شاخص OEE (اثربخشی کلی تجهیزات)، یک معیار استاندارد است که برای سنجش بهرهوری و کارایی در صنعت تولید به کار میرود. در این مقاله، به تحلیل روشهای رفع ۶ ضایعه بزرگ در OEE و لزوم استفاده از خدمات Power BI برای دستیابی به نتایج بهتر میپردازیم.
بهرغم چالشهایی مانند اختلالات زنجیره تأمین، کمبود نیروی کار، تورم و محدودیتها که طی چند سال اخیر بازار جهانی را تحت تأثیر قرار داده، صنعت تولید در دستههای مختلف در حال توسعه است. بر اساس دادهها، تولید صنعتی جهانی (بهجز ایالات متحده) در دسامبر 2022 به میزان 1.53٪ افزایش یافت. همچنین، بازارهای نوظهور افزایش 3.3٪ را ثبت کردند، در حالی که تولید صنعتی ایالات متحده در همان دوره 2.07٪ رشد داشت. این افزایشها نشاندهنده پیشرفتهای مهم در صنعت تولید است.
موسسه Deloitte در گزارشی پنج روند برجسته در صنعت تولید برای سال 2023 معرفی کرد. اولین و مهمترین این روندها، سرمایهگذاری در فناوری برای کاهش ریسک است. این موضوع اهمیت بالایی دارد زیرا بسیاری از تولیدکنندگان در تلاش برای بهبود OEE در فرایندهای تولیدی خود هستند.
شش ضایعه بزرگ در OEE میتواند به شدت بر درآمد و رشد یک شرکت تولیدی تأثیر بگذارد. فناوری نقش حیاتی در کاهش این زیانها و افزایش کیفیت کلی، تولید و سودآوری صنعت ایفا میکند. شرکتهای تولیدی با ارائهدهندگان خدمات هوش تجاری همکاری میکنند تا فرایندهای خود را دیجیتالی تحول بخشند و OEE را به طور مؤثر بهبود دهند.
در این مقاله، به بررسی OEE، اتلاف مرتبط با آن و راهکارهای بهبود آن در کسبوکار خواهیم پرداخت.
شاخص OEE چیست؟
شاخص OEE، یا اثربخشی کلی تجهیزات، به عنوان یک معیار برجسته برای ارزیابی بهرهوری تولیدی شناخته میشود. سازمانی که دارای OEE بالاتری است، به معنای تولید بیشتر، استفاده بهینهتر از منابع و کاهش نقصها و هدررفتها میباشد. برای ارزیابی OEE، سه شاخص کلیدی مورد توجه قرار میگیرد: کیفیت، عملکرد و زمان. OEE به سه بخش اصلی تقسیم میشود: توقفهای مرتبط با دسترسی به تجهیزات، توقفهای عملکردی و کیفیت.
اثربخشی کلی تجهیزات (OEE) به صنعت کمک میکند تا با بهبود فرایندها، مقایسه پیشرفتها و کاهش ضایعات، بهرهوری تجهیزات را بهبود بخشد. کسبوکاری که به 100% OEE دست یابد، به عنوان کسبوکاری کامل شناخته میشود، در حالی که OEE 85% یا بیشتر، در سطح کلاس جهانی قرار دارد. به طور معمول، صنایع OEE حدود 60% دارند و هر مقداری نزدیک به 40% یا کمتر به عنوان OEE پایین محسوب میشود. این نشاندهنده نیاز به رفع مشکلات و کاهش ضررها برای دستیابی به نتایج بهتر است.
فرمول محاسبهٔ شاخص OEE
متداولترین روش برای محاسبهٔ شاخص OEE ضرب سه عامل در یکدیگر است: میزان دسترسیپذیری تجهیز، عملکرد تجهیز و کیفیت تولید. هر کدام از این عاملهای مختلف، بخش مختلفی از کار یک تجهیز و نحوه عملکرد آن در حوزهٔ مشخص خود را اندازهگیری میکند.
- دسترسیپذیری: تجهیز در موارد نیاز تا چه اندازهای در دسترس و قابل بهرهبرداری است؟
- عملکرد: میزان تولید و خروجی تجهیز چهقدر است؟
- کیفیت: میزان تولید با کیفیت بالای تجهیز چه میزان است؟
در ادامه برای هر سه عامل بالا فرمول شاخص OEE را تجزیه کنیم:
دسترسیپذیری = مجموع زمان کار کلی یک تجهیز ÷ مجموع زمان برنامهریزیشده کار یک تجهیز
عملکرد = خروجی واقعی سیستم ÷ حداکثر خروجی ممکن
کیفیت = تعداد محصول قابلاستفاده و مورد پذیرش ÷ تعداد کل واحدهای تولیدشده
در ادامه نگاه عمیقتری به هر یک از این محاسبات میاندازیم. به یاد داشته باشید که هنگام محاسبات این ارقام، خاموشیهای برنامهریزیشدهٔ تجهیز ناشی از برنامههای نت پیشگیرانه، خاموشی در تعطیلات و دورههای مشابه را حذف کنید. وقتی این سه عدد را داشته باشیم، به راحتی میتوانیم از آنها برای محاسبهٔ شاخص اثربخشی کلی تجهیزات استفاده کنیم.
شاخص OEE = دسترسیپذیری x کیفیت x عملکرد
۶ ضایعه بزرگ در OEE چیست؟
پیش از اینکه یاد بگیریم چگونه اثربخشی کلی تجهیزات (OEE) را بهبود بخشیم، ابتدا باید ۶ ضایعه بزرگ را که بر صنعت تولید تأثیر میگذارند، درک کنیم.
۱. خرابی تجهیزات
خرابی و نقص تجهیزات باعث از دست رفتن زمان و کاهش بهرهوری در یک شرکت میشود. این معمولاً به عنوان از دست دادن دسترسیپذیریپذیری دستهبندی میشود زیرا زمان توقف غیر برنامهریزی شده است. وقتی تجهیزات در زمانی که انتظار میرود کار کنند، متوقف میشوند، منجر به اتلاف زمان (که همه چیز را از برنامه عقب میاندازد) و بهرهوری (کارخانه به دلیل خرابی یا نقص تجهیزات، مقدار کمتری کالا تولید میکند) میشود.
این نوع اتلاف همچنین میتواند شامل جنبههای مرتبطی مانند خرابی ابزار، نگهداری و تعمیرات برنامهریزی نشده، کمبود مواد یا اپراتور، یا به دلیل انسداد در هر دو طرف فرایند تولید باشد. به عنوان مثال، اگر تولید یک محصول خاص شامل هشت مرحله باشد، اختلال در مرحله سوم بر مرحله چهارم تأثیر میگذارد، همانطور که اختلال در مرحله پنجم نیز تأثیرگذار است.
۲. زمان تنظیم و راهاندازی تجهیز
دومین نوع اتلاف OEE در تولید مربوط به عدم دسترسیپذیری تجهیزات به دلیل تنظیمات، نصب، سفارشیسازی یا سایر نیازهای نصب و تنظیم تجهیز است. این مدت زمانی است که ماشین باید در حال کار باشد اما به جای آن در حال تنظیم شدن است (به دلایل مختلف).
اگرچه این مسئله به عنوان تلفات دسترسی نیز شناخته میشود، اما در دسته توقفهای برنامهریزی شده قرار میگیرد. دلیل این توقفها این است که کارگران یا تکنسینها باید قبل از شروع مجدد، تجهیزات را تنظیم کنند. تمیزکاری، نگهداشت دورهای، زمان گرم شدن و خنک شدن، و بازرسیهای کیفی از جمله این موارد هستند.
۳. اتلاف وقت و توقفات جزئی
توقف یا وقفه جزئی به زمانی کوتاه اطلاق میشود که اپراتور ماشین به منظور حل یک مشکل، کار دستگاه را متوقف میکند. این مدت معمولاً یک یا دو دقیقه برای هر توقف است. به دلیل اینکه تجهیزات در دسترسیپذیری و در حال کار هستند؛ اما در این مدت کوتاه تولیدی انجام نمیدهند، این وقفهها به عنوان اتلاف عملکرد دستهبندی میشوند.
توقفات جزئی میتواند شامل بیکاری ماشین به دلیل تأخیر کوتاه در تغذیه مواد ورودی، تنظیمات نادرست، سنسورهای ناهماهنگ، گرفتگی مواد، پیچیدگیهای طراحی و جلسات پاکسازی اجباری دورهای باشد. همه انواع توقفات یا وقفههای تولیدی که کمتر از پنج دقیقه برای هر دوره باشند، تحت این نوع از اتلاف OEE قرار میگیرند. این توقفات میتوانند به سختی ردیابی شوند و در صورت نادیدهگرفتن منجر به خرابیهای عمده شوند.
۴. کاهش سرعت
سرعت کاهش یافته به دورهای اشاره دارد که تجهیزات با سرعتی کمتر از زمان چرخه ایدهآل کار میکنند، و در نتیجه تعداد کالاهای تولیدی کمتر از حد انتظار است. این موضوع به عنوان اتلاف عملکرد دستهبندی میشود، زیرا تجهیزات به اندازهای که معمولاً تولید میکنند، کالا تولید نمیکنند. زمان چرخه ایدهآل، سریعترین زمانی است که برای ساخت یک محصول ممکن است و یک مقدار نظری است که بر اساس مشخصات داده شده ماشین محاسبه میشود.
دلایل متعددی میتوانند منجر به کاهش سرعت شوند. چند علت رایج عبارتند از نگهداشت نامناسب تجهیزات، روانکاری ضعیف، گیر کردن مواد، قطعات یدکی فرسوده، محیط کاری نامناسب (غیرقابلتولید)، مواد خام یا ورودی با کیفیت پایین، اپراتورهای کمتجربه و خاموشیهای ناگهانی.
۵. نقصهای تولید
نقص فرایند به مواردی اشاره دارد که در هر دسته تولیدی، علیرغم پایداری فرایند تولید، ممکن است برخی قطعات یا کالاهای معیوب وجود داشته باشد. محصولات دورریختنی و محصولاتی که قابل بازکاری یا استفاده مجدد هستند، در این اتلاف محاسبه میشوند. OEE کیفیت را بر اساس اولین بازده عبور اندازهگیری میکند، که این موضوع نقض فرایند را به یک مسئله اتلاف کیفیت تبدیل میکند. اگر کیفیت محصولات خوب باشد، به عنوان معیوب علامتگذاری نمیشوند.
نقضهای فرایند میتواند به دلایل مختلفی از جمله تنظیمات نادرست یا غلط، ارائه مواد اولیه اشتباه به تجهیزات، ناکارآمدی اپراتور، یا انقضای مواد (که معمولاً در صنایع داروسازی و غذایی یافت میشود) اتفاق بیافتد.
۶. نقصهای راهاندازی
آخرین اتلاف OEE کاهش یا ضایعات بالاتر ناشی از نقضهای فرایندی است. کاهش بازده نیز به عنوان اتلاف کیفیت دستهبندی میشود. اگرچه این مسئله میتواند در هر مرحلهای از تولید رخ دهد، کاهش یا بازده کمتر عمدتاً پس از تغییرات (با تناوب بالا) مشاهده میشود. این مسئله نیز از منظر اولین بازده عبور محاسبه میشود.
کاهش بازده یا بازده کمتر به دلایل مختلفی مانند تنظیمات نادرست، تغییرات کمتر از بهینه، اجرای نادرست چرخههای گرم کردن، یا استفاده از تجهیزاتی که پس از راهاندازی ضایعات ایجاد میکنند، رخ میدهد.
چگونه ۶ ضایعه بزرگ را اندازهگیری کنیم؟
برای اندازهگیری ۶ ضایعه بزرگ، نیاز به جمعآوری دادههایی درباره عملکرد تجهیزات خود دارید، مثل زمان کارکرد، زمان توقف، زمان چرخه، خروجی و نقایص. میتوانید از روشهای دستی یا خودکار، مثل چکلیستها، لاگها، حسگرها یا نرمافزار استفاده کنید. دادهها باید دقیق، قابل اعتماد و سازگار باشند.
پس از بدست آوردن داده ها، میتوانید OEE و اجزای آن را با استفاده از فرمول های زیر تجزیه کنید:
- دسترسیپذیرییپذیری = مجموع زمان کار کلی یک تجهیز ÷ مجموع زمان برنامهریزیشده کار یک تجهیز
- عملکرد = خروجی واقعی سیستم ÷ حداکثر خروجی ممکن
- کیفیت = تعداد محصول قابلاستفاده و مورد پذیرش ÷ تعداد کل واحدهای تولیدشده
- شما همچنین میتوانید درصد هر اتلاف را با استفاده از فرمولهای زیر محاسبه کنید:
- اتلاف خرابی = (زمان توقف به دلیل خرابی / زمان برنامهریزی تولید) × ۱۰۰
- اتلاف تنظیمات و راهاندازی = (زمان توقف به دلیل تنظیمات و تنظیم مجدد / زمان برنامهریزی تولید) × ۱۰۰
- اتلاف وقف و توقفات جزئی = (زمان توقف به دلیل بیکاری و توقفات جزئی / زمان برنامهریزی تولید) × ۱۰۰
- اتلاف سرعت کاهش یافته = (خروجی ایدهآل – خروجی واقعی) / خروجی ایدهآل × ۱۰۰
- اتلاف نقایص و بازکاری = (نقایص + بازکاری) / خروجی واقعی × ۱۰۰
- اتلاف راهاندازی = (خروجی ایدهآل – خروجی بدون نقص) / خروجی ایدهآل × ۱۰۰
نحوۀ بهبود شاخص اثربخشی کلی تجهیزات
شاخص اثربخشی کلی تجهیزات (OEE) یک عدد قابل اندازهگیری است. بسیاری از کسبوکارهای تولیدی به دنبال روشهایی برای بهبود امتیاز OEE هستند که در نهایت نشاندهنده ارزشهای تولیدی با کیفیت بالا است. استراتژیهای محبوبی مانند نگهداری و تعمیرات بهرهور فراگیر (TPM) و مدیریت ناب از نمودارهای OEE برای ایجاد رویههای بهتر و بهبود کیفیت کلی محصولات استفاده میکنند.
در اینجا نحوه حل ۶ ضایعه بزرگ در OEE در تولید آمده است:
۱. محاسبه OEE
برای شروع، اولین قدم محاسبه OEE است. باید بدانید وضعیت کسبوکار شما در حال حاضر چگونه است تا بتوانید بهبودها را شروع کنید. این کمک میکند که نقاط مشکلدار را به درستی شناسایی کرده و راهحلهای مناسبی پیدا کنید. با اینکه فرمول OEE ساده است، اما محاسبه آن میتواند پیچیده و گیجکننده باشد. همچنین، استفاده از دادههای نادرست یا قدیمی میتواند منجر به امتیاز اشتباه شود. بهتر است در داخل نرم افزار نگهداری و تعمیرات خود تا یک داشبورد سفارشی OEE تنظیم کرده و امتیاز را به صورت لحظهای دریافت کنید.
۲. دیجیتالیسازی
دیجیتالی شدن فرایندی است که از جدیدترین تکنولوژیها برای خودکارسازی و ارتقاء سیستمها به منظور دستیابی به نتایج بهتر استفاده میکند. زیانهای کوچک، سرعتهای چرخه کندتر و غیره نمیتوانند در بلندمدت به درستی اندازهگیری شوند مگر اینکه ابزار دقیقی برای ثبت هر توقف یا تاخیر داشته باشید. دیجیتالی شدن این امکان را با یکپارچهسازی برنامههای لازم با تجهیزات و سادهسازی جریان دادهها در کارخانه فراهم میکند. دستگاههای اینترنت اشیا (IoT) دادهها را به صورت لحظهای از تجهیزات جمعآوری کرده و به سرپرستان کمک میکنند تا تأخیرها، خطاها، خرابیها و غیره را پرچمگذاری کنند.
۳. سیستمهای مدیریت دانش
سیستم مدیریت دانشی را بسازید که به راحتی توسط اپراتورها و کارگران در کارخانه قابل دسترسیپذیریی باشد. این سیستم میتواند زمان مناسب برای برنامهریزی بررسیهای نگهداری پیشگیرانه را به کارکنان پیشنهاد دهد، هشدارهایی برای تعویض روغنها ارسال کند و یک چکلیست ایجاد کند تا اطمینان حاصل شود که احتمال خرابی ماشینآلات به دلیل تعمیرات یا قطعات یدکی آسیبدیده به حداقل برسد. با توجه به اینکه برنامههای نگهداشت میتوانند در زمانهای غیرتولیدی برنامهریزی شوند، کسبوکار میتواند تأخیرها و ضایعات را کاهش دهد.
۴. تعویض تکدقیقهای قالب (SMED)
تکنیک SMED اصلیترین اصل تولید ناب است. این تکنیک زمان تغییر تجهیزات را با سادهسازی فرایند کاهش میدهد. هدف این است که زمان تغییر به یک رقم کاهش یابد. این امر هزینههای تولید را کاهش میدهد و تغییرات در محصولات را بدون از دست دادن سرمایه زیاد آسانتر میکند. زمانی که تولیدکنندگان یک سیستم به خوبی کارآمد داشته باشند، کارگران میتوانند اندازه دستهها را افزایش دهند تا کالاهای بیشتری در دستههای کمتر تولید شود. این به استانداردسازی فرایندها برای افزایش کارایی کلی معروف است. این تکنیک همچنین تنوعهایی که منجر به تولید کالاهای معیوب و ضایعات میشوند را کاهش میدهد.
چگونه ضایعههای دسترسیپذیریپذیری را کاهش دهیم؟
دو مورد اول از ۶ ضایعه بزرگ در امتیاز دسترسیپذیریپذیری شما قرار میگیرند و مربوط به حفظ فرایند به کارگیری تجهیزات تا حد امکان هستند. اگر امتیاز دسترسیپذیریپذیری شما پایین است، باید به اعداد مربوط به زمان کارکرد واقعی و زمان برنامهریزی تولید نگاه دقیقی بیندازید.
از دست دادن برنامه در محاسبات OEE در نظر گرفته نمیشود زیرا وقتی تولید نباید انجام شود، اندازهگیری OEE بیمعنی است. از دست دادن برنامه برای محاسبه TEEP (عملکرد کلی تجهیزات موثر) استفاده میشود.
اولین ضایعه بزرگ: خرابیهای تجهیزات (زمان توقف برنامهریزی نشده)
خرابی تجهیزات منبع مهمی از توقفهای برنامهریزی نشده و بیکاری هستند. اگر زمان توقف برنامهریزی نشده چیزی است که زمان کارکرد شما را کاهش میدهد، این همان جایی است که باید شروع کنید.
راهحلها عبارتند از:
- ایجاد یک برنامه نگهداری و تعمیرات پیشگیرانه قوی. یا اگر ممکن است، از حسگرها در مهمترین داراییهای تولیدی خود استفاده کنید و از نگهداری و تعمیرات مبتنی بر وضعیت یا نت پیشبینانه استفاده کنید.
- پیادهسازی یک CMMS پیشرفته مانند سیستم نگهداری و تعمیرات پگاه آفتاب. این سیستم به شما کمک میکند تا از برنامههای نت پیشگیرانه (PM) بیشترین بهره را ببرید، خرابیها را کاهش دهید و عملکرد تجهیزات را به حداکثر برسانید.
- پیگیری زمانهای توقف شما. بیشتر نرمافزارهای CMMS دارای ماژولهایی برای ردیابی توقفها و دلایل آنها هستند. راهکار نرمافزاری نگهداری و تعمیرات پگاه آفتاب این کار را با داشبوردهای سفارشی که به شما اجازه میدهد به طور خودکار گزارشهایی از مشکلات تجهیزات دریافت کنید، ساده میکند. آنها به شما کمک میکنند تا بزرگترین مشکلات را شناسایی کنید تا بتوانید آنها را در زمان مناسب تعمیر یا تعویض کنید.
- پیشبینی و اجرای اقدامات برای جلوگیری از توقفها. زمانی که الگوهایی در زمانهای توقف خود پیدا کردید، میتوانید از آنها جلوگیری کنید. اگر یک تجهیزات پس از یک دوره مشخص از زمان کار متوقف میشود، شیفتهای خود را بر اساس آن برنامهریزی کنید تا یک راهحل بلندمدت پیدا کنید.
دومین ضایعه بزرگ: تنظیم و راهاندازی (زمان توقف برنامهریزی شده)
تنظیم و راهاندازی تجهیزات زمانبر هستند و نمیتوان از آنها گریخت. خبر خوب این است که این موارد به ما فضایی برای بهبود میدهند. انجام آنها در زمان مناسب و به روش صحیح، میتواند به حداقل رساندن اتلافهای تولید کمک کند.
برای کاهش تعداد و طول این توقفهای برنامهریزی شده:
- دستههای بزرگتر به معنای دستههای کمتر و تغییرات کمتر تجهیزات در کارگاه شما است. اگر بتوانید به دقت تعداد کل واحدهایی که در نهایت نیاز دارید را پیشبینی کنید، میتوانید تولید خود را بسیار کارآمدتر برنامهریزی کنید. (اگر از سیستم تولید پیوسته استفاده میکنید، نیازی به نگرانی در این مورد نخواهید داشت.)
- پیادهسازی تکنیک تعویض قالب در یک دقیقه (SMED). تکنیک SMED یکی از اصول تولید ناب است. با دقت به آنچه که در طول توقفهای برنامهریزی شده رخ میدهد نگاه کنید. به دنبال راههایی برای حذف یا کوتاه کردن مراحل باشید. هدف شما باید این باشد که توقفها را تا حد ممکن سریع انجام دهید – به زمانی نزدیک به یک یا تکرقمی دقیقه برسید.
چگونه ضایعههای عملکرد را کاهش دهیم؟
بیایید درباره دو ضایعه بعدی که مربوط به امتیاز عملکرد شما هستند صحبت کنیم. این دو ضایعه شامل کاهش سرعت و توقفات جزئی میشوند. رسیدگی به این دو مشکل به شما کمک میکند تا تولید خود را به حداکثر برسانید.
اگر امتیاز عملکرد شما پایین است، باید به بررسی ثبات زمان اجرای و زمان چرخه بپردازید.
سومین ضایعه بزرگ: توقفات جزئی
نظارت بر توقفات جزئی امری دشوار است و ممکن است به کلی نادیده گرفته شوند. واقعیت این است که بسیاری از توقفات کوچک که در یک فرایند تولید بزرگمقیاس رخ میدهند، به سرعت جمع میشوند. اینجا جایی است که باید شروع کنید.
رسیدگی به انحرافات به صورت لحظهای
با رسیدگی به انحرافات در زمان واقعی و آموزش اپراتورهای ماشین برای رفع مشکلات جزئی در محل، میتوان مبنایی برنامه نگهداری و تعمیرات مستقل یا خودگردان (“AM”) ایجاد کرد و زمان زیادی را صرفهجویی کرد. تیم نگهداشت شما میتواند برای خرابیهای جدیتر تجهیزات آزاد شود و تیم تولید شما نیازی به انتظار برای رفع یک خرابی جزئی نخواهد داشت.
اگر یک سیستم نگهداری و تعمیرات مانند CMMS پگاه آفتاب استفاده میکنید، یک ابزار عالی برای شروع نت مستقل (AM) در اختیار دارید. با دادن دسترسیپذیریی به سیستم، کارکنان میتوانند با اپلیکیشن موبایل CMMS، تمام کمکها و دستورالعملهای لازم را به راحتی در دسترسیپذیری خود داشته باشند.
پیروی کردن از الگوهای کاهش عملکرد
چه زمانی توقفهای جزئی یا چرخههای آهسته بیشتر اتفاق میافتد؟ الگوهای موجود در این دادهها میتوانند به شما کمک کنند تا علت اصلی را پیدا کرده و از آن جلوگیری کنید.
- آیا تولید در یک شیفت خاص کاهش پیدا میکند؟
- پس از نگهداری روتین یا برنامهریزی شده؟
- بعد از یک مقدار معین از زمان کارکرد؟
استانداردسازی فرایندها
استانداردسازی فرایندها به دلیل وجود رویههای استاندارد عملیاتی (SOPs) اهمیت دارد. این رویهها معمولاً به خوبی تدوین شده و به طور کامل آزمایش شدهاند. همانطور که قبلاً گفته شده و دوباره میگوییم: یک فرایند واحد و یکسان را هر بار دنبال کنید تا اشتباهات و توقفات جزئی کاهش یابند. به همین دلیل است که بسیاری از سازمانها تلاش میکنند فرایندها را هر جا که ممکن است، اتوماسیون کنند.
چهارمین ضایعه بزرگ: کاهش سرعت
کاهش سرعت معمولاً نتیجه استهلاک، نگهداشت ضعیف یا استفاده نادرست است. این موضوعی است که ما انسانها به خوبی درک میکنیم.
با گذشت زمان، ممکن است کندتر شویم. اما با داشتن یک برنامه ورزشی مناسب و مراقبت از خود، میتوانیم برای مدت طولانی با سرعت خوبی به کار ادامه دهیم.
بهینهسازی چرخه و سرعت تولید
این کار را برای تجهیزات خود نیز انجام دهید. نگهداشت تجهیزات در شرایط ایدهآل، بهترین راه برای حفظ سرعت تولید است.
هر اقدامی که برای بهبود برنامه نت پیشگیرانه (PM) لازم است انجام دهید. اپراتورهای دستگاههای خود را آموزش دهید تا از تجهیزات بهدرستی استفاده و مراقبت کنند. و مهم است که قدردان آنها باشید؛ مهم این است که بهخوبی از آنها مراقبت کنید.
چگونه ضایعههای مرتبط با کیفیت را کاهش دهیم؟
اگر امتیاز کیفیت کمتر از 100% باشد، به این معنی است که در فرایند تولید برخی کالا معیوب تولید میشوند.
هرچه امتیاز کیفیت پایینتر باشد، درصد قطعات معیوب بیشتر است. باید به فرایندهای تولید و تجهیزاتی که در آنها امتیاز کیفیت پایینتری دارید، نگاه دقیقی بیندازید و نقاط ضعف را شناسایی کنید.
پنجمین ضایعه بزرگ: ضایعات محصول
بسیاری از نقصها به دلیل فرسایش تجهیزات شما رخ میدهد. انواع نقصهایی که مشاهده میکنید را ردیابی کنید و تجهیزات کهنه را به دقت نظارت کنید.
ممکن است تیم نگهداشت بسیار ماهری داشته باشید که بتواند تجهیزات را در حال کار نگه دارد، اما زمانی میرسد که کاهش سرعت و تعداد نقصها و بازکاریها دیگر ارزش نگهداشتن آن دارایی را نخواهد داشت. در آن زمان، تعویض تجهیزات منطقیتر خواهد بود.
ششمین ضایعه بزرگ: ضایعات راهاندازی
کاهش تولید در شروع کار
این آسان است که وقتی تجهیزات قدیمی را جایگزین میکنید، هیجانزده شوید. تجهیزات قدیمی ممکن است مدتها کند و ناکارآمد بودهاند که احساس کنید باید زمان از دسترفته را جبران کنید.
مقاومت در برابر وسوسه افزایش سریع سرعت در ابتدای کار اهمیت دارد. اما ممکن است چندین دسته تولیدی زمان ببرد تا محصول به استانداردهای کیفی شما برسد.
در این مدت به دستههای کوچکتر پایبند باشید. این کار به شما اجازه میدهد مشکلات را پیدا و رفع کنید قبل از اینکه به سرعت کامل برسید، و زمان و مواد را از ضایعات راهاندازی نجات دهید.
کاهش تغییرات کیفیت
پس از نصب و راهاندازی تجهیزات جدید و شروع به کار خوب آنها، تصور نکنید که این وضعیت پایدار خواهد بود. تنظیمات به مرور زمان ممکن است تغییر کنند و مواد نیز دستخوش تغییر میشوند. در روزهای ابتدایی، تنظیمات و مواد را به دفعات بررسی کنید تا بتوانید هر گونه تغییر را به سرعت برطرف کنید.
چگونه ۶ ضایعه بزرگ را تحلیل کنیم؟
برای تحلیل ۶ ضایعه بزرگ، باید علل اصلی و تأثیر هر ضایعه بر عملکرد تولید خود را درک کنید. میتوانید از ابزارها و تکنیکهای مختلفی مانند نمودارهای پارتو، نمودارهای استخوان ماهی، روش ۵ چرا، یا ماتریسهای علت و معلول استفاده کنید. این ابزارها به شما کمک میکنند تا مهمترین ضایعات را اولویتبندی کرده و موثرترین راهحلها را پیدا کنید.
شما باید از این نکته لذت ببرید که میتوانید امتیاز OEE خود و بخشهای آن را با استانداردهای صنعت خود یا بهترین روشها مقایسه کنید. این کار میتواند به شما کمک کند تا اهداف واقعی و قابل دستیابی برای بهبود را تعیین کنید.ذهمچنین میتوانید از پایگاههای دادههای آنلاین، گزارشها یا نظرسنجیها برای پیدا کردن اطلاعات مرجعی برای بخش یا فرایند خود استفاده کنید.
جمعبندی
تیمهای موفق در نگهداشت و تولید روی تمرین مداوم، بهرهگیری از ابزارهای مناسب و بهبود مستمر تمرکز میکنند.
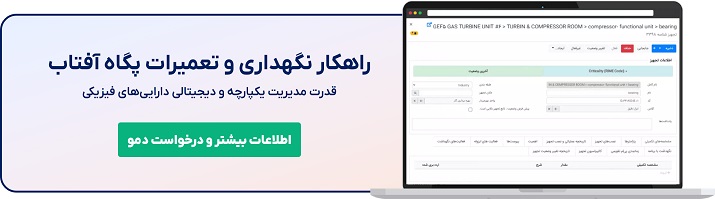
یک نرم افزار نگهداری و تعمیرات مانند محصول CMMS پگاه آفتاب میتواند کلید اصلی در حل برخی از رایجترین اتلافات بهرهوری باشد. ما یک پلتفرم آسان برای استفاده ارائه میدهیم که به شما امکان میدهد تا نگهداشت تجهیزات را بهینهسازی کنید، گزارشدهی دقیق داشته باشید و عملکرد این بخش را بهبود بخشید. با درخواست دمو، ما آمادهٔ مشاوره و راهنمایی شما در این رابطه هستیم.