ارزیابی قابلیت سرویس دهی (FFS) مجموعهای از روشها است که از دادههای کمّی برای اینکه مشخص کند، آیا یک قطعه تخریبشده میتواند تحت پارامترهای عملیاتی فعلی به کار خود ادامه دهد یا خیر، استفاده میکند. همچنین از این مفهوم برای تعیین عمر مفید باقیمانده آن قطعه استفاده میشود. نمونههایی از این موارد در این مقاله ارائه شده است.
ارزیابی قابلیت سرویس دهی (Fitness For Service) چیست؟
ارزیابی قابلیت سرویس دهی (FFS) روشی استاندارد و بهروشی در صنایع نفت، گاز و فرایندهای شیمیایی است که برای ارزیابی تجهیزات در حال بهرهبرداری و تعیین امکان ادامه استفاده از آنها به کار میرود.
این روش تحلیل میتواند بر تصمیمات مربوط به ادامه کار، تغییر شرایط عملیاتی یا تعمیر قطعات تأثیر بگذارد و برای تجهیزات تحت فشار مانند مخازن تحت فشار، مخازن ذخیرهسازی، لولهها، خطوط لوله و دیگهای بخار کاربرد دارد. این نوع تجهیزات تحت فشار را میتوان تحت عنوان تجهیزات تحت فشار ثابت (یا استاتیک) دستهبندی کرد.
این روش، مبنایی منطقی برای تعیین حد پذیرش نقصها ارائه میدهد و به مهندسان امکان میدهد تا بر اساس استانداردهای پذیرفتهشده مهندسی (RAGAGEP)، بین نقصها و آسیبهای قابلقبول و غیرقابلقبول تمایز قائل شوند.
قابلیت سرویسدهی یک ماده خاص، با انجام یک ارزیابی استانداردشده مشخص میشود. انجام ارزیابی دقیق FFS، بخشی اساسی از مدیریت یکپارچه داراییهای ثابت است و بهعنوان جایگزینی برای استفاده از کد طراحی اولیه مطرح میشود. قابلیت سرویسدهی تجهیزات را میتوان هم از نظر شرایط فعلی و هم از نظر طول عمر باقیمانده آنها در نظر گرفت.
در بسیاری از موارد، تجهیزات حتی با وجود نقصهای جزئی میتوانند به کار خود ادامه دهند، و تعمیر یا تعویض آنها میتواند هزینهای غیرضروری و سنگین باشد. علاوه بر این، برخی از تعمیرات جوشکاری غیرضروری میتوانند بیشتر به تجهیزات آسیب برسانند و حتی خطرات غیرضروری را برای کارکنان ایجاد کنند.

تجهیزات دوار مانند پمپها، کمپرسورها و توربینها از روشهای FFS ارائهشده در این مقاله مستثنی هستند. با این حال، لازم به ذکر است که مرز فشار در تجهیزات دوار در روششناسیهای FFS استاندارد API 579/ASME FFS1 و سایر استانداردهای بینالمللی پوشش داده شده است.
زمانی که یک قطعه از تجهیزات تحت فشار وارد سرویس میشود، احتمالاً دچار نوعی تخریب ناشی از محیط فرایندی میشود. این تخریب ممکن است به دلیل نوع سیال، شرایط جوی خارجی یا بارهای چرخهای و/یا حرارتی رخ دهد.
عامل اصلی ایجاد این تخریب، مکانیزم آسیب (Damage Mechanism) نامیده میشود. توجه داشته باشید که از عبارت مکانیزم خوردگی استفاده نشده است، زیرا همیشه خوردگی باعث آسیب نمیشود. شناسایی مکانیزم آسیب، عاملی حیاتی در انجام ارزیابیهای FFS است، زیرا نوع ارزیابی مورد استفاده و همچنین نرخ تخریب آینده قطعه را تعیین میکند. این موضوع در تعیین عمر باقیمانده قطعه بسیار مهم است.
استاندارد API 579/ASME FFS1 (که به عنوان استاندارد شناخته میشود) رویکردهای فنی و مورد اجماعی را ارائه میدهد تا ضمن حفظ ایمنی، امکان ادامه کار تجهیزات فرسوده را فراهم کند و همچنین میتواند برای بهینهسازی روشهای نگهداری و عملیاتی استفاده شود. این استاندارد یک مرجع عالی است و در سراسر جهان و در بسیاری از صنایع به طور گسترده پذیرفته شده است.

دامنه کاربرد استاندارد API 579/ASME FFS1
روشهای ارزیابی ارائهشده در API 579 میتوانند برای ارزیابی قابلیت سرویس دهی (FFS) و/یا تغییر شرایط عملیاتی (Rerating) تجهیزاتی که بر اساس کدهای زیر طراحی و ساخته شدهاند، استفاده شوند:
۱. کد ASME B&PV کد دیگهای بخار و مخازن تحت فشار، بخش هشتم، قسمت ۱
۲. کد ASME B&PV کد دیگهای بخار و مخازن تحت فشار، بخش هشتم، قسمت ۲
۳. کد ASME B&PV کد دیگهای بخار و مخازن تحت فشار، بخش اول
۴. کد ASME B31.1 Piping کد لولهکشی نیروگاهی
۵. کد ASME B31.3 کد لولهکشی صنایع فرایندی
۶. کد ASME B31.4 Piping کد لولهکشی سیستمهای انتقال نفت و مایعات
۷. کد ASME B31.8 Piping کد لولهکشی سیستمهای انتقال و توزیع گاز
۸. کد ASME B31.12 Piping کد لولهکشی سیستمهای انتقال هیدروژن و مخلوطهای هیدروژن
۹. کد API Std 650 استاندارد مخازن ذخیرهسازی جوشخورده
۱۰. کد API Std 530 استاندارد محاسبات ضخامت پوستههای فولادی برای کورههای صنعتی
این استانداردها و کدها بهطور گسترده در صنایع مختلف مورد استفاده قرار میگیرند و API 579/ASME FFS1 ابزارهای لازم را برای ارزیابی ایمنی و عملکرد تجهیزات طراحیشده بر اساس این کدها فراهم میکند.
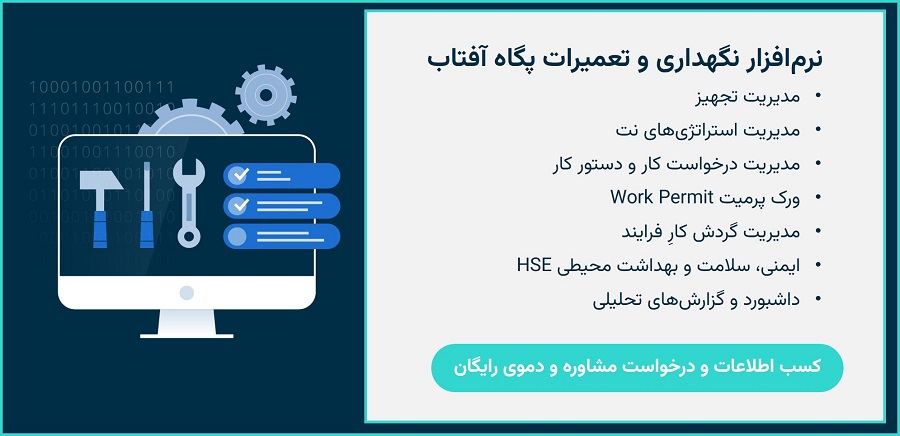
سایر کدها و استانداردهای شناختهشده
روشهای ارزیابی ارائهشده در این استاندارد همچنین میتوانند برای تجهیزات تحت فشاری که بر اساس سایر کدها و استانداردهای شناختهشده، از جمله استانداردهای بینالمللی و استانداردهای داخلی شرکتها ساخته شدهاند، به کار گرفته شوند. این استاندارد کاربرد گستردهای دارد، زیرا روشهای ارزیابی آن بر اساس روشهای تنش مجاز و بارهای فروپاشی پلاستیک برای عیوب غیرترکمانند و همچنین رویکرد نمودار ارزیابی شکست (FAD) برای عیوب ترکمانند است.
از آنجایی که PD5500 و EN13445 هر دو از کدهای بینالمللی شناختهشده هستند، واضح است که روشهای ارائهشده در API 579 برای مخازن تحت فشار ساختهشده بر اساس این کدها نیز قابل اجرا هستند.
API 579 به طور مناسب به ۱۴ بخش تقسیم شده است که هر بخش شامل پیوستهای متعددی است و روشهای ارزیابی را با توجه به نوع آسیب شرح میدهد. مروری بر محتوای این استاندارد در زیر آورده شده است:
- بخش ۱: مقدمه
- بخش ۲: روش ارزیابی مهندسی FFS
- بخش ۳: شکست ترد
- بخش ۴: کاهش ضخامت عمومی فلز
- بخش ۵: کاهش ضخامت موضعی فلز
- بخش ۶: خوردگی حفرهای
- بخش ۷: آسیبهای ناشی از تاولها و HIC/SOHIC
- بخش ۸: ناهمترازی جوش و اعوجاج پوسته
- بخش ۹: عیوب ترکمانند
- بخش ۱۰: خزش
- بخش ۱۱: آسیبهای ناشی از آتش
- بخش ۱۲: فرورفتگیها و خراشها
- بخش ۱۳: لایهلایهشدگی
- بخش ۱۴: آسیبهای ناشی از خستگی
این ساختار جامع و دقیق، API 579 را به یک مرجع ارزشمند برای ارزیابی ایمنی و عملکرد تجهیزات تحت فشار در شرایط مختلف تبدیل کرده است.

سطوح ارزیابی در روشهای API 579
هر روش ارزیابی در این استاندارد دارای ۳ سطح است که با افزایش سطح، میزان محافظهکاری کاهش مییابد. سطح ۳ اغلب نیازمند روش تحلیل اجزاء محدود (Finite Element Analysis FEA) است و به طور طبیعی پیچیدهتر از سطوح ۱ و ۲ میباشد.

سطح ۱: این سطح سادهترین و محافظهکارانهترین روش ارزیابی است و معمولاً توسط بازرسان انجام میشود. با این حال، استاندارد تأکید میکند که تحلیل انجامشده باید توسط یک مهندس تأیید شود. بازرسان باید تجربهای در بازرسی، بررسی یا هر دو، در مورد نوع تجهیزات و فرایند مرتبط با ارزیابی FFS داشته باشند.
سطح ۲: این سطح از ارزیابی پیچیدهتر از سطح ۱ است و ممکن است نیاز به دادهها و محاسبات دقیقتری داشته باشد. این سطح معمولاً توسط مهندسان با تجربه انجام میشود.
سطح ۳: این سطح پیشرفتهترین و کممحافظهکارانهترین روش ارزیابی است و اغلب نیاز به استفاده از تحلیلهای پیشرفته مانند روش تحلیل اجزاء محدود (FEA) دارد. این سطح معمولاً برای موارد پیچیده و بحرانی استفاده میشود و نیازمند تخصص فنی بالایی است.
مسئولیتهای ذینفعان در ارزیابی قابلیت سرویس دهی (FFS)
مالک-گرداننده (Owner-Operator)
- مسئولیت کلی ارزیابی قابلیت سرویس دهی (FFS) را بر عهده دارد.
بازرس
- در برابر مالک گرداننده مسئول است.
- جمعآوری و سازماندهی دادههای بازرسی مورد نیاز برای ارزیابی FFS را انجام میدهد.
- ممکن است ارزیابی اولیه (غربالگری) را نیز انجام دهد (بر اساس API 579 / ASME FFS1 2016).
مهندس
- اکثر انواع ارزیابیها را انجام میدهد.
- مستندات لازم را تهیه میکند.
- دستورالعملهایی برای عملیات آینده (ادامه کار، تعمیر یا تعویض) ارائه میدهد.
مهندس مواد
- شناسایی مکانیزمهای آسیب را انجام میدهد.
- خواص مواد را بررسی میکند.
- پارامترهای رشد آسیب (مانند رشد ترک) را تحلیل میکند.
مهندس آزمونهای غیرمخرب (NDE Engineer)
- تشخیص و توصیف آسیبها را انجام میدهد.
مهندس فرایند
- نیازهای عملیاتی گذشته، حال و آینده را بررسی میکند.
- شرایط عادی و شرایط غیرعادی (اضطراری) را تحلیل میکند.
این تقسیمبندی مسئولیتها اطمینان میدهد که ارزیابی FFS بهطور جامع و دقیق انجام شده و تصمیمات مناسب برای ایمنی و عملکرد تجهیزات اتخاذ میشود.
روش ارزیابی
بخش ۲ از استاندارد API 579/ASME FFS1 روش کلی ارزیابی را تشریح میکند. مراحل زیر برای تمامی ارزیابیها دنبال میشود:
مرحله ۱ – شناسایی عیوب و مکانیزمهای آسیب
- تشخیص عیوب موجود (مانند ترکها، خوردگی، کاهش ضخامت و غیره) و مکانیزمهای آسیب مرتبط.
مرحله ۲ – بررسی قابلیت اجرا و محدودیتهای روشهای ارزیابی FFS
- تعیین اینکه آیا روشهای ارزیابی FFS برای شرایط موجود قابل اجرا هستند و بررسی محدودیتهای آنها.
مرحله ۳ – جمعآوری دادههای مورد نیاز
- جمعآوری اطلاعات لازم از جمله دادههای بازرسی، خواص مواد، شرایط عملیاتی و تاریخچه تجهیزات.
مرحله ۴ – انتخاب روشهای ارزیابی و معیارهای پذیرش
- انتخاب تکنیکهای مناسب ارزیابی (سطوح ۱، ۲ یا ۳) و تعیین معیارهای پذیرش بر اساس استاندارد.
مرحله ۵ – ارزیابی عمر باقیمانده
- تخمین مدت زمانی که تجهیزات میتوانند بهطور ایمن به کار خود ادامه دهند.
مرحله ۶ – تعیین اقدامات اصلاحی
- ارائه راهکارهای مناسب برای تعمیر، تقویت یا تعویض تجهیزات در صورت نیاز.
مرحله ۷ – پایش در حین کار (Inservice monitoring)
- تعیین برنامههای نظارتی برای کنترل وضعیت تجهیزات در طول عملیات.
مرحله ۸ – مستندسازی
- ثبت تمامی مراحل ارزیابی، دادهها، نتایج و تصمیمات اتخاذشده.
این مراحل برای انواع روشهای ارزیابی قابل اجرا هستند و باید بهصورت روشمند و سیستماتیک انجام شوند تا اطمینان حاصل شود که تمام دادههای مورد نیاز جمعآوری شده و فرایند صحیح ارزیابی دنبال میشود. این رویکرد جامع، ایمنی و قابلیت اطمینان تجهیزات را در طول عمر عملیاتی آنها تضمین میکند.
مرحله ۱ – شناسایی عیوب و مکانیزمهای آسیب
اولین قدم در فرایند ارزیابی، شناسایی نوع عیب (حالت آسیب) و علت ایجاد آسیب (مکانیزم آسیب) است. این شناسایی تعیین میکند که از کدام روش ارزیابی باید استفاده شود.
مرحله ۲ – بررسی قابلیت اجرا و محدودیتهای روش ارزیابی
پس از انتخاب روش ارزیابی مناسب، باید قابلیت اجرا و محدودیتهای آن بخش از استاندارد بررسی شود تا اطمینان حاصل شود که تکنیک ارزیابی انتخابشده معتبر است.
مرحله ۳ – جمعآوری دادههای مورد نیاز
موارد زیر باید در مستندات ارزیابی گنجانده شوند:
- دادههای طراحی اولیه تجهیزات
- گزارش دادههای سازنده یا سایر مستندات معادل و مشخصات فنی.
- نقشههای ساخت که جزئیات کافی برای محاسبه حداکثر فشار مجاز کار (MAWP) قطعه دارای عیب را نشان میدهند.
- در صورت نیاز به تغییر شرایط فشار و/یا دما (افزایش یا کاهش)، این اطلاعات باید برای تمامی قطعات مرتبط در دسترس باشد.
- در صورت عدم دسترسی به نقشههای ساخت اولیه، میتوان از نقشههای دقیق با دادههای لازم برای محاسبه MAWP استفاده کرد.
- سوابق بازرسی قطعه در زمان ساخت.
- مشخصات طراحی کاربر (User Design Specification) در صورتی که مخزن بر اساس کد ASME، بخش VIII، قسمت ۲ طراحی شده باشد.
- گزارشهای آزمایش مواد.
- اطلاعات مربوط به دستگاههای تخلیه فشار، از جمله تنظیمات و ظرفیت شیرهای اطمینان و/یا دیسکهای پارگی.
- سوابق تست هیدرواستاتیک اولیه، شامل فشار تست و دمای فلز در زمان تست یا در صورت عدم دسترسی به دمای فلز، دمای آب یا محیط.
- دادههای مربوط به لولهکشی
- لیست خطوط لولهکشی یا سایر مستنداتی که شرایط طراحی فرایند را نشان میدهند.
- توصیف کلاس لولهکشی شامل مشخصات مواد، ضخامت دیواره لوله و رتبهبندی فشاردما.
- نقشههای ایزومتریک لولهکشی به اندازهای که برای انجام ارزیابی FFS لازم است. این نقشهها باید شامل جزئیات کافی برای محاسبه انعطافپذیری لولهکشی باشند، در صورتی که مهندس چنین تحلیلی را برای تعیین MAWP تمامی قطعات لولهکشی ضروری بداند.
- در صورت عدم دسترسی به نقشههای ایزومتریک اولیه، میتوان از نقشههای دقیق با دادههای لازم برای محاسبه MAWP استفاده کرد.
- دادههای بازرسی
- نوع عیب و توصیف آن، شامل تمام دادههای مربوط به اندازهگیری عیب.
- دادههای بازرسی شامل تمام قرائتهای استفادهشده در ارزیابی FFS.
این لیست به هیچ وجه کامل نیست و دادههای مورد نیاز بستگی به نوع عیب تحت ارزیابی دارد. جمعآوری دقیق و کامل این اطلاعات برای انجام یک ارزیابی دقیق و قابل اعتماد ضروری است.
مرحله ۴ – تکنیکهای ارزیابی و معیارهای پذیرش
در این مرحله، سه سطح ارزیابی ارائه میشود. به طور کلی، هر سطح ارزیابی تعادلی بین محافظهکاری، میزان اطلاعات مورد نیاز برای ارزیابی، مهارت پرسنل انجامدهنده ارزیابی و پیچیدگی تحلیل انجامشده برقرار میکند.
سطح ۱ ارزیابی
این سطح، محافظهکارانهترین روش ارزیابی است اما استفاده از آن سادهتر است.
روشهای ارزیابی در این سطح معیارهای غربالگری محافظهکارانهای را ارائه میدهند که میتوانند با حداقل اطلاعات بازرسی یا اطلاعات مربوط به قطعه مورد استفاده قرار گیرند.
ارزیابی سطح ۱ میتواند توسط پرسنل بازرسی یا مهندسی کارخانه انجام شود.
سطح ۲ ارزیابی
این سطح ارزیابی، یک بررسی دقیقتر را ارائه میدهد که نتایج آن دقیقتر از سطح ۱ است.
در ارزیابی سطح ۲، اطلاعات بازرسی مشابه سطح ۱ مورد نیاز است، اما از محاسبات دقیقتری در ارزیابی استفاده میشود.
ارزیابی سطح ۲ معمولاً توسط مهندسین کارخانه یا متخصصین مهندسی با تجربه و دانش کافی در انجام ارزیابیهای FFS انجام میشود.
سطح ۳ ارزیابی
این سطح، دقیقترین ارزیابی را ارائه میدهد و نتایج آن دقیقتر از سطح ۲ است.
در ارزیابی سطح ۳، معمولاً به دقیقترین اطلاعات بازرسی و اطلاعات مربوط به قطعه نیاز است و تحلیل توصیهشده بر اساس تکنیکهای عددی مانند روش اجزاء محدود (Finite Element Method) یا تکنیکهای آزمایشگاهی (در صورت لزوم) انجام میشود.
ارزیابی سطح ۳ عمدتاً برای استفاده توسط متخصصین مهندسی با تجربه و دانش کافی در انجام ارزیابیهای FFS طراحی شده است.
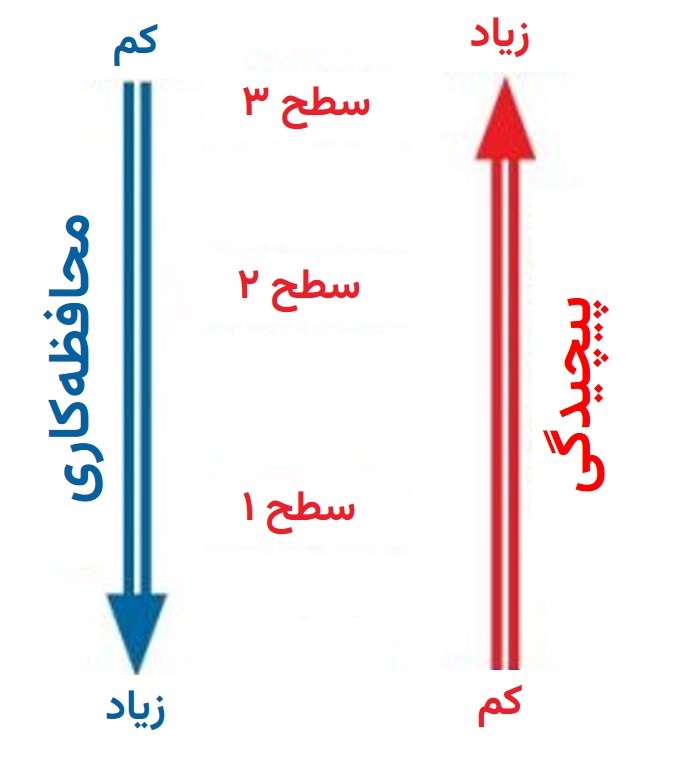
معیارهای پذیرش در ارزیابی قابلیت سرویس دهی (FFS)
روشهای ارزیابی FFS از یک یا چند معیار پذیرش زیر استفاده میکنند:
- تنش مجاز (Allowable Stress)
- عامل مقاومت باقیمانده (Remaining Strength Factor RSF)
- نمودار ارزیابی شکست (Failure Assessment Diagram FAD)
تنش مجاز (Allowable Stress)
مقدار تنش مجاز معمولاً به عنوان کسری از تنش تسلیم، تنش کششی یا تنش گسیختگی در دمای طراحی تعیین میشود و میتواند با حاشیه طراحی مرتبط باشد.
مقادیر تنش مجاز در کدهای طراحی برای محاسبه حداقل ضخامت مورد نیاز دیواره و حداکثر فشار مجاز کار (MAWP) استفاده میشوند.
نسبت تنش مجاز به تنش تسلیم یا کششی در کدهای مختلف متفاوت است، بنابراین لازم است مشخص شود که تنش مجاز بر اساس کد طراحی چگونه تعیین شده است.
عامل مقاومت باقیمانده (Remaining Strength Factor RSF)
روشهای ارزیابی سازهای که از تحلیل تنش خطی با طبقهبندی تنش و معیارهای پذیرش تنش مجاز استفاده میکنند، تنها یک تقریب از بارهایی که یک قطعه میتواند بدون شکست تحمل کند، ارائه میدهند.
عامل مقاومت باقیمانده (RSF) برای تعیین قابلیت پذیرش یک قطعه برای ادامه خدمت استفاده میشود و به صورت زیر تعریف میشود:
RSF = LDC / LUC
تعاریف:
- LDC: حد بار یا بار فروپاشی پلاستیک قطعه آسیبدیده (قطعه دارای عیوب).
- LUC: حد بار یا بار فروپاشی پلاستیک قطعه سالم (بدون عیوب).
معیارهای پذیرش:
- فشار مجاز کاهشیافته (Reduced MAWP) برای قطعه (با کسر فشار استاتیک در صورت لزوم) باید با فشار طراحی (DP) یا MAWP تجهیزات مقایسه شود.
- اگر فشار مجاز کاهشیافته ≥ فشار طراحی یا MAWP باشد، قطعه برای ادامه خدمت قابل قبول است.
- اگر فشار مجاز کاهشیافته < فشار طراحی یا MAWP باشد، قطعه غیرقابل قبول است.
شرایط پذیرش بر اساس RSF:
- اگر RSF محاسبهشده ≥ RSF مجاز باشد، قطعه برای ادامه خدمت مناسب است.
- اگر RSF محاسبهشده < RSF مجاز باشد، قطعه نیاز به تعمیر، تغییر شرایط عملیاتی (Rerate) یا بازنشستگی دارد.
مزایای ارزیابی قابلیت سرویس دهی
ارزیابی FFS مزایای متعددی دارد که در مراحل مختلف عمر یک دارایی (از طراحی تا بهرهبرداری) قابل استفاده است. برخی از این مزایا عبارتند از:
۱. کاربرد در مراحل مختلف عمر دارایی
تکنیک FFS میتواند در مراحل مختلف عمر یک دارایی، از جمله طراحی، ساخت و بهرهبرداری، اعمال شود.
این ارزیابی به مدیریت چرخه عمر تجهیزات کمک میکند و میتواند در برنامههای تمدید عمر تجهیزات نیز استفاده شود.
۲. کاهش نیاز به تعمیرات و تعویضهای غیرضروری
با استفاده از FFS، میتوان از تعمیرات یا تعویضهای غیرضروری جلوگیری کرد و هزینههای مرتبط را کاهش داد. این ارزیابی به شناسایی دقیق مشکلات و ارائه راهکارهای بهینه کمک میکند.
۳. بهبود استانداردهای ایمنی و در دسترسپذیری تجهیزات
تکنیک FFS استانداردهای ایمنی را ارتقا میدهد و اطمینان میدهد که تجهیزات بهطور ایمن و مطمئن به کار خود ادامه میدهند. این ارزیابی امکان تعیین عمر باقیمانده تجهیزات را فراهم میکند، که به برنامهریزی بهتر برای نگهداری و تعمیرات کمک میکند.
۴. ترکیب دانش و یافتههای قبلی برای بهینهسازی نگهداشت و بازرسی
FFS از دادهها و یافتههای قبلی (مانند نتایج بازرسیها، سوابق عملیاتی و تحلیلهای مهندسی) استفاده میکند تا برنامههای نگهداری و تعمیرات و بازرسی را بهینهسازی کند. این رویکرد باعث کاهش هزینهها و افزایش کارایی تجهیزات میشود.
ارزیابی قابلیت سرویس دهی (FFS) نه تنها ایمنی و قابلیت اطمینان تجهیزات را بهبود میبخشد، بلکه با کاهش هزینههای غیرضروری و بهینهسازی برنامههای نگهداری، به مدیریت مؤثر چرخه عمر داراییها کمک میکند. این روش به ویژه در صنایع با تجهیزات تحت فشار و شرایط عملیاتی چالشبرانگیز، بسیار ارزشمند است.
چه زمانی از FFS استفاده میشود؟
ارزیابی قابلیت سرویس دهی (FFS) برای بررسی یکپارچگی ساختاری و قابلیت استفاده از یک قطعه یا دارایی برای کاربرد مورد نظر آن انجام میشوند. این فرایند به ویژه برای ارزیابی قطعات تحت فشار بحرانی و سازههای جوششده استفاده میشود. FFS در مراحل مختلف عمر یک دارایی، از جمله طراحی، ساخت و بهرهبرداری، به کار میرود تا فرایندهای کاهش ریسک مورد نیاز برای استفاده ایمن و ادامهدار از داراییها یا قطعات شناسایی شوند.
صنایعی که از FFS استفاده میکنند:
FFS در بسیاری از صنایع مختلف، از جمله نفت و گاز، تولید برق، فرآوری شیمیایی و هوا فضا، کاربرد دارد. در زیر نمونههایی از مواردی که TWI (موسسه جوشکاری بریتانیا) ارزیابیهای FFS را در این صنایع انجام داده است، آورده شده است:
۱. صنایع دریایی
- برای بررسی مقادیر بالای سختی در مناطق جوششده یک سیستم لولهکشی استیل ضدزنگ
- برای بررسی یک خط لوله زیردریایی که توسط لنگر یک تانکر آسیب دیده بود
۲. تولید برق – مخازن تحت فشار
- از FFS برای ارزیابی دیژسترهایی که دچار خوردگی شده بودند، استفاده شد.
۳. صنعت نفت و گاز – سیستمهای لولهکشی
- ارزیابی FFS بر اساس آسیبهای موجود در یک خط لوله بینکشوری
- ارزیابی FFS در پاسخ به شناسایی یک زیربرش کوچک در ریشه جوش یک خط لوله
- از FFS برای ارزیابی یک سیستم لولهکشی فشار بالا پس از شناسایی فلنجها
نرمافزارهای ارزیابی قابلیت سرویس دهی
نرمافزارهای متنوعی ارائه شده است که به انجام ارزیابی قابلیت سرویس دهی (FFS) کمک میکنند. این نرمافزارها عبارتند از:
۱. IntegriWISE
این نرمافزار امکان ارزیابی یکپارچگی مخازن ذخیرهسازی، خطوط لوله، مخازن تحت فشار، دیگهای بخار و تجهیزات با دمای بالا را فراهم میکند.
این کار را با ارزیابی مکانیزمهای آسیب و ایجاد سناریوهای «چه میشد اگر» انجام میدهد.
۲. CrackWISE
این نرمافزار به ارزیابی عیوب در خطوط لوله، سازهها و تجهیزات تحت فشار کمک میکند تا اطمینان حاصل شود که این تجهیزات بهطور ایمن به کار خود ادامه میدهند.
۳. RiskWISE
این نرمافزار مدیریت یکپارچگی است که برای کارخانههای فرایندی، دیگهای بخار و خطوط لوله استفاده میشود.
این نرمافزار قادر است حجم زیادی از دادههای مرتبط با تکنیکهای بازرسی مبتنی بر ریسک را پردازش کند.
چکلیست ارزیابی FFS بر اساس API 579
شروع یک ارزیابی جامع تناسب برای ادامه خدمت (FFS) نیازمند توجه دقیق و برنامهریزی منظم است. یک چکلیست ساختارمند برای انجام ارزیابیهای دقیق و سازمانیافته ضروری است. استاندارد API 579 از موسسه نفت آمریکا (API) راهنمای معتبری برای این ارزیابیها ارائه میدهد و دستورالعملهای روشنی برای تعیین قابلیت استفاده از داراییهای صنعتی فراهم میکند.
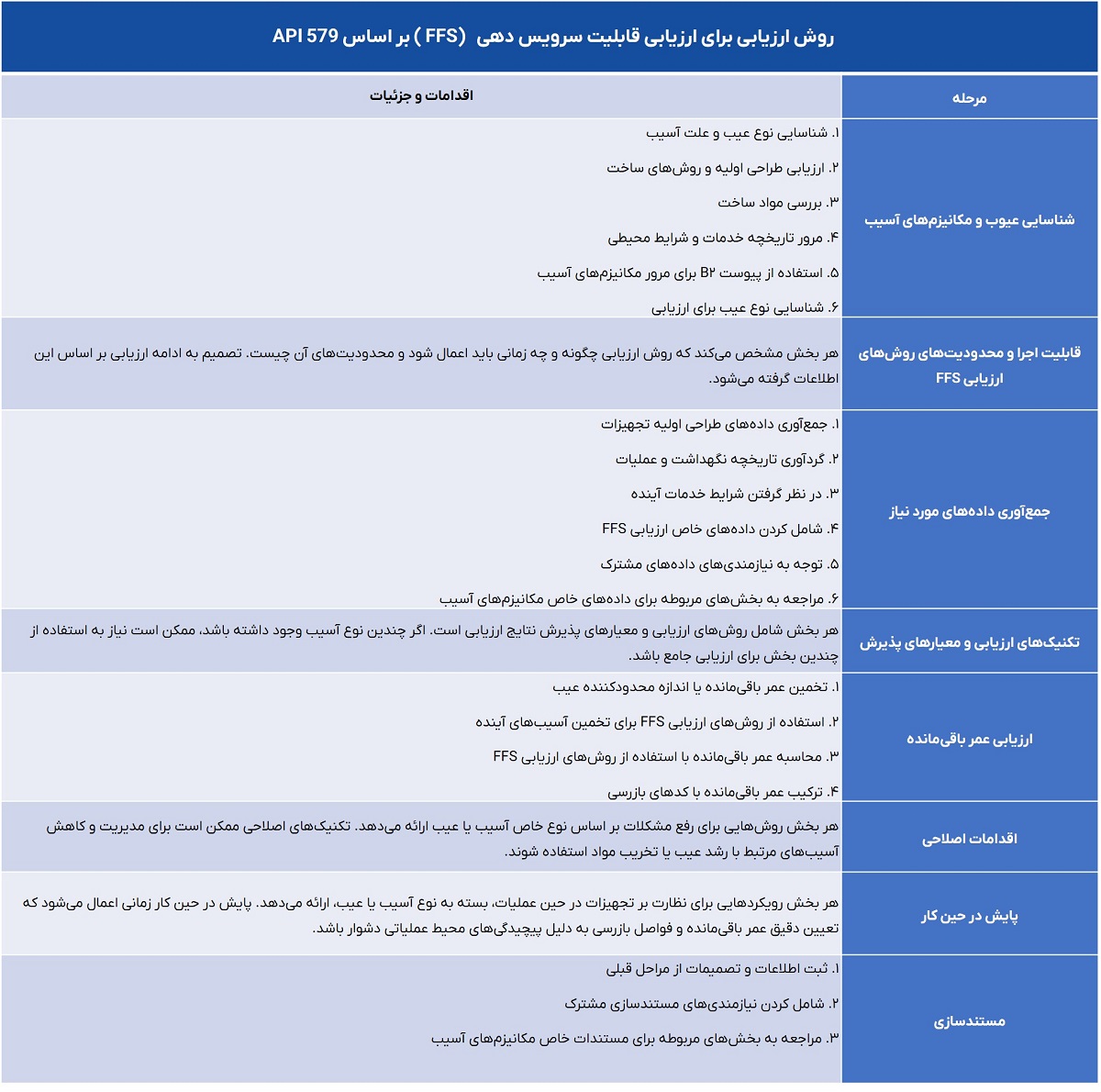
انجام ارزیابی قابلیت سرویس دهی (Fitness for Service FFS)، به ویژه با استفاده از رویکرد سهسطحی، برای اطمینان از ایمنی و کارایی تجهیزات صنعتی بسیار حیاتی است. چه یک بررسی سریع (سطح ۱) و چه یک ارزیابی دقیق و پیشرفته (سطح ۳)، هر سطح به ما کمک میکند تا درک بهتری از عملکرد تجهیزات و نیازهای آنها داشته باشیم. این نه تنها به عملکرد روان و بیوقفه تجهیزات کمک میکند، بلکه از بروز مشکلات احتمالی نیز جلوگیری مینماید.
یک پاسخ
واقعا سپاس گذارم بابت مطالب علمی و عمیقی که فراهم میکنی