Pegahe Aftab Spare Parts and Inventory Management Solution
From designing a classification and coding system for goods and parts to integrating data with inventory management software.
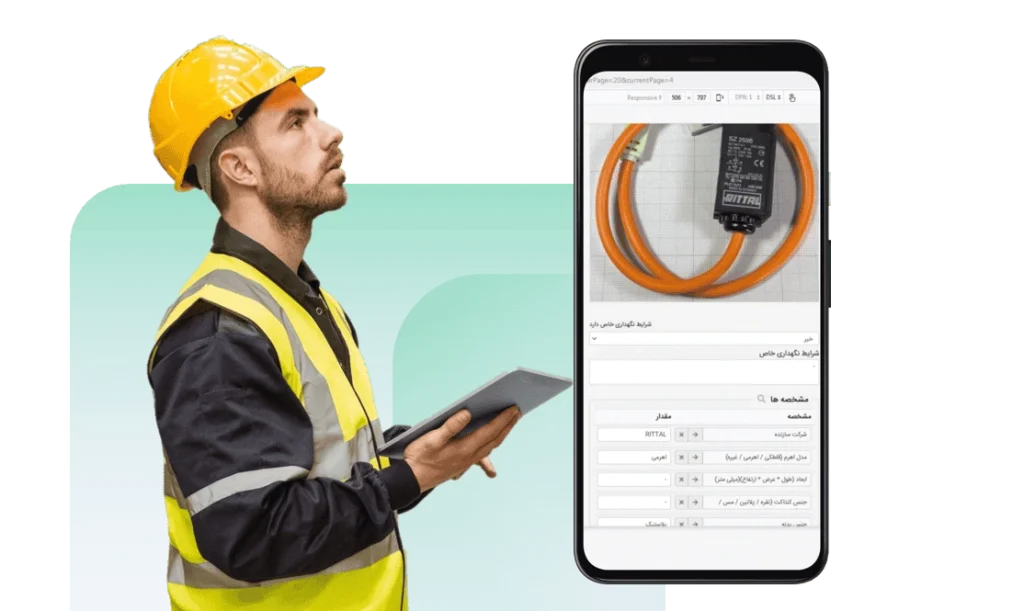
Services and Software for Spare Parts and Inventory Management Solution
The Pegahe Aftab Spare Parts and Inventory Management Solution is more than just software. It is a comprehensive set of services and software tools designed to define the most efficient classification system tailored to the organization’s specific conditions, requirements, and existing standards. After extracting the classes of goods and parts, we establish a clear identification mechanism and specify the detailed attributes for each category.
Next, we design the structure and workflow for identifying new items and re-identifying existing ones, which is then implemented within the Pegahe Aftab management software. Finally, based on the completed identification and the established best practices for coding goods and parts, all items are systematically coded within the software.
Our goal with this solution is to provide services and software tools that extend spare parts and inventory management into seamless integration with warehouse and stock management, supply chain management, and maintenance management.
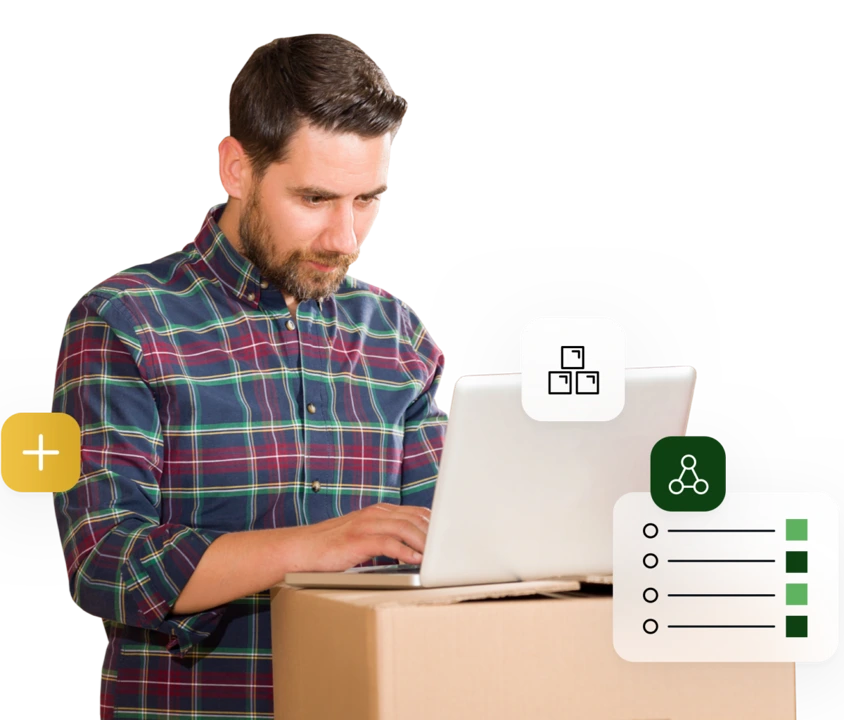
Spare Parts and Inventory Management Software
From defining product groups and enabling the classification and categorization of goods and parts, to establishing a hierarchical classification structure and integrating it with warehouse and inventory systems.
Consulting and Implementation Services
Our services include needs assessment, defining and designing classification methods, designing processes for identifying new items and re-identifying existing ones, team building and training staff to implement the classification system, as well as consulting and overseeing the execution.
Warehouse and Inventory Management Software
Spare parts and consumable materials defined in the spare parts and inventory management software can be integrated with the movement and transactions of goods and parts in Pegahe Aftab’s warehouse and inventory management system, creating a centralized and digitalized management system for goods and parts across the entire organization.
Our Services
Pegahe Aftab will work alongside you from a thorough assessment of your organization’s needs and the design of a new goods classification system to the implementation of classification, identification, and coding steps. By empowering your organizational team and digitizing this system, we help streamline the management of physical assets within your organization.
Consultation
Item coding is the result of a goods and spare parts classification system, and it has always been a challenging and complex task for organizations. Pegahe Aftab’s services facilitate this major transformation by defining a clear and structured roadmap.
Parts and Goods Identification
After defining the roadmap and implementing the goods classification structure, Pegahe Aftab is ready—with its specialized and experienced team—to identify your organization’s goods and spare parts based on the selected classification system.
Standardized Item Coding
Based on your organization's requirements and characteristics, and using global best practices, one of the coding and classification methods—such as TATA, TMC, GS1, GPC, MESC, SFI, or other approaches—will be implemented.
Software Solution Implementation
After defining the classification system, identification, and coding of goods and spare parts, this system and identification processes will be implemented and operationalized within Pegahe Aftab’s spare parts and consumables management software solution, which will then be integrated with other related systems.
Training and Support
During and after the design and implementation of the classification, identification, and coding system for goods and spare parts, as well as the deployment of the necessary software solutions, you can benefit from professional support services and essential training to build your organizational team, ensuring sustainable use of the spare parts and inventory management system.
Custom Development
If customization of Pegahe Aftab’s spare parts and inventory management solution is needed to meet your organization’s unique requirements and specifications, this solution—with its flexible structure—can be tailored in the shortest possible time. Our product development team will be by your side throughout the process.
Expected Benefits from Implementing Pegahe Aftab’s Spare Parts and Inventory Management System
Pegahe Aftab Spare Parts and Inventory Management Software
In the Pegahe Aftab spare parts and inventory management software, it is possible to define product groups, classify and categorize goods and parts, and establish a hierarchical tree structure for classification. The software allows defining supplementary attributes for each class, forming identification teams, and designing and implementing identification processes. During the identification process, after recording and verifying the entered data, identification requests lead to the creation of items in the warehouse inventory database, and item codes are assigned accordingly. Additionally, the organization can use this software to create an electronic catalog for all items in the warehouse and share it across procurement, inventory control, production, finance, maintenance, and other organizational units that interact with goods and spare parts.
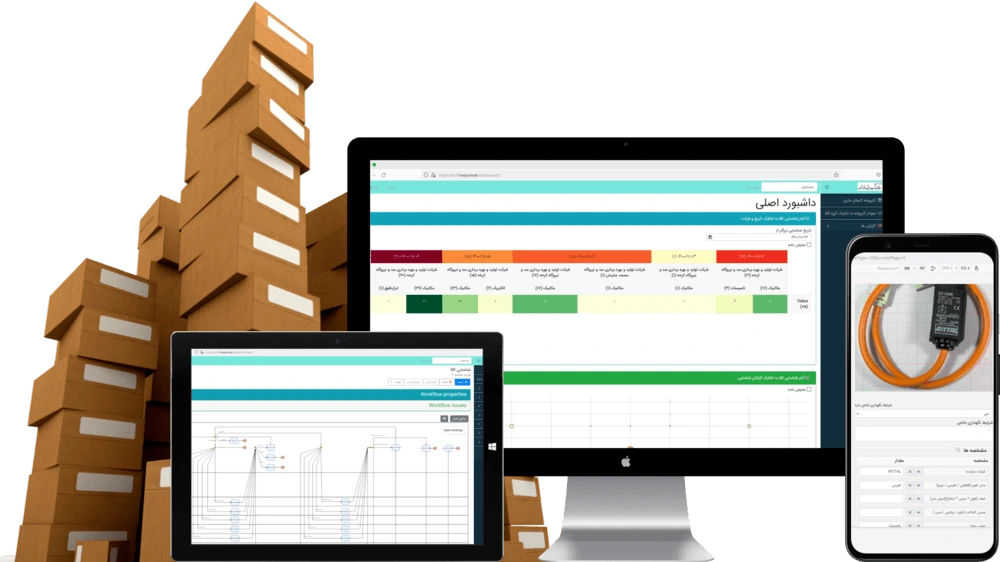
Components of Pegahe Aftab’s Spare Parts and Inventory Management Software
The core of the goods management system is creating a hierarchical classification or categorization structure for items. This structure helps identify goods by grouping them based on their category and usage characteristics. For each class, additional attributes can be defined to aid in identifying each item. The software supports various classification methods, including TATA, MESC, TMC, and others.
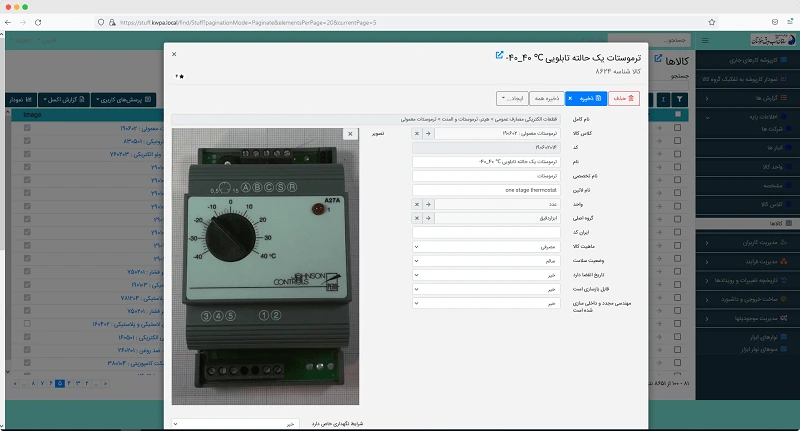
One of the challenges in warehouse and inventory management systems is handling items that circulate within the organization using different units of measurement. In the Pegahe Aftab system, goods can be defined with standardized units of measurement, and through automatic system-based conversions of secondary units, related transactions are seamlessly processed. This also prevents the duplication of similar item definitions.
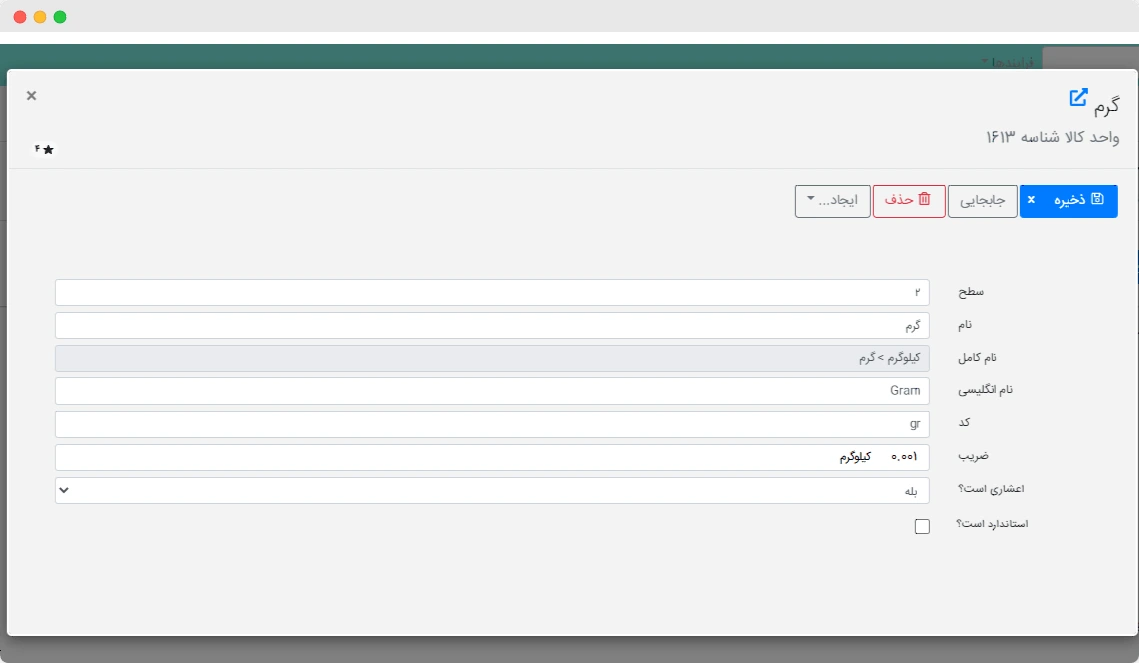
Item identification is a multidisciplinary activity and, unlike common practices, items should be defined by technical experts. Since defining a new item requires determining its class as well as general, supplementary, and specific attributes (related to holding company groups), it is impossible for a single person to complete and approve this task alone. This system enables experts and specialists from various organizational departments to define new items through a fully automated process.
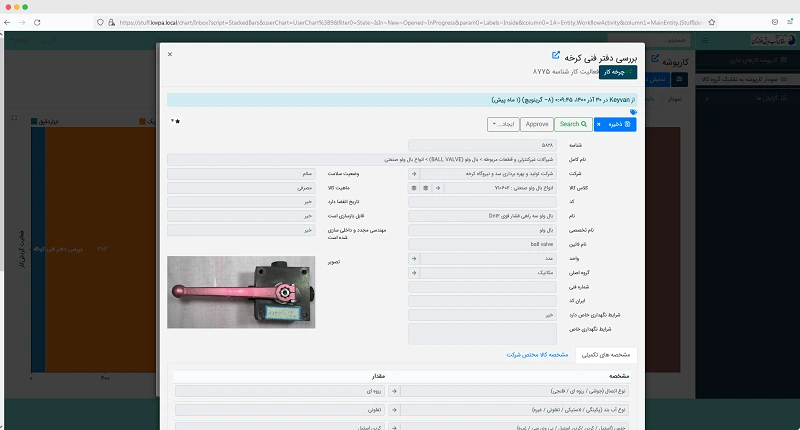
To optimize the classification system over time, it is necessary to make changes to the recorded information and adjust the classes or attributes of previously defined items. This requires the ability to review defined items and their past transactions. The Pegahe Aftab system provides organizations with the capability to carry out this process entirely digitally.
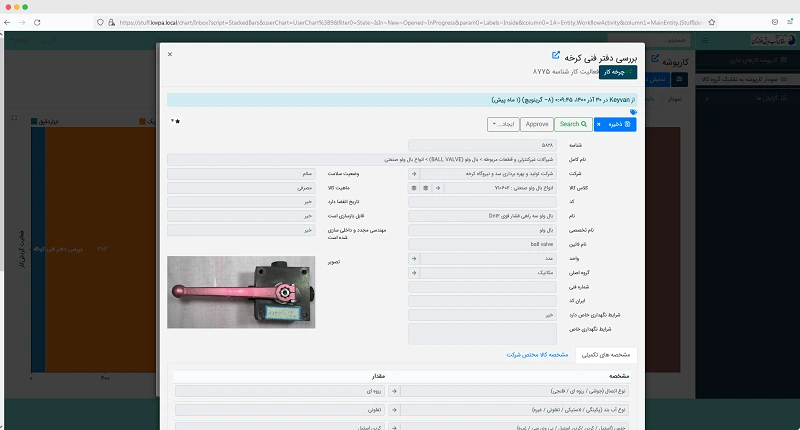
Item coding is usually based on their classification structure, although depending on the chosen pattern and classification, characters or phrases may be added to the beginning or end of each item code. Pegahe Aftab’s goods and spare parts management software allows organizations to define various coding patterns—such as using class structures for coding, incorporating general and supplementary attributes, and more—for their items and parts.
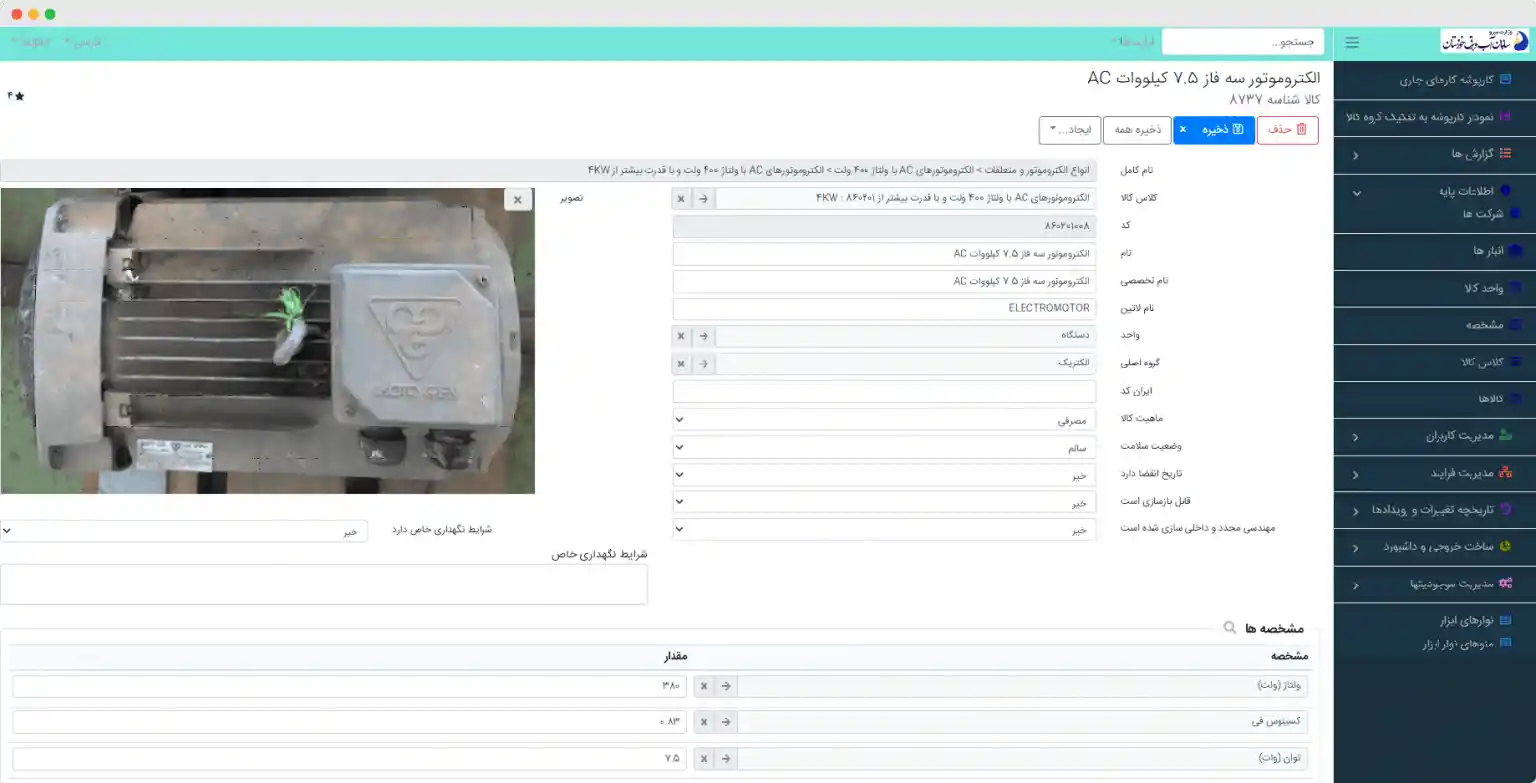
Since the Pegahe Aftab system is developed for managing goods and spare parts within holding organizations, it includes features that provide statistics and information related to item identification and re-identification, allocation data across organizational subsidiaries, as well as overall circulation and inventory of goods and parts—all accessible through interactive dashboards.
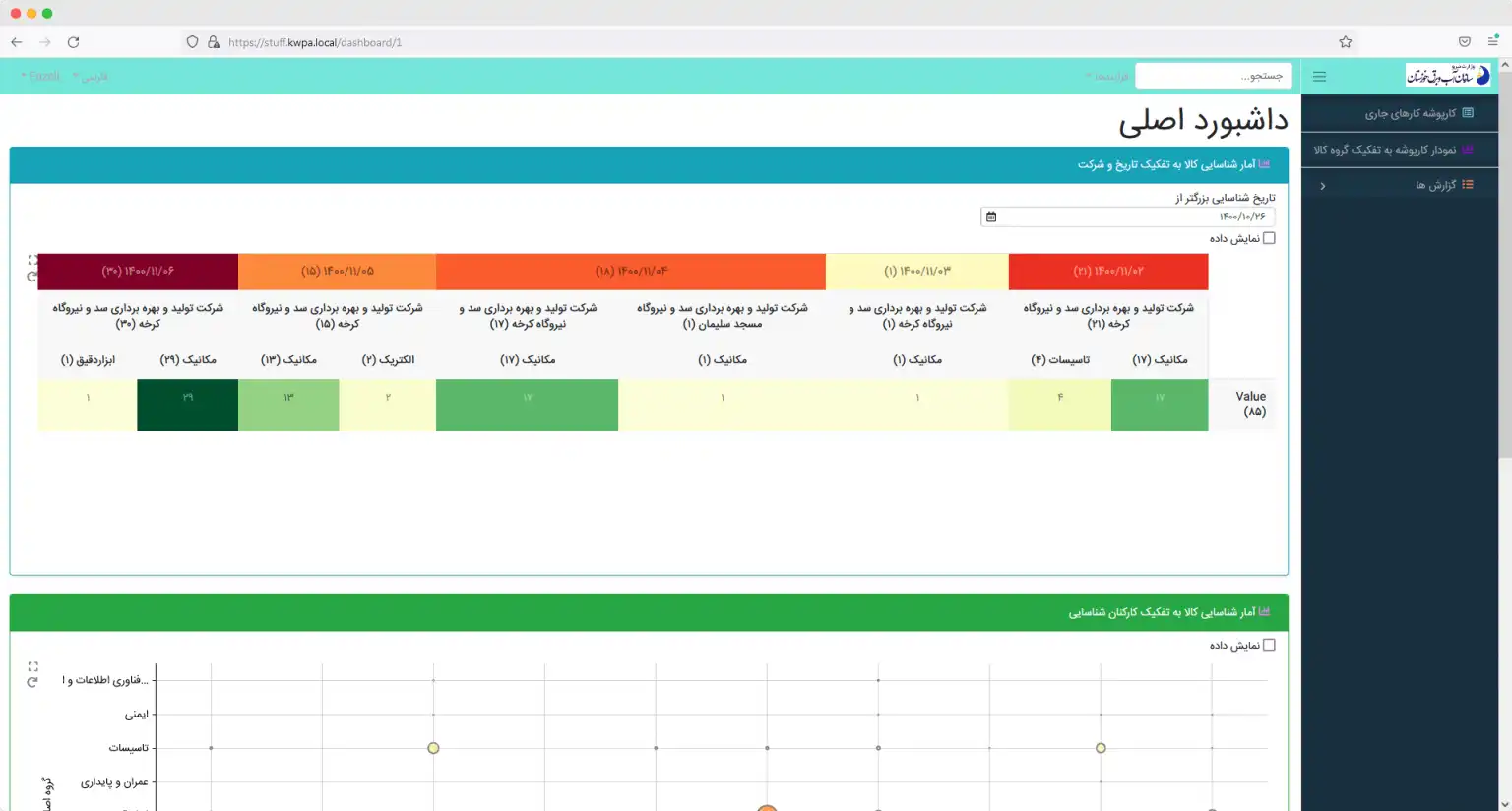
The process engine and workflow designer within Pegahe Aftab’s spare parts and inventory management system enable organizations to easily streamline all goods management processes across departments by defining existing workflows and applying business rules. Additionally, if needed, the organization can quickly and independently make desired changes to its workflows using the system’s visual process design environment—without relying on Pegahe Aftab’s support.
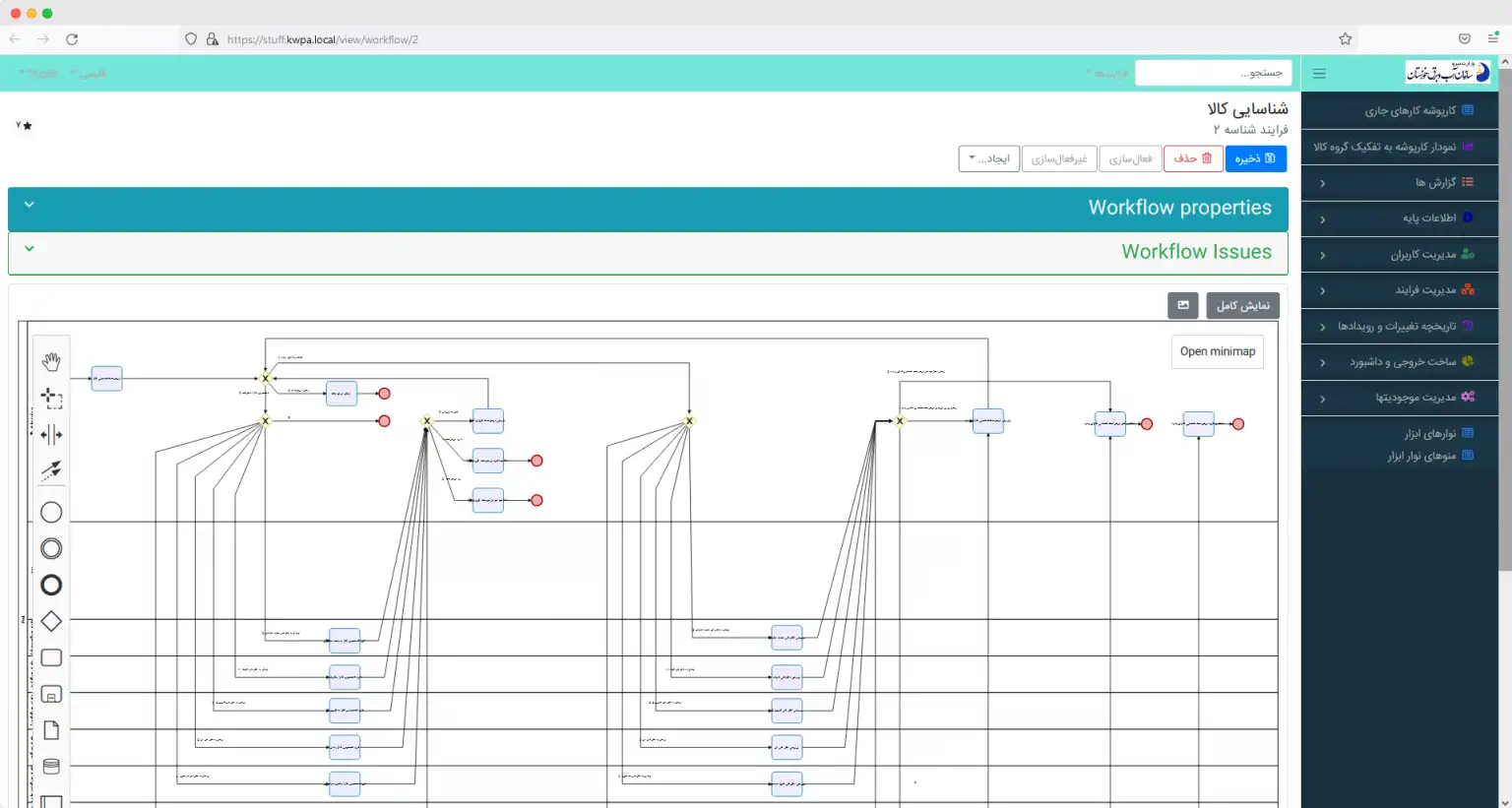
User Management
System administrators can effortlessly manage users by assigning individuals, roles, organizational positions, and access levels to different system components.
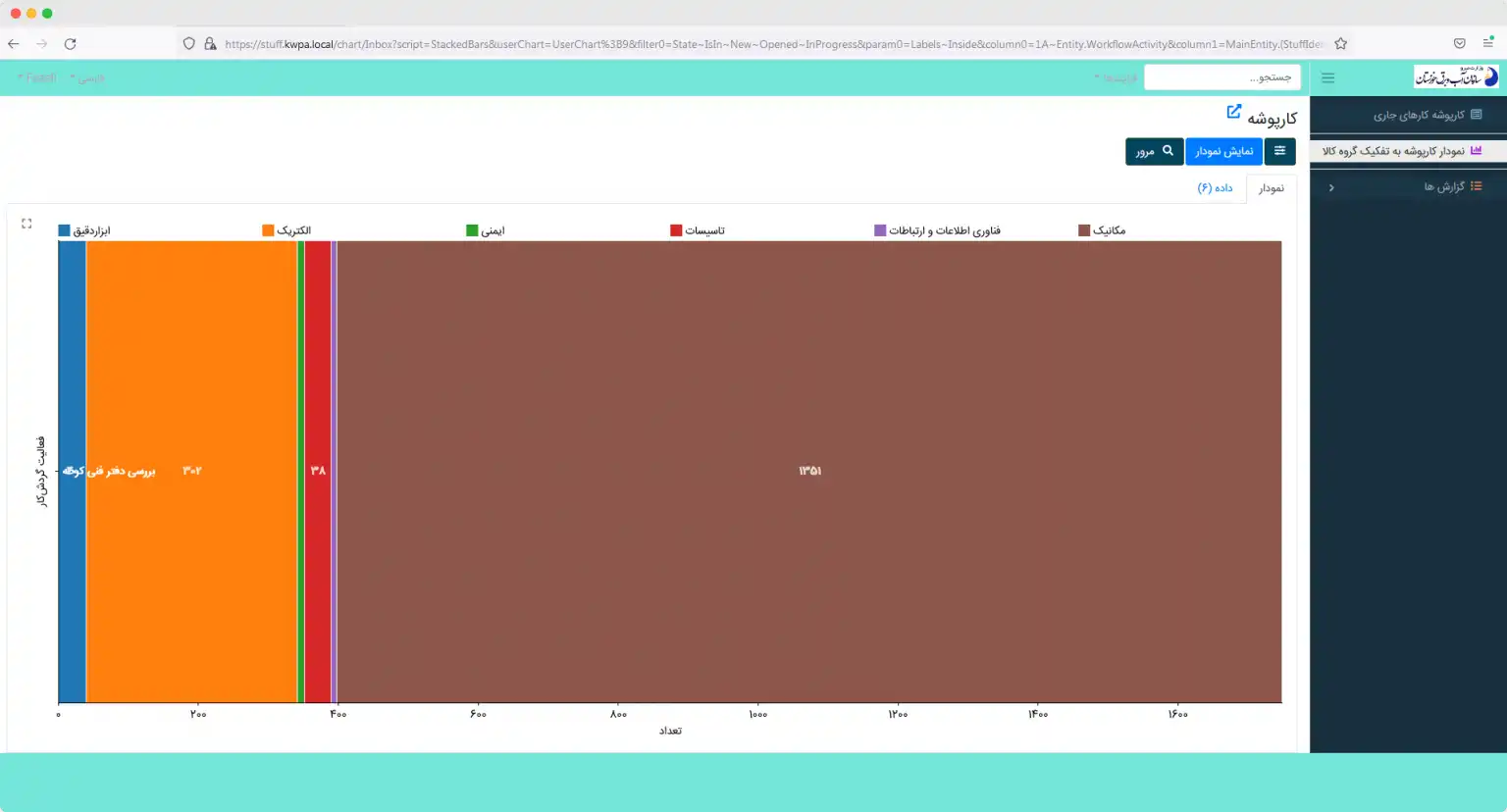
Benefits of Using the Goods and Spare Parts Management Software
Creating a Common Language
Regardless of the use of items and parts across various systems and equipment, by identifying units and defining the consumption and application of each item and part within the system, all stakeholders throughout the organization will be able to consistently refer to each item or spare part by a unified name and code, along with a standardized set of general and supplementary specifications. This ensures clear and integrated usage across the entire organization.
Increased Uptime
Identifying spare parts and managing inventory within the system—especially for items and equipment critical to production stability—and enabling inventory planning for each part (such as setting reorder points and reorder intervals) helps reduce equipment downtime, minimize the frequency and duration of failures, and ultimately enhances equipment availability, reliability, and overall uptime.
Robust Inventory Control
By assigning unique identification (tracking) to all goods and spare parts and linking these items to the organization's systems and equipment, it becomes possible to analyze the criticality levels of the organization’s equipment. Using equipment data within the inventory management system allows for highly accurate management of spare parts inventory and enables more optimized decision-making regarding stock levels of goods and parts.
Ease of Inventory Counting
Access to all product information and details within the software system enables inventory and warehouse operations to be carried out with high accuracy, relying on precise data. Having an integrated classification system also ensures that warehouse organization is structured, making item retrieval simple and fast, and allowing periodic checks to be performed with greater item-specific details and confidence.
Time and Cost Savings
By assigning unique identification and enabling easy tracking of items, organizations can efficiently make decisions about surplus, idle stock, and safety inventory levels of goods and spare parts. Defining the relationships between items and equipment helps prevent inventory shortages when needed, thereby avoiding resource wastage.
Greater Accessibility
By identifying and classifying the organization’s goods and parts, it becomes possible to easily define each user’s access to the required item classes according to their roles within the organization; thus, each person can directly and online obtain information about the goods and parts they need. This creates easier and more transparent accessibility throughout the entire organization.
Project for Organizing the Material Management Processes in the Power Plants of Khuzestan Water and Power Authority
Khuzestan Water and Power Authority, as the steward of surface and groundwater resources, is responsible for conducting studies in water resource planning, constructing dams (including reservoir, diversion, and regulating dams), irrigation and drainage networks, hydroelectric power plants, development of water and soil resources, as well as the operation and protection of these resources.
This project was implemented through the following steps:
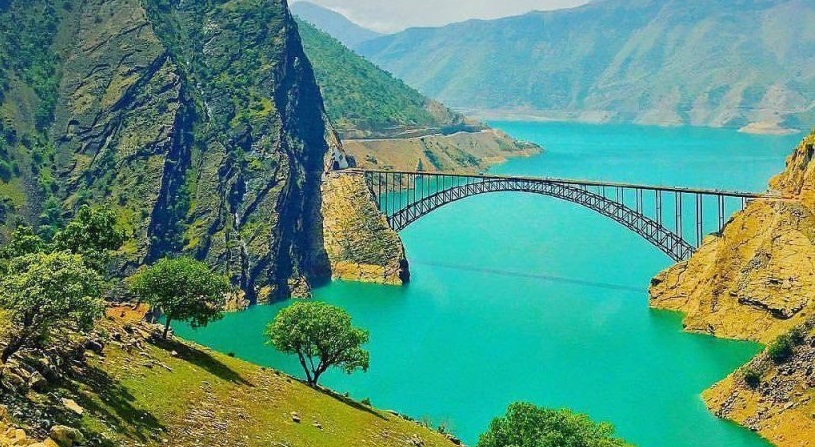
Project for Organizing the Material Management Processes in the Power Plants of Khuzestan Water and Power Authority
1. Designing and establishing the organizational structure required for the project
2. Designing a classification and coding system for materials (spare parts and consumables)
3. Defining, analyzing, and designing the process of “identifying new items”
4. Defining, analyzing, and designing the process of “re-identifying existing inventory items”
5. Deploying the required software system to support the “re-identification of existing items” process in each warehouse, ensuring full integration with the inventory management system
6. Deploying the required software system to support the process of “requesting identification for new items” needed in the future
7. Training the classification and coding system, as well as operational and supervisory procedures for item identification and new item requests, to the item identification task force
8. Implementing, analyzing, and designing reports and key performance indicators (KPIs) required by the organization through the spare parts and materials management system, and developing the relevant dashboards
Our Clients
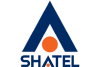
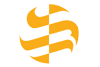
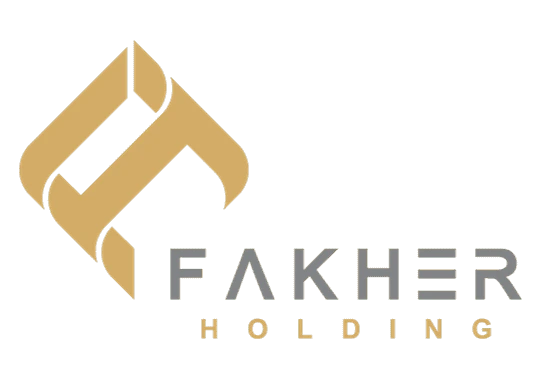
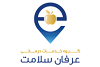
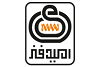
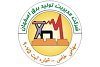
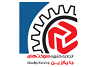
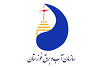
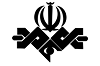
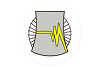
FAQs
Answers to your questions about Pegah Aftab’s CMMS Solution are here.
Does relying solely on software suffice in spare parts and inventory management?
Although having software plays a significant role in systematizing spare parts and inventory management, it is crucial to understand that managing materials and spare parts is not a one-time project—it is a continuous process. Just like warehouse operations and transactions, materials and spare parts management processes must be ongoing and continuously optimized within the organization.
Choosing the right classification system and standards tailored to the organization’s specific needs, localizing the selected standards and best practices, as well as forming and training internal teams are all essential components of success.
Pegahe Aftab is ready to support you through every step of this journey.
How does the spare parts and inventory management system integrate with other organizational systems?
The spare parts and inventory management system is a core system, and it is essential that the data collected—such as item information and detailed specifications—be utilized across other organizational systems, including warehouse management, procurement and ordering, and maintenance systems.
Pegahe Aftab’s solution is designed to seamlessly integrate with all related systems, ensuring consistency, accuracy, and efficiency across your organization.
How long does it typically take to complete a project for designing a material classification system?
To identify items and spare parts, it is first necessary to assign identification teams based on the main categories of goods—such as mechanical, electrical, instrumentation, safety, health, and information technology. Each team can typically identify 4 to 6 items per hour.
For example, identifying the items in a warehouse with approximately 10,000 inventory items would require about 4 to 6 months if conducted by three identification teams (a total of six personnel).