کلمه کایزن از دو کلمه ژاپنی “kai” به معنای تغییر و “zen” به معنای خوب تشکیل شده است. بنابراین، به معنای «تغییر به سوی بهتر شدن» است.
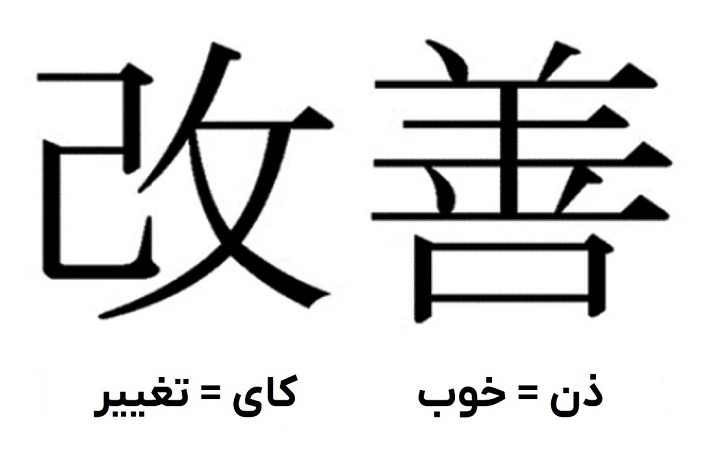
کایزن چیست؟
کلمه کایزن (به ژاپنی 改善) از دو کلمه ژاپنی “kai” به معنای تغییر و “zen” به معنای خوب تشکیل شده است. بنابراین، به معنای «تغییر به سوی بهتر شدن» است.
در حالت عمومی، کایزن معمولاً به معنای اقداماتی برای پیادهسازی بهبود مستمر است.
کلمه کایزن در کل به معنی بهبود است و شامل فرایندهایی بهبود کوتاهمدت و بلندمدت میشود. در تولید ناب، کایزن به معنای ایدهپردازی و اجرای فعالیتهای روزانه به شکلی است که به طور مداوم فرایندها را بهبود میبخشد. این شامل تمام کارکنان میشود، از مدیران ارشد تا کارگران خط تولید.
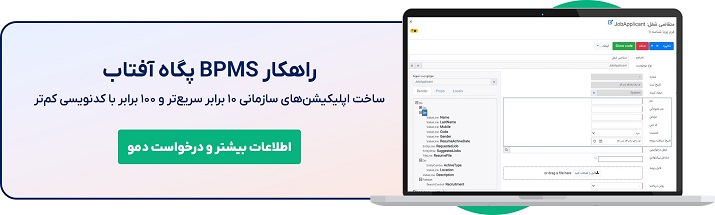
هدف از کایزن، باریک یا بهینه شدن فرایندهای تولید از طریق بهبود فرایندها و برنامههای استاندارد فعلی برای حذف اتلافها و ضایعات و افزایش کارایی است. کایزن گاهی به عنوان بخشی از برنامه عملیاتی و بخشی از یک فلسفه بهبود در نظر گرفته میشود. برنامههای عملیاتی شامل سازماندهی گروههای متمرکز یا تیمها و رویدادهایی است که برای بهبود نواحی خاص در سازمان تعیین شدهاند. تیمها باید شامل کارکنانی از همه سطوح باشند و به شدت بر کارکنان خط تولید تمرکز کنند.
فلسفه کایزن شامل ایجاد فرهنگی کاری است که مشوق مشارکت فعال در پیشنهاد بهبود و استفاده از استانداردهای جدید است. برای اینکه یک شرکت تولیدی واقعاً بهینه شود، این فلسفه باید به شیوه تفکر مدیران ارشد و کارکنان خط تولید تبدیل شود.
شاید اصطلاح «کار استاندارد» را شنیده باشید. کایزن با این مفهوم عهد اخوت دارد. کار استاندارد فرایندهای فعلی یا بهروشها را ترسیم میکند، در حالی که کایزن تلاش میکند تا این فرایندها را بهبود بخشد. کار استاندارد به عنوان سندی زنده دیده میشود که کایزن به طور مداوم آن را بهبود میبخشد. بیایید نگاهی به انواع مختلف کایزن، نحوه رویکرد به پیادهسازی کایزن در فرایندهای موجود و نحوهای که کایزن میتواند با حذف اتلافها، به سازمان شما سود برساند، بیندازیم.
تاریخچه کایزن
استفاده از کایزن به عنوان یک روش یا مفهوم بهبود کسب و کار، پس از جنگ جهانی دوم، تاریخچه اخیر بسیار جالبی دارد.
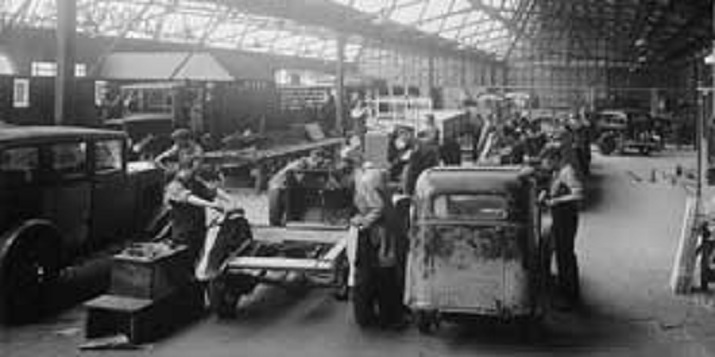
گروه بخش اقتصادی و علمی (ESS)
پس از جنگ جهانی دوم، برای کمک به بازسازی ژاپن، نیروهای اشغالگر آمریکایی متخصصان آمریکایی را برای کمک به بازسازی صنعت ژاپن آوردند. به گروه بخش اقتصادی و علمی (ESS) وظیفه بهبود مهارتهای مدیریتی ژاپنیها محول شد.
فیلم Kaizen eno Yon Dankai
در سال 1951، گروه ESS یک فیلم آموزشی برای معرفی سه برنامه TWI “J” (آموزش شغلی، روشهای شغلی و روابط شغلی) داشت. عنوان این فیلم Lبهبود در 4 مرحله (Kaizen eno Yon Dankai) بود. اینگونه بود که کایزن، به عنوان یک روش یا مفهوم بهبود کسب و کار، به ژاپن معرفی شد.
آموزش درون صنعت (TWI)
رویکرد بهبود کار گام به گام در ایالات متحده تحت برنامه آموزش درون صنعت (TWI Job Methods) توسعه یافت. به جای تشویق به تغییرات بزرگ و رادیکال برای دستیابی به اهداف مورد نظر، این روشها توصیه میکردند که سازمانها بهبودهای کوچک، ترجیحاً آنهایی که میتوانند در همان روز اجرا شوند، را ارائه و اجرا کنند. دلیل اصلی این بود که در طول جنگ جهانی دوم نه وقت و نه منابعی برای تغییرات بزرگ و نوآورانه در تولید تجهیزات جنگی وجود نداشت. جوهرهٔ این رویکرد به بهبود استفاده از نیروی کار و فناوریهای موجود خلاصه میشد.
سهم متخصصان آمریکایی
متخصصان آمریکایی از جمله لوول ملن و دبلیو ادواردز دمینگ در اوایل دهه ۱۹۵۰ به ژاپن آمدند تا به کسبوکارهای ژاپنی در مورد TWI، فرایندهای کنترل آماری و سایر تکنیکهای بهبود مستمر مشاوره دهند. برای معرفی و اجرای پیشگامانه کایزن در ژاپن، امپراتور ژاپن در سال 1960 مدال درجه دوم گنجینه مقدس را به دکتر دمینگ اعطا کرد.
ارتباط بین TWI-Kaizen-TPS-Lean
معرفی برنامه آموزش درون صنعت (TWI) منجر به توسعه کایزن شد که متعاقباً به سیستم تولید تویوتا و در نهایت تولید لاغر تکامل یافت.
رویکرد کایزن
از آنجایی که کایزن به بهبود مستمر میپردازد، صرفاً یک رویداد مقطعی نیست، بلکه یک طرز فکر آگاهانه است که همیشه به دنبال راههایی برای بهبود کارایی است. این رویکرد بهبود مستمر معمولاً به شش مرحله تقسیم میشود:
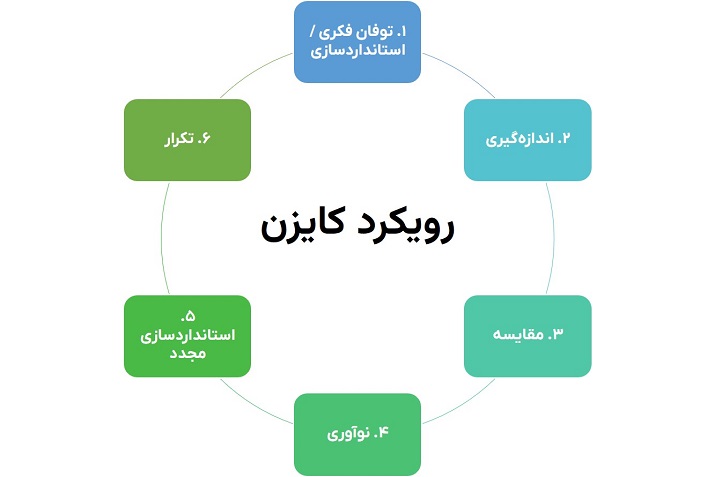
۱. ایدهپردازی/استانداردسازی
با همکاری یک تیم چندوظیفهای، به دنبال ایجاد فرایندهای ساده و تکرارپذیر باشید که فعالیتهای خاصی را بهبود دهند. برای مثال، مؤثرترین روش برای تغییر شیفت را مشخص کرده و هر بار همان روش را اجرا کنید.
۲. سنجش و اندازهگیری
اطمینان حاصل کنید که فرایندها با استفاده از دادههای قابل اندازهگیری کارآمد هستند. برای مثال، انجام یک کار با استفاده از فرایند جدید در مقایسه با روش قدیمی چقدر طول میکشد؟ این یک معیار قابل پیگیری برای اندازهگیری پیشرفت است.
۳. مقایسه
دادههای اندازهگیریشده را با الزامات تعیینشده مقایسه کنید. آیا فرایند جدید در حالی که نتیجه مطلوب را حاصل میکند، موجب صرفهجویی در زمان نیز میشود؟
۴. نوآوری
بهطور مستمر به دنبال روشها و راهکارهای جدید و بهبودیافته برای انجام همان کار و دستیابی به همان نتیجه باشید.
۵. استانداردسازی مجدد
وقتی همه از ایده یا فرایند جدید آزمایششده راضی بودند، آن را تکرارپذیر و بهراحتی قابل اجرا برای همه کنید.
۶. تکرار
این رویکرد را دوباره از ابتدا آغاز کنید.
چند پیشنهاد برای اجرای کایزن با تیم خود:
- ایجاد دفترچه ایده: از تیم خود بخواهید دفترچهای از ایدهها داشته باشند که در آن مواردی را که در طی فعالیتهای روزانهشان متوجه میشوند و به نظر معیوب یا ناکارآمد میآیند و نیاز به بهبود دارند، ثبت کنند. معمولاً وقتی در حال انجام کار هستید، متوجه این مسائل میشوید، نه زمانی که در اتاقی نشستهاید و سعی میکنید آنها را به یاد بیاورید.
- برگزاری جلسات طوفان فکری ماهانه: جلسات ماهانهای برگزار کنید که در آن حوزههای اتلاف در فرایندهایی که تیم شما در حال حاضر استفاده میکند شناسایی شود. دفترچه ایدهها را در اینجا به کار بگیرید و انواع اتلاف (که در ادامه ذکر شده است) را مرور کنید تا ببینید کجا میتوان اتلاف را حذف کرد و چگونه میتوان کارها را بهبود داد.
- ایجاد برنامهای قابل اجرا: برای نحوه پذیرش تغییرات توسط تیم خود (مدیریت تغییر)، برنامهای عملی تدوین کنید. بین انجام سریع تغییرات و صرف زمان بیش از حد برای اجرای ایده که منجر به اتلاف بیشتری میشود، تعادل برقرار کنید.
- تأثیر تغییرات بر دیگران: به این فکر کنید که تغییرات پیشنهادی چگونه ممکن است دیگران را در سازمان تحت تأثیر قرار دهد و قبل از اجرای تغییرات، با آنها مشورت کنید.
کایزن چگونه اتلافها را کاهش میدهد؟
ایده اصلی کاهش اتلاف با استفاده از کایزن بر حذف هفت نوع اتلاف که مانع کارایی میشوند، متمرکز است. در ادامه به بررسی این انواع اتلاف میپردازیم تا بدانید در هنگام بهبود فرایندهای خود باید به دنبال چه مواردی باشید:

۱. تولید بیشازحد
این مورد یکی از جدیترین انواع اتلاف محسوب میشود و میتواند مانند یک اثر دومینویی، باعث بروز دیگر انواع اتلاف شود، از جمله ایجاد موجودی اضافی. برای مثال، داشتن موجودی بیشازحد منجر به هزینههای متعددی میشود، از جمله هزینههای نگهداری، مواد هدررفته، و سرمایهای که بهصورت غیرضروری در موجودی گیر کرده است.
۲. موجودی
موجودی پردازشنشده شامل اتلافهای مربوط به نگهداری، سرمایهای که در موجودی پردازشنشده گیر کرده است، اتلاف ناشی از حملونقل موجودی، محفظههای ذخیرهسازی برای نگهداری موجودی و دیگر هزینههای مرتبط با انبارش میشود.
۳. حرکت
اتلاف حرکت به هر نوع حرکتی، چه از جانب انسان یا ماشین، اشاره دارد که میتوان آن را به حداقل رساند. اتلاف حرکت ممکن است شامل مواردی مانند جستجوی یک ابزار توسط کارکنان یا رسیدگی به خرابی ماشینآلات باشد.
۴. معایب
معایب شامل هر محصولی است که مطابق با استانداردهای طراحی یا انتظارات مشتری نباشد. محصولات معیوب اتلافزا هستند زیرا باید جایگزین شوند، که این امر مستلزم کار و نیروی کار بیشتری است. همچنین ممکن است شرکت مشتریان خود را از دست بدهد. توجه داشته باشید که تمام منابع، مواد و نیروی کار استفادهشده در محصول معیوب نیز هدر میروند زیرا محصول در آن قابل استفاده نیست. در بسیاری موارد، معایب نشاندهنده اتلاف در دیگر بخشهای سازمان هستند که ممکن است علت اصلی ایجاد عیب بوده باشند.
۵. پردازش بیشازحد
پردازش بیشازحد به هر بخش از فرایند تولید اشاره دارد که ضروری نیست. برای مثال، اضافه کردن ویژگیهایی به محصول که احتمالاً استفاده نخواهند شد. به عبارت دیگر، شما بیش از آنچه مشتری نیاز دارد ارزش افزوده ایجاد میکنید.
۶. انتظار
اتلاف ناشی از انتظار را میتوان با مثال خط تولید توضیح داد. اگر یک ایستگاه در خط تولید زمان بیشتری نسبت به دیگر ایستگاهها ببرد، کارکنان ایستگاه بعدی منتظر خواهند ماند. هر زمانی که به دلیل کاهش سرعت یا توقف تولید در یک بخش از زنجیره تولید، اتلاف ایجاد شود، اتلاف انتظار رخ میدهد. در رویکرد کایزن، بهبود کارایی بخشی که باعث تأخیر شده است باید در اولویت باشد.
۷. حملونقل
انتقال مواد از یک موقعیت به موقعیت دیگر بهعنوان اتلاف حملونقل در نظر گرفته میشود، زیرا خود عمل حملونقل ارزشی به محصول اضافه نمیکند. کاهش حملونقل ممکن است به معنای نزدیکتر کردن تسهیلات مربوط به فرایند تولید به یکدیگر یا یافتن روشهای مؤثرتر برای کاهش هزینههای حملونقل باشد. حملونقل به دیگر انواع اتلاف مانند استفاده از منابع و زمان برای جابجایی مواد، استخدام کارکنان یا شرکتهای حملونقل و نیاز به آموزش کارکنان منجر میشود.
۸. استعدادهای استفادهنشده
این شامل هر نیروی کاری است که به طور کامل از تواناییهای او استفاده نمیشود. ممکن است نیروی کاری مهارتها و تخصصهای مورد نیاز را داشته باشد اما نتواند از آنها استفاده کند.
متدولوژیهای کایزن
چهار نوع روش کایزن وجود دارد که شامل کایزن تیان، رویدادهای کایزن، کایکاکو و کاکوشین میشود. در ادامه، هر یک از این روشها به تفصیل توضیح داده شده است:

۱. کایزن تیان (Kaizen Teian)
کایزن تیان به بهبودهای روزانهای اشاره دارد که هر نیروی کار مسئول آن است. هر نیرو کار باید دائماً در تلاش باشد تا فرایندهای کاری و گردش کار مربوط به خود را بهبود دهد. مهمتر اینکه، همه کارکنان، از جمله ناظران و مدیران، باید هر روز بر حذف هشت شکل اتلاف (که در بالا اشاره شد) که توسط کایزن تعریف شدهاند، تمرکز کنند.
۲. رویدادهای کایزن
در حالی که کایزن تِیان به مسئولیتهای روزانه همه کارمندان اشاره دارد، یک رویداد کایزن یک دوره زمانی برنامهریزیشده است که در آن یک فرایند کاری یا وظیفه خاص برای بهبود شناسایی میشود. رویدادهای کایزن رویدادهای متمرکزی هستند که
در آنها مدیریت، سرپرستان و کارکنان خط مقدم برای بهبود یک مشکل از پیش تعیینشده کار میکنند.
در نهایت، رویدادهای کایزن شامل برنامهریزی قبلی بیشتری هستند، در حالی که کایزن تِیان بیشتر در مورد مسئولیتهای روزانه همه کارکنان برای بهبود جریان کار است.
۳. کایکاکو
کایکاکو مکمل کایزن است. هنگام فکر کردن به کایکاکو، به آن مواردی فکر کنید که یک شرکت طراحی مجدد کامل فرایندها یا رویهها را آغاز میکند. این رویدادی است که در آن یک شرکت روشی کاملاً متفاوت برای انجام کارها را اتخاذ میکند. یک مثال جایگزینی فرایندهای کاری زمانبر و کار فشرده با فرایندهای اتوماسیون مانند تجهیزات و ماشینآلات و نرمافزارها است. این حرکت شامل تجزیه و تحلیل عمیق و تمایل به اطمینان از این است که همه سلولهای کاری میتوانند با افزایش تولید هماهنگ شوند.

۴. کاکوشین
هنگام فکر کردن به کاکوشین، به یک پیشرفت فناورانه فکر کنید که نحوه انجام کار را کاملاً تغییر میدهد. یک رویداد کاکوشین یک چرخش و تغییر کامل و بنیادین است. این را میتوان بهترین روش توصیف کرد؛ به عنوان نهاییترین جلسه طوفان فکری که در آن یک شرکت مسیری را به سمت یک فرهنگ جدید و روش جدید انجام کار ترسیم میکند. یک مثال شامل یک شرکت قالبگیری تزریق پلاستیک است که تجهیزات را برای انجام آلیاژهای منیزیم تیکسومولدی تغییر میدهد. این امر میتواند شامل پذیرش چاپ سهبعدی یا فناوری قالبگیری تزریق فلز (MIM) توسط یک شرکت باشد.
مروری بر ۱۲ روش کایزن
اساساً، همه روشهای کایزن برای ایجاد تغییرات کوچک و تدریجی در فرایندها، محصولات و خدمات طراحی شدهاند. در ادامه تعدادی از مهمترین روشهای کایزن آورده شده است:
۱. چرخه PDCA (برنامهریزی-اجرا-بررسی-اقدام)
- برنامهریزی :(plan) هدف و فرایند بهبود را تعریف کنید.
- اجرا (Do): برنامه را به مرحله اجرا درآورید.
- بررسی (Check): نتایج را ارزیابی کرده و تجربیات به دست آمده را تحلیل کنید.
- اقدام (Act): تغییرات لازم را بر اساس درسهای آموختهشده اعمال کنید.
۲. روش 5s
- ساماندهی(Sort – Seiri) : موارد غیرضروری را حذف کنید.
- نظمدهی (Systematize – Seiton): محیط کار را به شکلی مؤثر سازماندهی کنید.
- پاکیزهسازی :(Clean – Seiso) محیط کار را تمیز نگه دارید.
- استانداردسازی :(Standardize – Seiketsu) استانداردهایی برای نظم و پاکیزگی ایجاد کنید.
- انضباط :(Self-discipline – Shitsuke)انضباط و بهبود مستمر را حفظ کنید.
۳. کارگاههای کایزن
رویدادهای سازماندهیشدهای که در آن تیمها گرد هم میآیند تا فرایندها را تحلیل کرده، مشکلات را شناسایی و راهحلها را توسعه دهند.
۴. بازدیدهای گمبا (Gemba Walks)
مشاهده مستقیم محیطهای کاری و فرایندها برای شناسایی مشکلات و یافتن فرصتهای بهبود.
۵. کانبان
استفاده از کارتها برای تجسم فرایندهای کاری و شناسایی گلوگاهها و مشکلات گردش کار.
۶. گروههای کیفیت
گروههای کوچک کاری از کارکنان که بهطور منظم گرد هم میآیند تا مشکلات را بررسی کرده و راهحلهایی ارائه دهند.
۷. رویه های استاندارد عملیاتی (کار استاندارد)
ایجاد رویههای استاندارد برای ارتقای کارایی و یکنواختی.
۸. سیستم آندون (Andon System)
سیستمی بصری که مشکلات موجود در فرایند تولید را برای پاسخ فوری نشان میدهد.
۹. فرایند بهبود مستمر
رویکردی سیستماتیک برای بهبود مستمر فرایندها و محصولات.
۱۰. هوشین کانری (مدیریت اهداف)
روشی برای برنامهریزی استراتژیک، اجرا و نظارت بر اهداف سازمانی.
۱۱. نقشهبرداری جریان ارزش (Value Stream Mapping)
تجسم فرایندها برای شناسایی اتلافها و بهینهسازی جریان ارزش.
۱۲. نگهداری و تعمیرات بهرهور فراگیر (TPM)
رویکردی برای نگهداری و تعمیرات با هدف افزایش کارایی ماشینآلات و کاهش زمان خرابی.
این روشهای کایزن میتوانند بهصورت جداگانه یا در ترکیب با یکدیگر به کار گرفته شوند تا به بهبود مستمر در جنبههای مختلف یک سازمان کمک کنند.
۱۰ اصل کایزن
روش کایزن از ده اصل مشخص پیروی میکند که در زیر شرح داده شدهاند:
- به طور مداوم همه چیز را بهبود ببخشید.
- مفاهیم قدیمی و سنتی را منسوخ کنید.
- هیچ بهانهای را نپذیرید و کارها را انجام دهید.
- به وضعیت موجودِ اجرای روشهای جدید و فرض چگونگی عملکرد آنها، «نه» بگویید.
- اگر چیزی اشتباه است، آن را اصلاح کنید.
- به همه قدرت دهید تا در حل مسئله شرکت کنند.
- طلاعات و نظرات را از افراد متعدد دریافت کنید.
- قبل از تصمیمگیری، پنج بار سؤال «چرا» را بپرسید تا به ریشه اصلی مشکل برسید. (روش ۵ چرا)
- اقتصاددان باشید. از طریق بهبودهای کوچک، پول پسانداز کنید تا پول پسانداز شده را صرف بهبودهای بیشتر کنید.
- به یاد داشته باشید که بهبود محدودیتی ندارد. هرگز از تلاش برای بهبود دست نکشید.
روش کایزن با حذف ضایعات (مودا) در محل کار (گمبا) در جهت کمال تلاش میکند. هدف کایزن، تولید بدون ضایعات از طریق بهبود فعالیتها و فرایندهای استاندارد شده است. مهندس صنایع، تایایچی اوهنو
انواع کایزن و آموزشهای مورد نیاز
انواع مختلفی از کایزن وجود دارد. اصطلاحاتی مانند کایزن نقطهای (Point Kaizen)، رویداد کایزن (Kaizen Event) یا آموزش کایزن (Kaizen Training) از جمله مفاهیمی هستند که بهطور گسترده بهکار برده میشوند.
اصطلاح «نقطه» در «کایزن نقطهای» معنای خاصی دارد. همچنین عبارات قبل از کایزن و بعد از کایزن نیز مفاهیم مشخصی دارند. به هر حال، هنگام تسهیل یک رویداد کایزن، احساسات جدیای دخیل هستند.
کایزن نقطهای (Point Kaizen)
اصطلاح کایزن نقطهای اغلب با رویدادهای مجزا در یک بخش یا شرکت مرتبط است. این فعالیتها برای بهبود مستمر طراحی شدهاند که در آن اصول تولید ناب (Lean Manufacturing) بهکار گرفته میشوند. اصطلاح نقطه توصیفی است، زیرا نواحی که در آنها روشهای ناب به کار گرفته میشوند، غیرمرتبط و جدا از یکدیگر هستند.
برای مثال، ممکن است روشهای ناب در بخش مالی و همچنین در بازاریابی اجرا شوند، اما این دو پیادهسازی ناب هیچ ارتباطی با یکدیگر نداشته باشند.
میتوانید کایزن نقطهای را بهصورت زیر تصور کنید که از هیرانو (Hirano) الهام گرفته شده است.

کایزن خطی
مرحله بعدی در یک اجرای سازمانیافته از روشهای ناب، چیزی است که به آن کایزن خطی (Line Kaizen) میگوییم. در این زمینه، «خط» به گسترش سازمانیافته ناب از نقطه یا فرایندهای مجزا به خط اشاره دارد. برای مثال، ممکن است کایزن در یک فرایند (نقطه) اعمال شود، اما همچنین در فرایند پاییندستی نیز اجرا گردد. این دو نقطه یک کایزن خطی را تشکیل میدهند.
یک مثال از این حالت میتواند اجرای روشهای ناب در بخش تأمین و همچنین در بخش برنامهریزی باشد. در این مثال، برنامهریزی بالادستی بخش تأمین قرار دارد و کایزن در این دو نقطه اجرا میشود؛ بنابراین این حالت یک خط محسوب میشود.
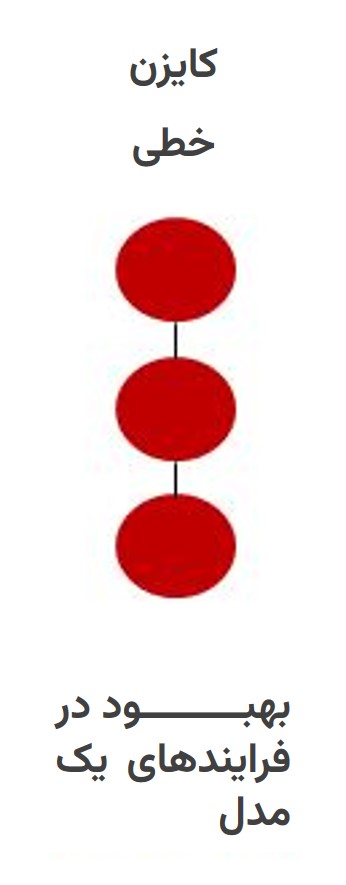
کایزن صفحهای
مرحله بعدی بلوغ در این مدل، اتصال چندین خط به یکدیگر است که به آن کایزن صفحهای (Plane Kaizen) میگوییم. در اصطلاحات مدرنتر، این مفهوم ممکن است بهعنوان جریان ارزش توصیف شود. در این حالت، بهجای ساختار سنتی بخشها، شرکت به خانوادههای محصول و جریانهای ارزش سازماندهی میشود.

کایزن مکعبی
در نهایت، طبق این مدل، ما به کایزن مکعبی (Cube Kaizen) میرسیم. کایزن مکعبی وضعیتی را توصیف میکند که در آن تمام نقاط به هم متصل هستند و هیچ نقطهای از دیگری جدا نیست. این وضعیت زمانی اتفاق میافتد که روشهای ناب در سراسر کل سازمان گسترش یافته باشد.
این حالت نشاندهنده گسترش کامل ناب در تمام بخشهای سازمان است و تصویر آن میتواند به شکل زیر نمایش داده شود:

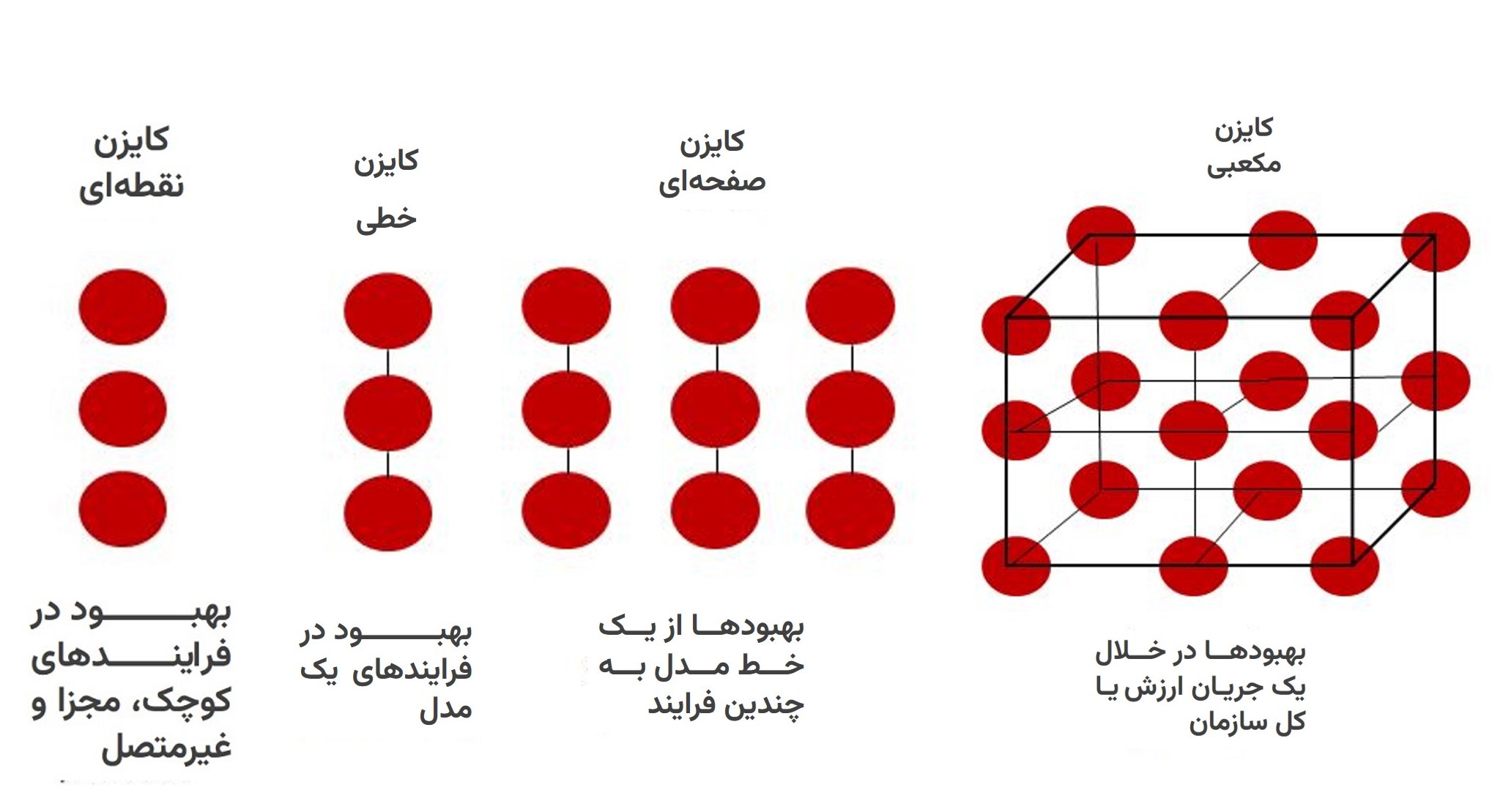
علاوه بر این، میتوانیم این مدل را بر روی یک منحنی بلوغ ترسیم کنیم. همانطور که در تصویر زیر مشاهده میکنید، بسیاری از شرکتها درگیر کایزن نقطهای هستند، اما با پیشروی در امتداد سطح بلوغ، تعداد شرکتها کمتر و کمتر میشود، بهویژه هنگامی که از کایزن نقطهای به کایزن خطی، سپس به کایزن صفحهای، و در نهایت به کایزن مکعبی حرکت میکنیم.
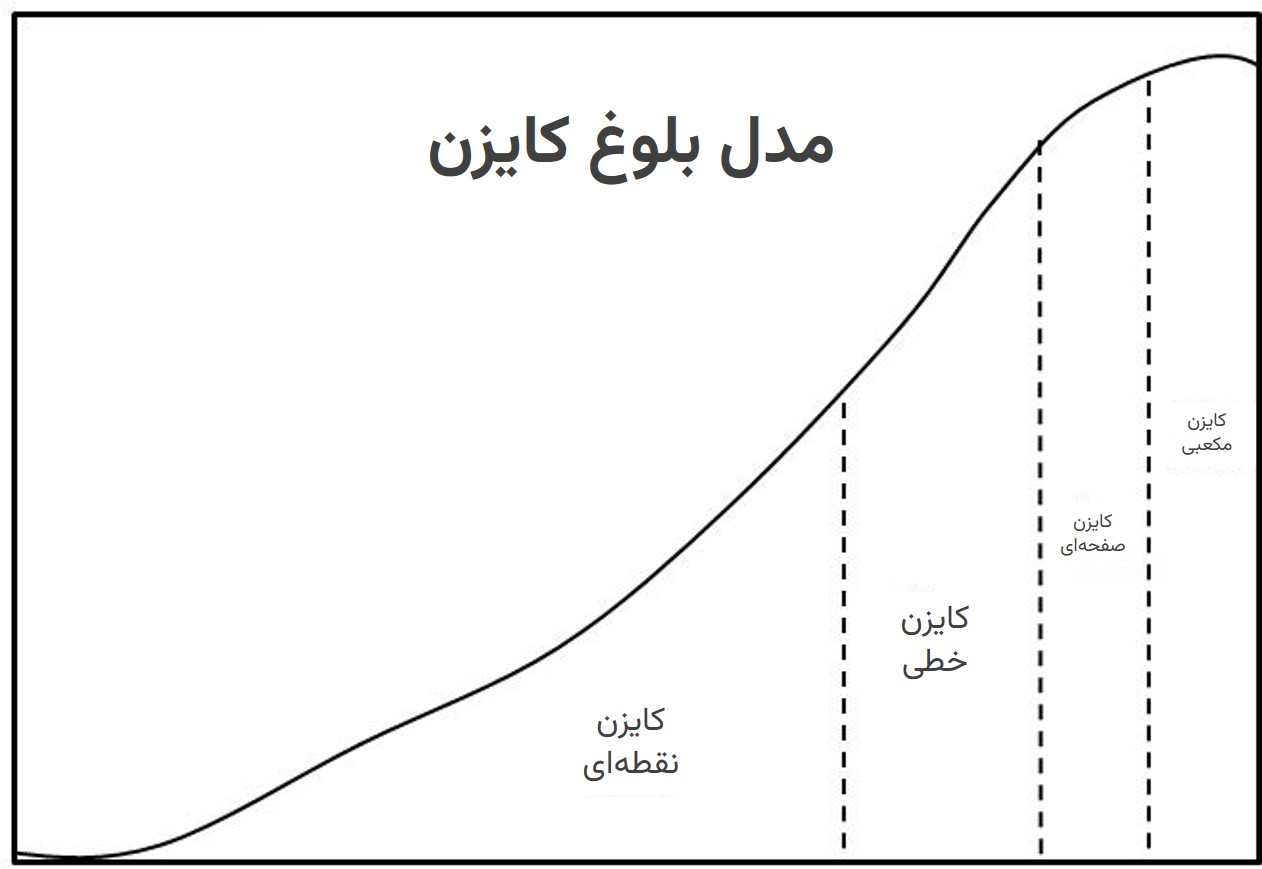