هر چند وقت یکبار خبر حوادثی چون انفجار، انتشار گازهای سمی یا آتش سوزیهای باعث بهت و حیرت جهانیان میشود. به عنوان مثال دو سال قبل، انفجار عظیم ۲۷۵۰ تن نیترات آمونیوم در بندر بیروت لبنان را به خاطر بیاورید که چه قدر تراژیک بود و دنیا را تکان داد. چنین حوادثی کابوسهایی هستند که باید همواره تلاش کرد تا از وقوع آنها جلوگیری کرد.

بازرسی بر مبنای ریسک RBI
در این مقاله بر یکی از جنبههای کاهش ریسک در صنایع و به طور مشخص، ریسکهای خرابی داراییهای ثابت، میپردازیم. بازرسی بر مبنای ریسک یا RBI (Risk Based Maintenance) روشی است که به سازمانها این امکان را میدهد تا روی حیاتی ترین دارایی های ثابت خود تمرکز کنند. توجهی که که برای صنایع تجهیزمحور ضروری است زیرا در یک یک واحد صنعتی معمولی دارایی های ثابت بسیار زیادی وجود دارد که همواره نمیتوان آنها را به صورت مستقیم زیر نظر داشت.
بازرسی مبتنی بر ریسک روشی موثر و کارآمد به منظور ایجاد یکپارچگی و افزایش قابلیت اطمینان در دارایی های ثابت تاسیسات صنعتی است. روشی که به تخصیص صحیح منابع بازرسی به دارایی های ثابتی، که بر اساس اطلاعات شناسنامهٔ ریسک آنها نیاز به بیشترین توجه دارند، را کمک میکند.

به همین خاطر است که توصیه میشود که بازرسی بر مبنای ریسک (RBI) بهعنوان یکی از استراتژیها و روشهای پیشفرض واحدهای صنعتی، به ویژه در پروژههای نگهداری و تعمیرات بزرگ استفاده شود. زیرا در این صورت به جای انتظار کشیدن برای روبرو شدن با خرابی داراییهای ثابت و واکنش نشان دادن به آن در موقعیتهای ناایمن و آسیبها و ضررهای متعاقب آن، میتوان از قبل برنامهای کنشگرایانه برای کاهش احتمال و ریسک خرابی داشت.
بازرسی مبتنی بر ریسک RBI را باید به عنوان جزئی از استراتژی نگهداری و تعمیرات مبتنی بر ریسک (RBM) در نظر گرفت و همچنین از آن به عنوان راهکاری برای حرکت به سوی نگهداری و تعمیرات مبتنی بر وضعیت تجهیز (CBM) استفاده کرد.
دارایی های ثابت و ریسکهای آن
بین داراییهای ثابت و مکانیکی تفاوت وجود دارد. تمایز در این حقیقت ساده است که قطعات مکانیکی شامل قطعات دوار یا متحرکی هستند که معمولاً توجه بخشهای مختلف واحد نگهداری و تعمیرات را به سمت خود سوق میدهند. به طور کلی، قطعات دوار یا متحرک مکانیکی اغلب در طول کارکرد خود به نسبت دیگر تجهیزات سریعتر خراب میشوند. زیرا حرکت و دوران این نوع از قطعات باعث ایجاد اصطکاک، حرارت و ارتعاش شده و در نهایت این اتفاقات منجر به ایجاد ساییدگی در قطعه میشوند.
با این حال، وجود ارتعاش، حرارت و اصطکاک دلیل موجهی برای نادیده گرفتن قطعات ثابت در تاسیسات صنعتی نیست، زیرا این قطعات در معرض مکانیزمهای فرسودگی مختلفی مانند خوردگی زیر عایق (CUI) هستند که باید به آنها توجه شود. داراییهای ثابت معمولاً در ساخت کارخانهها یا برای ذخیرهسازی و حمل و نقل سیالات استفاده میشود. این سیالات به ویژه در تاسیسات شیمیایی اغلب موادی خطرناک هستند.

انسجام و یکپارچگی و قابلیت اطمینان داراییهای مکانیکی در حیطهٔ نگهداری و تعمیرات مبتنی بر قابلیت اطمینان (RCM) میگنجد، در حالی که دارایی های ثابت به طور مشخص مرتبط با موضوع مورد بررسی امروز ما، یعنی بازرسی مبتنی بر ریسک هستند. علیرغم شباهتهایی که بین استراتری نت مبتنی بر قابلیت اطمینان یا RCM در مقایسه با بازرسی مبتنی بر ریسک یا RBI به خصوص در کاربرد ماتریس ریسک در هر دو، اما باید توجه داشت که اصولا RCM و RBI دو مقولهٔ مجزا هستند.
دارایی ثابت چیست؟
دارایی های ثابت اجزایی از تاسیسات صنعتی هستند که شامل قطعات دوار یا متحرک نیستند. یک کارخانه با اندازهٔ متوسط به راحتی میتواند بیش از ۱۰۰ دارایی ثابت داشته باشد، به عنوان مثال:
- سیستمهای لوله کشی
- مخازن ذخیره سازی
- مخازن تحت فشار
- مبدلهای حرارتی
- پوشش داراییها
- سازههای حمال یا باربر
نمونههایی از داراییهای مکانیکی هم عبارتند از پمپها، شفتهای دوار، تسمه نقالهها، توربینها، موتورها و بازوهای رباتیک.
خرابی دارایی های ثابت
صنایع تجهیز محور با مسائل و مشکلات قابل توجهی مواجه هستند که بازرسی مبتنی بر ریسک بخشی از راهکار برای حل مشکلات گستردهتر و عمیقتر ناشی از خرابی دارایی های ثابت است. برخی از این مسائل و مشکلات موارد زیر هستند:
- نگهداری و تعمیرات اصلاحی اغلب خیلی دیر انجام می شود (بعد از خاموشی یا توقف تجهیز)، نگهداری و تعمیرات پیشگیرانه اغلب خیلی زود انجام میشود
- ناکارآمدی هزینهکردها و پایین بودن سطح آپتایم (آماده بکاری) و زمان در دسترس تجهیز به دلیل توقفهای برنامهریزی نشده
- بروز مدلهای تخریب نارسا، دستورالعمل های استاندارد محدود، فقدان ابزار تخصصی (فنی)
خوردگی زیر عایق (CUI)
خوردگی زیر عایق (CUI) یکی از مکانیزمهای تخریب است که معمولاً شاهد وقوع آن در لولهها و وسایل و تجهیزات دارای عایق هستیم. تخریبی که معمولاً یکی از تهدیدهای کلیدی و مهم برای داراییهای قدیمی در صنایع مختلف در عصر ما قلمداد میشود. کنترل پدیده خوردگی زیر عایق دشوار است زیرا محلهایی که معمولاً خوردگی در آنها رخ می دهد به سختی قابل تشخیص و در چشم هستند. همچنین میزان تخریب به عوامل زیادی بستگی دارد و پیشبینی آن دشوار است. اقدام اصلاحی بر آن به طور متوسط پس از 20 تا 30 سال پس از شروع عملیات ضروری است. به طور بالقوه، تخریب لولههای فولادی و سایر تجهیزات توسط خوردگی زیر عایق یا CUI می تواند منجر به حوادث بزرگی که ناشی از دست رفتن یکپارچگی سیستم است، شود. برای جلوگیری از این امر، گاهی در صنایع اقداماتی اصلاحی که ارزش آنها به میلیاردها یورو میرسد انجام میشود.
به منظور کاهش ریسکهای مرتبط با مکانیزمهای مختلف خرابیاز جمله همین پدیدهٔ خوردگی زیر عایق، لازم است که هر یک از این مکانیزمهای تخریب به خوبی فهمیده و درک شوند و پس از آن اقدامات کنترلی برای اطمینان از یکپارچگی و قابلیت اطمینان تجهیزات و تاسیسات تعریف شوند. اقدامات کنترلی بایدشامل بازرسی، نظارت، تنظیمات و تعمیرات باشد.
بهبود یکپارچگی سیستم، توقفهای برنامهریزینشده کمتر، هزینههای کمتر برای نگهداشت و تولید بالاتر تعدادی از مزایا و نتایج مثبت بازرسی مبتنی بر ریسک هستند.
نتایج قابل دسترسی بر اساس ریسک
بازرسی
بازرسی بر مبنای ریسک RBI منجر به پنج نتیجهٔ قابل دسترسی زیر میشود: (شکل بالا را ببینید):
- اولویت بندی اجزای پرخطر تجهیز: در اصل به این سوال پاسخ داده میشود که چه چیزی باید بازرسی شود
- تعیین فواصل بازرسی: چه وقت و در چه فواصلی بازرسی انجام شود
- مکانیزمهای آسیب مورد انتظار: کجا باید بازرسی صورت بپذیرد
- انتخاب بهترین روش بازرسی: نحوه بازرسی چگونه باید باشد
- دادههای لازم برای بهبود مستمر: آنچه باید گزارش شود چه چیزهایی را شامل میشود.
برای به دست آوردن این نتایج قابل دسترسی و موثر ساختن آنها، RBI یا بازرسی مبتنی بر ریسک یک فرایند ساختار یافته را دنبال میکند.
فرایند بازرسی مبتنی بر ریسک RBI
فرایند بازرسی مبتنی بر ریسک RBI همانطور که در شکل بعدی نشان داده شده است شامل چرخهای است که شش مرحلهٔ زیر را در برمیگیرد:
- جمع آوری دادهها و اطلاعات
- ارزیابی ریسک
- رتبه بندی ریسک
- طرح و برنامه بازرسی
- کاهش ضرر
- ارزیابی مجدد
مرحله ۱: جمع آوری دادهها و اطلاعات
فرایند RBI با مرحله جمع آوری داده ها و اطلاعات آغاز میشود. این اقدام برای درک ویژگیهای فرایندهای اولیه، به ویژه برای درک تأثیر مخرب محیطهای پردازش مواد شیمیایی در تجهیزات ثابت، لازم است. در این مرحله اطلاعات دقیق و کاملاً بهروزی را برای مراحل بعدی فرایند بازرسی مبتنی بر ریسک RBI فراهم میکنیم. هدف اصلی در گامهای بعدی تبدیل همهٔ این دادهها به یک برنامه بازرسی مبتنی بر ریسک مناسب برای نظارت مستمر بر وضعیت تجهیز، بازرسیهای دورهای و بازسازیهای بزرگتر است.

برای افزایش احتمال پیشبینی خرابی، پایگاه دادهٔ بازرسی مبتنی بر ریسک RBI باید شامل اطلاعات بهروز زیر باشد:
- شرح سازوکارها یا همان مکانیزمهای شکست
- مطالعات خوردگی، به ویژه در مورد خوردگی زیر عایق (CUI)، که به عنوان قاتب بدنان تجهیزات معروف است.
- مدلهای تخریب در هر فرایند.
دادهها معمولاً از طریق تجزیه و تحلیل دقیق و موشکافانهٔ فرایند و با بررسی و مطالعهٔ بلند مدت خوردگیها و تخریبها در هر بخش از تجهیزات استاتیک درگیر جمعآوری میشوند. جمعآوری و پردازش این دادهها ممکن است تلاش زیادی را بخواهد و به همین خاطر باید برای انجام آن یک چشمانداز بلندمدت داشت. به خصوص زمانی که سیستمهای اطلاعاتی مختلفی را در سازمان داریم که اطلاعات بین آنها رفت و برگشت دارند. بسیاری از سازمانهای بزرگ برای حل این مساله از قبل قبلاً پایگاهی اطلاعاتی از مدلهای مختلف تخریب تهیه کردهاند که به آنها در امر جمعآوری اطلاعات کمک میکند.
دادههای مورد نیاز در تجزیه و تحلیل ارزیابی مبتنی بر ریسک RBI
داده هایی که معمولاً برای تجزیه و تحلیل RBI مورد نیاز است ممکن است شامل موارد زیر باشد، اما باید یادآوری کرد که این دادهها محدود به موارد زیر نیست:
- نوع تجهیزات (قطعات اصلی، قطعات جایگزین یا قطعات اصلاحی؛ طول عمر باقیمانده)
- مصالح ساختمانی
- سوابق بازرسیها، تعمیرات و تعویضها
- فرایند ترکیب سیالات
- موجودی سیالات
- شرایط عملیاتی
- سیستمهای ایمنی و تشخیص
- مکانیزمهای تخریب و میزان و شدت تخریب (مانند خوردگی، خوردگی زیر عایق، خستگی فلز (metal fatigue) (به شکست ماده در اثر اعمال نیروهای متناوب کمتر از استحکام نهایی و (اغلب) کمتر از حد تسلیم، خستگی گفته میشود. خستگی مواد وقتی اتفاق میافتد که ماده تحت تنشهای تکراری یا نوسانی قرار گیرد که منجر به شکست ناگهانی قطعه میگردد. دلیل اصلی خطرناک بودن شکست خستگی این است که بدون آگاهی قبلی و قابل رویت بودن اتفاق میافتد. خستگی علت شکست زودهنگام بیشتر قطعههای صنعتی است. خستگی بهطور معمول همراه با جوانهزنی ترک در سطح قطعه یا نواحی تمرکز تنش و اشاعهٔ آن در ناحیهٔ تحت تنش بیشینه است.) ، استرس یا حمله شیمیایی)
- تراکم کارکنان
- دادههای مربوط به پوشش، روکش، و عایق
- هزینههای به وجود آمدن اختلال و توقف در کسبوکار
- هزینههای تعویض تجهیزات
- هزینههای پاکسازی و اصلاح محیط زیست
داشتن کتابخانه یا پایگاهی از مدلهای مختلف تخریب پایه و اساس تمام استراتژیهای نگهداری و تعمیرات است. چنین پایگاهی پیش نیازی برای حرکت از پارادایم بازرسی قاعدهمند یا یازرسی مبتنی بر زمان به پارادایم بازرسی مبتنی بر ریسک است.
مرحله ۲: ارزیابی ریسک
برای هر قسمت از تجهیزات استاتیک، احتمال خرابی و عواقب خرابی بر اساس دادههای موجود در پایگاه پایگاه داده بازرسی بر مبنای ریسک (RBI) که در مرحلهٔ قبل تهیه کردیم، ارزیابی میشود. آنالیز احتمال خرابی باید تمام مکانیزمهای زوال و تخریب تدریجیای را که تجهیزات مورد مطالعه در معرض آن هستند، بررسی کند.
در این مرحله و برای ارزیابی ریسک، پیامدهای زیر برای خرابیها باید در نظر گرفته شوند:
- پیامدهای مالی
- پیامدهای بهداشتی و مرتبط با سلامتی
- پیامدهای محیط زیستی
- پیامدهای نظارتی و مرتبط با قوانین و دستورالعملهای بالادستی
بازرسی مبتنی بر ریسک یا RBI به نگرانیهای بسیاری از مدیران کارخانه به خصوص نگرانیهای زیر قرار است پاسخ دهد:
- کاهش یکپارچگی و انسجام تاسیسات
- خرابی داراییهای ثابت و پیامدهای آن (مانند تعمیرات گسترده، بروز توقفهای ناگهانی و برنامهریزی نشده)
- قابلیت دسترسی و قابلیت اطمینان ناکافی تاسیسات
- پیامدهای خرابی برای کل کسبوکار (مانند افزایش هزینهها، پیامدهای مربوط به HSE و غیره)
- ایمنی کارمندان و ساکنان محلی (مصدومیت، سوختگی یا مسمویت آنها)
- پیامدهای مربوط با پاکیزگی محیط (نشت مواد خطرناک، انفجارهای قوی، انتشار گازهای سمی)
- پیامدهای مرتبط با الزامات قانونی مقامات (جریمههای مربوط به تخطی از قوانین، تعطیلی یا پلمپ کارخانه).
احتمال خرابی در بازرسی مبتنی بر ریسک معمولاً بر حسب فراوانی بیان میشود (از ۱ تا ۵) در حالی که پیامدهای آن از “A” (جزئی) تا “E” (شدید) را شامل میشود. در مرحله بعد، ریسک خرابی محاسبه میشود که منجر به دستهبندی ریسکها در سه دستهٔ ریسک «زیاد»، «متوسط» و «کم» میشود.
ریسک خرابی = احتمال خرابی x پیامد خرابی
RoF = PoF x CoF
ارزیابی ریسک کلی واحد صنعتی یا کارخانه بسیار امر پیچیدهای است. به همین دلیل است که برای انجام |آن به یک تیم چند رشتهای با تخصصهای متعدد نیاز است. فرایند بازرسی مبتنی بر ریسک یا RBI باید شامل ذینفعان و مشارکتکنندگان متعدد در زمینههای مهندسی متفاوت باشد. هر چند در این عرصه قضاوت افراد باتجربهٔ میدانی در این حرفه باید بسیار ارزشمند تلقی شود، اما حتی برای آنها نیز ممکن است در بسیاری موارد، برآورد ریسکها بسیار دشوار باشد.
مرحله ۳: رتبه بندی ریسک
برای اولویتبندی ریسکها و بامعنا ساختن نتایج تجزیهوتحلیل در مرحلهٔ قبل، میتوان از یک ماتریس ریسک استفاده کرد. ماتریس ریسکی مانند یک ماتریس ریسک ۷ در ۷ که در مثال نشان داده شده است. دستههای ریسک (RoF) در ماتریس دستههای احتمال (PoF) توسط دستههای پیامد (CoF) ترسیم میشوند.
تجزیه و تحلیل، همانطور که در ماتریس ریسک نشان داده شده و با داده های کمی اثبات شده است، برای بهینهسازی اولویتبندیهای و فواصل زمانی برای برنامه بازرسی استفاده میشود. اقلام تجهیزاتی که در گوشه سمت راست بالای ماتریس قرار دارند باید اولویت داشته باشند، زیرا این موارد در معرض بیشترین ریسک هستند. این دسته از موارد محتملترین خرابیها با شدیدترین پیامدها و عواقب هستند. در مقابل، مواردی که در گوشه پایین سمت چپ ماتریس قرار دارند، اولویت کمتری دارند، زیرا این موارد کمترین ریسک را دارند.
مانند بسیاری از پدیدههای دیگر، اصل پارتو برای بازرسی مبتنی بر ریسک RBI نیز قابل اجرا است، زیرا مشخص شده است که درصد زیادی از کل ریسک واحد مربوط به درصد نسبتاً کمی از اقلام تجهیزات است. بنابراین، از بین تمام اقلام تجهیزاتی که در واحد صنعتی وجود دارند، باید طرح بازرسی را با تمرکز بر اجزا و تجهیزاتی با بالاترین ریسک بررسی کنیم.
مرحله ۴: طرح و برنامه بازرسی
پس از رتبه بندی ریسک، مهندسان مسئول طرح با همکاری مهندسان متخصص خوردگی سعی میکنند یک طرح و برنامه بازرسی طراحی کنند که در آن اولویت را به اجزا و تجهیزات دارای بالاترین ریسک کل داده شده است. باید توجه داشت که مهم نیست آیا بازرسی انجام شده یا خیر، همواره مکانیزمهای مختلف تخریب و خرابی مواد به گسترش مییابند و کار خود را میکنند. به همین خاطر اجرای بازرسی برای شناسایی، نظارت و سنجش میزان و شدت تخریب این مکانیزمهای تحریب قبل از تبدیل شدن آنها به مشکلاتی گسترده و حیاتی ضروری است. این بازرسیها در اصل با آگاه ساختن تصمیمگیران در خصوص این که چه به داراییهای ثابت میگذرد، تلاشی پایدار و مستمر برای بهروزرسانی برنامه و کاهش ریسک عمل هستند.
منابع و نیروی انسانی محدود یکی از موانع بازرسی کامل و همهجانبهٔ همه داراییهای ثابت است. این محدودیت به خصوص در مواقعی که باید روشهای بازرسی پرهزینه در مدت زمان نسبتاً کوتاهی انجام شوند به چشم میآید. از آنجایی که در طرح بازرسی، منابع بازرسی به داراییهای ثابت با بالاترین پروفایلهای ریسک تخصیص داده میشود، و در این صورت در این طرح از بازرسیهای منظم غیر ضروری در موارد غیر حیاتی اجتناب میشود. به همین خاطر است که در اصل بازرسی مبتنی بر ریسک یا RBI در واقع یک استراتژی کمهزینه در استراتژیهای مختلف نگهداری و تعمیرات است. تا جایی که بر اساس استانداردهای جهانی بکارگیری شیوهٔ بازرسی مبتنی بر ریسک به صورت بلاقوه منجر به صرفه جویی ۲۰ تا ۴۰ درصدی در هزینههای بازرسی میشود.
دستهبندیهای بازرسی
برای شناسایی، طبقه بندی، تجزیه و تحلیل و ارزیابی مکانیزمهای خرابی، در بازرسی مبتنی بر ریسک (RBI) از از سه دسته بازرسی استفاده میشود:
- بازرسی بصری: بازرسی خارجی.
- بازرسی تهاجمی: باز کردن داراییها و تجهیزات برای نمونهبرداری و بررسی خردگی زیر عایق (CUI).
- بازرسی غیر مخرب: آندوسکوپ، جریان گردابی، انتشار صوتی و تجزیه و تحلیل ارتعاش.
رتبهبندی ریسک به صورت مستقیم نوع بازرسی را مشخص نمیکند و این موضوع باید در هر مورد مشخص با انتخاب روش بازرسی که برای تشخیص مکانیزهای زوال و تخریب شدت آن کافی باشد تعیین شود.
موقعیتهای معمولی که در آن مدیریت ریسک از طریق بازرسی ممکن است تأثیر کمی داشته باشد یا هیچ اثری نداشته باشد عبارتند از:
- هنگامی که نرخ خوردگی به خوبی مشخص شده باشد و تجهیزات در حال نزدیک شدن به پایان عمر خود باشند.
- هنگامی که خرابیهای ناگهانی مربوط به شرایط عملیاتی مانند تردشکستها (brittle fracture) اتفاق بیافتد.
- هنگامی که فناوری بازرسی برای تشخیص یا تعیین کمیت خرابی کافی نباشد.
- هنگامی که از شروع خرابی تا خرابی نهایی برای موثر واقع شدن بازرسیهای دورهای (مانند ترکخوردگی خستگی سطحبالا – high-cycle fatigue cracking) در بازهٔ زمانی بسیار کوتاهی اتفاق بیافتد.
- هنگامی که خرابیها رخداد محور (شرایطی که قابل پیش بینی نباشند) باشند.
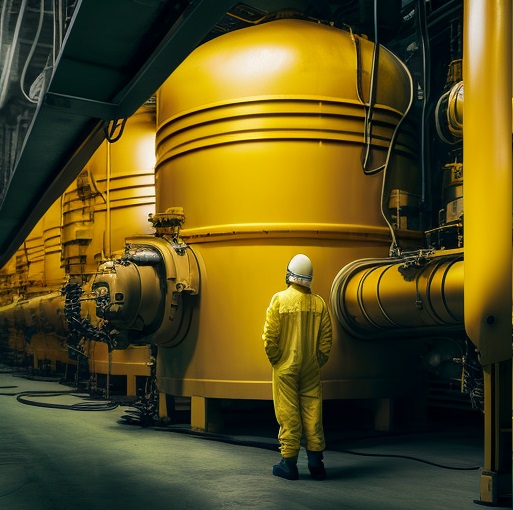
مرحله ۵: کاهش ریسک
اگر بازرسیهای انجامشده نشان دهد که ریسک کلی ذاتی یک تجهیز یا آیتم ثابت در مقایسه با سایر اقلام ثابت ارزیابی شده قابل قبول یا نسبتا کم است، ممکن است اقدامات کاهش بیشتری لازم نباشند. با این حال، از آنجایی که کل ایده بازرسی مبتنی بر ریسک حول محور مقابله با پرریسکترین تجهیزات و اجرای ثابت است، اغلب باید نوعی اقدامات کاهشی را در نظر گرفت. برای کاهش موثر ریسک، میتوانید اقداماتی را مشخص سازید که که پیامدها و احتمالات خرابی را کاهش میدهند. برای جلوگیری از خرابیهای بعدی، ممکن است نیاز به تعمیر، اصلاح، یا نوسازی قطعات یا کوتاه کردن فاصله زمانی بین چرخشها یا بازرسیهای منظم باشد.
بازرسی مبتنی بر ریسک یا RBI به طور بالقوه میتواند به عنوان اهرمی برای نظارت بر وضعیت تجهیز مورد استفاده قرار گیرد، زیرا این امکان را به سازمان میدهد تا اطلاعات آگاهیبخشِ ارزشمندی در مورد تجهیزات یا اجزایی که با بالاترین ریسک در حوزهٔ تجهیزات ثابت روبرو هستند و به صورت معمولمورد بازرسی قرار میگیرند، را در اختیار ذینفعان قرار دهد. هرچند در این مرحله سرمایهگذاری بر تجهیزات و سیستمهای نظارت بر وضعیت تجهیز، مانند حسگرهای پیچیده و سیستمهای نرمافزاری، ولخرجی به نظر برسند اما در طولانی مدت عملکرد مثبت آنها به عنوان یک نوع استراتژی در کاهش ریسک واضح است.
مرحله ۶: ارزیابی مجدد
مراحل قبلی همه در لظحات معینی اتفاق میافتند اما با گذشت زمان، واضح است که با تغییراتی روبرو میشویم که میتوانند بر احتمال یا پیامدهای خرابی تأثیر بگذارند. به همین خاطر، مهم است که در مرحلهٔ ششم دارای یک فرایند مدیریت تغییر موثر باشیم که تشخیص دهد ارزیابی مجدد ریسک چه زمانی ضروری است. موضوعات مورد توجه در ارزیابی مجدد در بازرسی مبتنی ریسک RBI موارد زیر هستند:
- بازرسیها
- ویژگیهای فرایندها و سخت افزارها
- نگهداری و تعمیرات (استراتژیها و رویکردها).
بسیاری از مکانیزمهای تخریب وابسته به زمان هستند. به طور معمول، ارزیابی بازرسی مبتنی بر ریسک یا RBI، تخریب را با نرخی پیوسته و دائمی پیشبینی میکند. نرخهای مربوط به سرعت تخریب ممکن است در طول زمان متفاوت باشند. زیرا از طریق اجرای اقدامات مرتبط با بازرسی، میانگین نرخ خرابی ممکن است در ارزیابی مجدد بهتر شود. اما برخی از مکانیزمهای تخریب مستقل از زمان هستند، به عنوان مثال، برخی از این تخریبها تنها زمانی رخ میدهند که شرایط خاصی به وجود آید. این شرایط ممکن است در ارزیابی اولیه پیشبینی نشده باشد اما بعداً رخ داده باشند. فعالیتهای بازرسی، میزان اطلاعات مربوط به وضعیت تجهیزات را افزایش میدهد و نتایج برآمده از این اطلاعات باید برای تعیین اینکه آیا ارزیابی مجدد RBI ضروری است یا نه در این مرحله بازبینی شوند.
با خلق و استفاده از مدلهای پیشبینیکننده تخریب و خرابی و بکار بستن آنها همراه با بازرسیها و آزمایشهای معمولِ تا حد امکان کارآمد و مؤثر، بازرسی مبتنی بر ریسک یا RBI امکان نظارت طولانیمدت بر داراییهای ثابت را فراهم میکند. رویکرد RBI در دل خود بهبود مستمر را نیز دارد، به این صورت که فرایند RBI باید پس از انجام وارد چرخهٔ تکرار شود و سرمایهگذاریهای لازم برای کاهش ریسک در آن تداوم یابد. به خاطر داشته باشید که همیشه درجاتی از ریسک باقی میماند زیرا تمام ریسکها را هرگز نمیتوان به صورت کامل حذف کرد. هدف بازرسی بر مبنای ریسک کاهش این ریسک باقیمانده به سطحی قابل قبول است.