همراه تجزیه و تحلیل طیف با رزولوشن بالا انجام شود. این روش معادل تجزیه و تحلیل مقدار ویژه ماتریس خودهمبستگی سیگنالهای جریان موتور در طول زمان است. روش پیشنهادی یک بانک فیلتر FIR را با تجزیه و تحلیل طیف با رزولوشن بالا بر اساس طبقهبندی چندگانه سیگنال ترکیب میکند تا شناسایی دقیق خطاهای مرتبط با فرکانس را انجام دهد. نتایج نشان میدهد که این روش قابلیت تشخیص قطعی را دارد و برای تشخیص ویژگیهای متعددی از فرکانسهای مرتبط با خطا مناسب است. به عنوان مثال، بانک فیلترهای میانگذر، جریان و ارتعاش اصلی را به باندهای مرتبط با خطا تفکیک میکند. سپس تجزیه و تحلیل طیف با رزولوشن بالا به هر باند اعمال میشود تا شناسایی دقیق خطاهای مرتبط با فرکانس انجام شود که حضور خطاهای تکی یا ترکیبی را تشخیص میدهد.
یک نکته مهم دیگر، تحلیل موجک برای تشخیص خطا است. در حالی که STFT برای تجزیه و تحلیل سیگنالهای غیر ثابت در یک پنجره سیگنال کوتاه استفاده میشود، تحلیل موجک به صورت همزمان در سیگنالهای غیرثابت استفاده میشود: به این صورت که از یک پنجرهٔ بزرگتر برای تخمین دینامیک سیگنال ثابت استفاده میشود و در عین حال از یک پنجره کوچکتر برای گذراها یا ترنزیتها (transient) استفاده میشود. این دیدگاه چند مقیاسی یا چند سطحی از سیگنال، اساس تحلیل موجک را تشکیل میدهد. سیگنالهای غیر ثابت نیز از ترنزیتهای جریان شروع در موتورهای القایی نشأت میگیرند. تجزیه و تحلیل موجک تشخیص خطاها را تحت شرایط بدون بار با استفاده از جریان شروع گذرا موتور ممکن میسازد.
تبدیل موجک تحلیلی (AWT) یک الگوریتم دیگر است که قادر به تشخیص و ردیابی فرکانسهای خطا میباشد. تشخیص تاج موجک تحلیلی دامنه کوچک سیگنالها در فرکانسهای خطا را ثبت میکند، در حالی که اطلاعات فاز از AWT پیچیده، پیگیری سیگنالهای خرابی واقعی مانند جریان معیوب استاتور را تسهیل میکند. مثال دیگری از استفاده از AWT میتوان در موتورهای DC بدون تسمه (BLDC) یافت که برای تشخیص و پیگیری فرکانسهای خطا مانند انحراف دینامیکی روتور تطبیق داده شده است.
یک الگوریتم کارآمد دیگر ترکیب تحلیل موجک و تکنیکهای چگالی طیفی توان (PSD) است. این رویکرد در تشخیص خطاهای مشابه انحراف موتور از مرکز و شکستگی میلههای روتر محبوب است.
الگوریتمهای تشخیصی رایج که از موجکها و امضای خطا در باند فرکانسی استفاده میکنند، با فرکانس تغذیه (برق ورودی) تداخل دارند. برای آشکارسازی دقیقتر خطا، میتوان از تکنیک میانگینگیری همزمان با زمان (TSA) همراه با تبدیل موجک گسسته (DWT) استفاده کرد. به طور کلی، TSA مؤلفه قطعی (تغییرناپذیر) را از سیگنال استخراج میکند. همچنین نشان داده شدهاست که قابلیت اطمینان تشخیص خطا به تابع موجک وابسته است.
۴. روشهای تشخیص عیوب ماشین آلات با استفاده از هوش مصنوعی
روشهای تشخیص هوش مصنوعی مبتنی بر الگوریتمهای یادگیری شامل شبکههای عصبی مصنوعی (ANN)، منطق فازی (FL)، سیستم استنتاج عصبی فازی، و الگوریتم ژنتیک (GA)، دومین مجموعه از تکنیکهای موسوم به مستقل از مدل در پایش وضعیت را ارائه میدهند. این مدلها دینامیک و کنترل سیستم مورد نظر را توصیف نمیکنند، بلکه سیستم را به عنوان یک نقشه دارای ورودی-خروجی مشاهده میکنند.
میتوان با استفاده از شبکههای عصبی مصنوعی (ANN)، خطاهای ناهمترازی شکاف هوا و شکستگی میله روتور را تشخیص داد. در این روش، ANN با سه لایه و الگوریتم یادگیری لونبرگ-مارکوارت آموزش داده میشود و از سیگنال ورودی ارتعاشی فیلتر شده استفاده میکند. شبکهٔ عصبی مصنوعی آموزشدیده با استفاده از مجموعههای شناساییشده از نمونههای آموزشی اعتبارسنجی میشود و با استفاده از خروجی ANN و دادههای نظارتی، باقیماندهها تولید میشوند.
باقیماندهها با توجه به آستانههای باقیمانده تنظیم شده، هشدارها و راهاندازهای خطا را فعال میکنند. به طور مشابه، الگوریتمهای یادگیری مانند تکنیکهای خوشهبندی در ترکیب با ANN استفاده میشوند. علاوه بر این، نشان داده شده است که تکنیکهای مبتنی بر رفتار مورچه، روشهای خوشهبندی مشابه خوشهبندی K-means را برای معیار ارزیابی پیادهسازی میکنند. شبکههای عصبی تابع پایه شعاعی (RBF) و نقشههای خودسازمانده (SOM) دو رویکرد مختلف برای تشخیص خطاها در سیستمها هستند و اجازه میدهید که به طور خودکار معماری شبکه مناسب را بر اساس دادههای ورودی طراحی کنند. همچنین، نورون RBF به طور طبیعی نه تنها از تشخیص خطا پشتیبانی میکند، بلکه شدت آن را نیز میتواند تشخیص دهد.
تکنیکهای مبتنی بر منطق فازی، یکی دیگر از حوزههای هوش مصنوعی هستند که به شکل گستردهای در نگهداری و تعمیرات مبتنی بر وضعیت یا همان نت اقتضایی (CBM) استفاده میشوند. این تکنیکها به تشخیص و پیشبینی خرابیها کمک میکنند. در زیر به برخی از الگوریتمهای هوش مصنوعی که با موفقیت در پیشبینی خرابی ماشین استفاده شدهاند، اشاره میکنیم: سیستمهای استنتاج عصبی – فازی تطبیقی (ANFI)، تبدیل بسته موجک منطق فازی، ماشین بردار پشتیبانی (SVM)، و غیره برخی از الگوریتمهای ساخت هوش مصنوعی هستند که با موفقیت در پیشبینی خطای ماشینآلات و تجهیزات بهکار گرفته شدهاند. ANFIS با آموزش بر روی دادههای تاریخی خرابی، الگوها را یاد میگیرد و خرابیهای آینده را پیشبینی میکند. مدل رشد خرابی میتواند با استفاده از مدل مارکوف مرتبه بالا نمایش داده شود. یک فیلتر ذرات مرتبه بالا از این مدل مارکوف برای پیشبینی تکامل زمانی نشانگر خطا در قالب یک تابع چگالی احتمال استفاده میکند.
تکنیک دیگری به نام منطق فازی موجک (Wavelet Fuzzy Logic) یک رویکرد مبتنی بر منطق فازی است که از مجموعهای از الگوها برای پایش سلامت ماشینآلات استفاده میکند. این الگوها به متغیرهای زبانی نگاشت میشوند و سپس توسط مجموعهای از توابع عضویت به مجموعهای فازی نگاشت میشوند. با استفاده از مجموعه قوانین تعریفشده، میتوان هر مجموعه از الگوهای سلامت تجهیز را به یک یا چند دستهبندی مبتنی بر منطق فازی نگاشت کرد. تکنیک منطق فازی موجک (Wavelet Fuzzy Logic) بهبود دقت در تشخیص و تحلیل خرابیها را ارتقا میبخشد.
تبدیل بسته موجک (WPT) به عنوان یک توسعه از تبدیل موجک، از توابع پایه تعمیمیافته استفاده میکند و از این رو میتواند تفکیکپذیری دلخواه زمان-فرکانس را در تمام نواحی فرکانسی ارائه دهد. تکنیک WPT بهبود قابلیت تجزیه و تحلیل سیگنالها را نسبت به تبدیل موجک ارتقا میبخشد. این امر امکان استخراج ویژگیهایی از سیگنالها را فراهم میکند که ویژگیهای ایستا و غیر ایستا را ترکیب میکند. خروجی WPT توسط بلوک تابعی منطق فازی برای تولید بردار ویژگی استفاده میشود، سپس نرمال شده و به عنوان الگویی از دادههای تجربی ذخیره میشود. این بردار ویژگی سپس نرمالسازی شده و به عنوان یک الگو از دادههای تجربی ذخیره میشود. زمانی که دستگاه در حال کار است، خطا با مقایسه بردار ویژگی استخراجشده از دادههای زمان واقعی با الگوهای ذخیرهشده، دستهبندی میشود. چون تکنیک WPT یک استخراجکننده ویژگی موثر است، میتوان از آن به همراه ماشین بردار پشتیبان (SVM) استفاده کرد. این ترکیب برای تشخیص خرابی، ارزیابی شدت و تشخیص خطاهای ترکیبی با دقت بالا اثبات شده است.