این راهنمای مفصل به بررسی جنبههای مختلف مدیریت انبار میپردازد: از تاریخچه، شکل مدرن آن، اتوماسیون و وظایف تا ذینفعان، چالشها و چشمانداز آینده.
امروزه، انبارها، به ویژه مراکز توزیع، در قلب عملیات تجارت و بازرگانی قرار دارند. هنگامی که مشتری سفارشی را به صورت آنلاین ثبت میکند، این انبار است که آن سفارش را پردازش میکند، محصول مناسب را انتخاب میکند، آن را به طور ایمن بستهبندی میکند و برای ارسال آماده میکند.
پیشرفتهای فناورانه، همراه با رشد چشمگیر تجارت، منجر به رشد انواع مختلف انبارها شده است. این انبارها به گروههای جمعیتی هدف خدمت میکنند و اهداف خاصی دارند.
مراکزی برای توزیع وجود دارند که انبارهای بزرگ معمولی هستند که کالاها قبل از توزیع به خردهفروشان یا مشتریان به طور موقت در آنها نگهداری میشوند. سپس مراکز توزیعی وجود دارند که عمدتاً برای عملیات تجارت الکترونیک استفاده میشوند.
برای پاسخگویی به تقاضاهای توزیع چندکاناله، مراکز توزیع خردی داریم که نسخههای کوچکتر مراکز توزیع هستند و نزدیکتر به مشتری نهایی قرار دارند، و فروشگاههایی که منحصراً به خرید آنلاین خدمات میدهند.
این انبارها به یک فرایند سیستماتیک برای سادهسازی ذخیرهسازی، سازماندهی و مدیریت محصولات در انبار نیاز دارند. برای جابجایی کارآمد محصولات در فرایند انجام سفارش، انبارداری بزرگترین عامل تمایز رقابتی است.
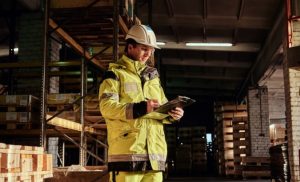
مدیریت انبار چیست؟
مدیریت انبار، مدیریت مؤثر کالاهایی فیزیکی است که قرار است در مراحل بعدی زنجیره تأمین به مصرفکنندگان نهایی فروخته شوند. این مجموعه فرایندهایی است که بر ذخیرهسازی کالاهای فیزیکی و همچنین جابجایی آنها در سراسر انبار برای انجام سفارش مشتری نظارت میکند.
به طور کلی، این امر شامل برداشت و بستهبندی، ردیابی موجودی، پیشبینی الگوهای تقاضا، بهینهسازی ذخیرهسازی، افزایش امنیت و بهبود کارایی کلی زنجیره تأمین است. هدف اصلی مدیریت انبار اطمینان از اجرای مؤثر عملیات روزانه در یک انبار و بهینهسازی فرایندها در هر کجا که ممکن باشد، است.
تاریخچه مختصر مدیریت انبار
منشأ انبارها به هزاران سال پیش و به مصر باستان بازمیگردد، جایی که انبارهای مرکزی بزرگ بهعنوان پیشزمینهای برای انبارهای مدرن عمل میکردند. با گذشت زمان، این انبارها به محلهای ذخیرهسازی و تالارهای صنفی تبدیل شدند که از شبکههای تجاری پیچیده درونمرزی و بینالمللی پشتیبانی میکردند.
نیمه دوم قرن بیستم
در نیمه دوم قرن بیستم، کد جهانی محصول (UPC) یا بارکد به یک استاندارد تبدیل شد. طولی نکشید که پیشرفتهای فناوری به اختراع اولین سیستم مدیریت انبار (WMS) منجر شد.
در سال ۱۹۷۵، شرکت خردهفروشی پوشاک J.C. Penney برای اولین بار از یک سیستم مدیریت انبار استفاده کرد و دوران جدیدی را برای لجستیک و مدیریت زنجیره تأمین رقم زد. پیشرفتها به سمت اتوماسیون متمرکز شدند و هم پیشرفتهای فیزیکی و هم نرمافزاری را تحت تأثیر قرار دادند.
تجهیزات انبار مانند نوارهای نقاله، قفسههای با چرخش دورانی و ابزارهای دیگر، حرکت محصولات در داخل انبار را خودکار کردند. از سوی دیگر، پیشرفت در سیستمهای مدیریت انبار (WMS) از وظایف پرزحمتی مانند مدیریت سفارشها، موجودیگیری، انتخاب و بستهبندی، ایجاد وظایف و موارد دیگر پشتیبانی کرد.
انبارهای عصر حاضر
انبارهای امروزی به اکوسیستمهای پیچیدهای تبدیل شدهاند: آنها حجم عظیمی از سفارشات را از طریق یکپارچهسازی با ابزارهای مبتنی بر اینترنت اشیا (IoT)، هوش مصنوعی، یادگیری ماشین و بلاک چین مدیریت میکنند.
ابزارهای مدیریت انبار میتوانند با سیستمهای مختلفی مانند حسابداری، سیستمهای برنامهریزی منابع سازمانی (ERP) و موارد دیگر یکپارچه شوند تا ارتباطات را اتوماسیون کرده و وظایف مدیریت انبار را با حداقل دخالت انسان انجام دهند.
تکامل سیستمهای مدیریت انبار، درست مانند پیشرفت خود انبارداری، میتواند به چهار مرحله مجزا تقسیم شود – WM 1.0، WM 2.0، WM 3.0 و در نهایت، WM 4.0. خدمات مدیریت انبار هر بار که پیشرفتهای فناورانه عمده، روندهای اقتصاد کلان و تغییراتی در رفتار مصرفکننده وجود داشته، تکامل یافته است.
مدیریت انبار نسل WM 1.0 : دوران فرایندهای دستی
اولین شکل مدیریت انبار بهطور کامل بر فرایندهای دستی متکی بود. این دوران که قبل از ظهور فناوریهای دیجیتال بود، بر استفاده از اسناد فیزیکی و تلاش انسانی برای ردیابی و مدیریت موجودی تمرکز داشت. هر کالایی که وارد یا از انبار خارج میشد، باید بهصورت دستی ثبت میشد، که اغلب منجر به بروز خطا، گم شدن کالاها و ناکارآمدیها میشد.
بااینحال، به دلیل سرعت کندتر تجارت، زنجیرههای تأمین سادهتر و حجم نسبتاً کمتر کالاها، این سیستمهای دستی قابل مدیریت بودند.
مدیریت انبار نسل WM 2.0 : مولود رایانه و اتوماسیون
با ورود به قرن بیستم، کسبوکارها شروع به استفاده از سیستمهای کامپیوتری پیشرفته کردند که نشاندهنده آغاز دوره WM 2.0 بود. نسخههای اولیه سیستمهای مدیریت انبار (WMS) ابتدایی بودند و تنها قابلیتهای پایهای مانند ردیابی موجودی و مدیریت داده را ارائه میدادند.
معرفی فناوریهایی مانند بارکد در دهههای ۱۹۷۰ و ۱۹۸۰، ردیابی موجودی را آسانتر و کارآمدتر کرد. این دوره همچنین شاهد اولین استفادهها از سیستمهای انبارداری خودکار بود که در آن لیفتراکها و نوار نقالهها سرعت عملیات را افزایش دادند.
صنعتیسازی و جهانیسازی از عوامل کلیدی در توسعه ابزارهای مدیریت انبار بودند، زیرا کسبوکارها با زنجیرههای تأمین پیچیدهتر و حجم بالاتری از کالاها مواجه شدند.
مدیریت انبار نسل WM 3.0: انبار پیشرفته و اتصالپذیر
اواخر قرن بیستم و اوایل قرن بیست و یکم، ظهور WM 3.0 را رقم زد که با ابزارهای پیشرفته مدیریت انبار و اتصالپذیری بهبودیافته شناسایی میشود. این سیستمها ردیابی موجودی به صورت آنی، پیشبینیپذیری بهبودیافته و هماهنگی بهتر بین بخشهای مختلف زنجیره تأمین را ارائه میدادند.
ظهور اینترنت و بهبود در فناوریهای ارتباطی، تبادل اطلاعات بین سیستمها و مکآنهای مختلف را سادهتر کرد و دید زنجیره تأمین را تا حد زیادی بهبود بخشید. افزایش محبوبیت تجارت الکترونیک و تغییر ناشی از آن در رفتار مصرفکننده به سمت خرید آنلاین، نقش مهمی در شکلدهی خدمات مدیریت انبار ایفا کرد.
مدیریت انبار نسل WM 4.0: دوران هوش مصنوعی، اینترنت اشیاء و رباتیک
در حال حاضر در میانه گذار از WM 3.0 به WM 4.0 هستیم. مدیریت انبار نسل WM 4.0 سناریویی است که در آن ابزارهای مدیریت انبار با یکپارچه شدن با اینترنت اشیا (IoT)، هوش مصنوعی (AI)، یادگیری ماشین، رباتیک و موارد دیگر شناسایی میشوند. تجزیه و تحلیل پیشرفته و یادگیری ماشین امکان مدلسازی پیشبینی را فراهم میکند و پیشبینی بهتر تقاضا و تخصیص بهینه منابع را ممکن میسازد.
رباتیک و اتوماسیون بسیار پیچیدهتر شدهاند و قادر به انجام وظایف پیچیده گزینش و بستهبندی هستند. اینترنت اشیاء ردیابی و نظارت بر موجودی را ب صورت آنی و در لحظه فراهم میکند.
هوش مصنوعی میتواند در تصمیمگیریهای استراتژیک بر اساس مجموعههای کلان داده کمک کند. غولهای تجارت الکترونیک مانند آمازون در استفاده از فناوری و ادغام اکوسیستمها برای سادهسازی فرایندهای مدیریت انبار و سادهسازی انجام سفارش مشتری پیشرو بودهاند. درصد زیادی از انبارها هنوز در چارچوب WM 3.0 فعالیت میکنند و به آرامی در دهه آینده به سمت WM 4.0 تغییر ریل خواهند داد.

اجزای مدیریت انبار
در ظاهر، فرایند مدیریت انبار میتواند ساده به نظر برسد؛ با دریافت یک محصول در انبار شروع میشود و با ارسال آن به مصرفکننده نهایی به پایان میرسد. با این حال، هنگامی که تمام لایهها را کنار بزنید، بخشهای پوایی زیادی وجود دارد که به صورت هماهنگ کار میکنند.
مهمترین اجزای مدیریت انبار را میتوان به صورت زیر دستهبندی کرد:

۱. عملیات انبارداری
۱.۱ فرایند کلی عملیات انبار
عملیات انبار شامل مجموعه گستردهای از وظایف و فعالیتهایی است که به عملکرد روزمره انبار مربوط میشود. این فعالیتها را میتوان بهطور کلی در سه دسته اصلی تقسیمبندی کرد: عملیات ورودی، ذخیرهسازی، و خروجی. پیش از ورود به جزئیات این عملیات، ابتدا فرایند کلی را بررسی میکنیم.
۱.۲ عملیات ورودی
عملیات ورودی بهعنوان نقطه شروع نقش انبار در زنجیره تأمین عمل میکند و بر مجتمعسازی دقیق و روان محصولات تمرکز دارد. این مرحله شامل دریافت کالاها از تأمینکنندگان یا تولیدکنندگان، بازرسی کیفیت و دقت کالاها، و قرار دادن استراتژیک آنها در مکانهای ذخیرهسازی تعیینشده از طریق فرایندی به نام «انتقال» (Putaway) است.
عملیات ورودی مؤثر پایهای مستحکم برای سطوح دقیق موجودی و پیکربندی بهینه فضای ذخیرهسازی ایجاد میکند. این موضوع برای اجرای عملیات انبار کارآمد و بدون خطا، که به تقاضای مشتریان بهسرعت و با اطمینان پاسخ میدهد، ضروری است.
۱.۳ عملیات ذخیرهسازی
عملیات ذخیرهسازی در انبار بهگونهای طراحی شده است که سطوح بهینه موجودی را حفظ کند و توازنی میان استفاده از فضا و دسترسی سریع و دقیق به کالاها برقرار سازد.
فعالیتهای کلیدی این عملیات شامل موارد زیر است:
- شمارش دورهای منظم برای تأیید دقت موجودی،
- انتقالهای استراتژیک کالاها برای بهینهسازی فضای انبار و مسیرهای برداشت،
- مدیریت جامع موجودی برای ایجاد تعادل میان دسترسی کالاها و هزینههای نگهداری آنها.
عملیات ذخیرهسازی بخش مهمی از کارایی انبار است و اطمینان میدهد که کالاها بهراحتی در دسترس بوده و آماده تحویل هستند، در نتیجه از مشکلاتی نظیر کمبود یا انباشت بیش از حد موجودی جلوگیری میشود.
۱.۴ عملیات خروجی
عملیات خروجی در انبار حول محور تحویل دقیق و بهموقع کالاها به مشتری نهایی یا مرحله بعدی زنجیره تأمین میچرخد. در ترکیب با فرایندهای ورودی و ذخیرهسازی، عملیات خروجی تأثیر مستقیمی بر رضایت مشتری دارد.
فعالیتهای اصلی شامل موارد زیر است:
- برداشت کالاها بر اساس سفارشهای مشتری،
- بستهبندی امن و کارآمد کالاها،
- مرتبسازی کالاها بر اساس مقصد نهایی آنها،
- و در نهایت ارسال کالاها از انبار.
عملیات خروجی بسیار مهم است، زیرا نتایج ملموسی را به مشتری نهایی ارائه میدهد؛ از جمله تحویل دقیق، بهموقع و بدون آسیب. موفقیت کل زنجیره عملیات انبار به اثربخشی فرایندهای خروجی وابسته است.
۲. اصول چیدمان و طراحی
چیدمان و طراحی یک انبار برای به حداکثر رساندن کارایی آن اساسی است. یک انبار با طراحی خوب میتواند با کاهش زمان جابجایی بین عملیات مختلف، بهبود جریان کالاها و استفاده بهینه از فضای موجود، بهرهوری را بهبود بخشد.
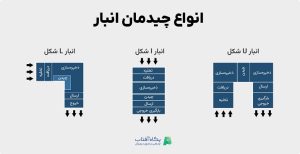
۲.۱ به حداکثر رساندن بازده ذخیرهسازی
وظیفه اصلی یک انبار، ذخیرهسازی است. طرحبندی باید از فضای عمودی و افقی به طور مؤثر برای به حداکثر رساندن ظرفیت ذخیرهسازی بدون مانع شدن حرکت استفاده کند. طبق یک نظرسنجی توسط Modern Materials Handling، در سال ۲۰۲۲ میانگین استفاده از فضای انبار ۸۵.۶ درصد بوده است.
در حالی که فضای موجود در یک انبار همیشه ثابت خواهد بود، هدف به حداکثر رساندن سود اقتصادی از آن فضا است. میتوان از سیستمهای قفسهبندی قابل تنظیم، قفسهبندی چند طبقه و قفسهبندی ماژولار استفاده کرد. همچنین مهم است که نوع کالاهای ذخیره شده، اندازهها، وزنها و دفعات دسترسی به آنها در نظر گرفته شود.
۲.۲ تسهیل جریان روان کالاها:
یک جریان منطقی، زمانهای جابجایی را کاهش میدهد، گلوگاههای احتمالی را به حداقل میرساند و فرایندهای دریافت، ذخیرهسازی، گزینش و ارسال را سرعت میبخشد. مناطق دریافت و ارسال را نزدیک به یکدیگر اما بدون تداخل قرار دهید. راهروها و مسیرها را به گونهای سازماندهی کنید که امکان حرکت شهودی فراهم شود و یک جریان U شکل برای کالاها در نظر بگیرید.
۲.۳ طراحی انعطافپذیر:
انبارها باید با نیازهای تجاری در حال تغییر، نوسانات تقاضای فصلی و پروفایلهای موجودی در حال تکامل سازگار باشند. قفسهبندی و قفسهبندی ماژولار که به راحتی قابل تنظیم مجدد هستند، راهکارهای ذخیرهسازی مقیاسپذیر و مناطقی که میتوانند بر اساس تقاضا تغییر کاربری دهند، در نظر گرفته شوند.
۲.۴ ملاحظات ایمنی:
ایمنی در عملیات انبار بسیار مهم است. یک چیدمان با طراحی خوب، خطر حوادث را به حداقل میرساند، از کارکنان محافظت میکند و از انطباق با مقررات اطمینان حاصل میکند. طبق گزارش اداره آمار کار ایالات متحده، کارفرمایان بخش خصوصی ۲.۶ میلیون مورد آسیب و بیماری غیرکشنده در محل کار در سال ۲۰۲۱ گزارش کردند. از این تعداد، صنایع حمل و نقل و انبارداری ۲۵۳۱۰۰ مورد آسیب غیر مرگبار در محل کار را گزارش کردند.
اجرای راهروهای عریض برای جلوگیری از ازدحام، تابلوهای مناسب، مناطق تعیین شده برای شارژ یا نگهداری تجهیزات و مسیرهای تخلیه واضح و روشن را در نظر بگیرید.
۲.۵ یکپارچهسازی با فناوری:
انبارهای مدرن به طور فزایندهای به فناوری، از سیستمهای مدیریت انبار (WMS) گرفته تا رباتیک، متکی هستند. چیدمان و طرحبندی باید یکپارچهسازی با این فناوریها و عملکرد روان آنها را تسهیل کند. اطمینان حاصل کنید که طراحی امکان حرکت رباتها یا وسایل نقلیه خودکار هدایت شونده (AGV) را فراهم میکند. فضاهایی برای ایستگاههای شارژ در نظر بگیرید و اطمینان حاصل کنید که پوشش وایفای در سراسر انبار برای ردیابی موجودی به صورت آنی وجود داشته باشد.
۳. تکنیکهای کنترل موجودی
مدیریت بهینه موجودی برای موفقیت هر انبار حیاتی است. این شامل اطمینان از سرعت موجودی (سرعتی که اقلام در انبار حرکت میکنند)، تجدید منظم موجودی و حفظ یک رکورد و تاریخچهٔ دقیق از سطوح موجودی است. تکنیکهای مختلفی برای کمک به دستیابی به این هدف وجود دارد، مانند آنالیز ABC، تولید به هنگام یا همان Just-in-Time (JIT) و مقدار سفارش اقتصادی یا Economic Order Quantity (EOQ) میتوانند برای تکمیل فرایندهای مدیریت موجودی استفاده شوند.
چند عامل حیاتی که بر مدیریت موجودی تأثیر میگذارند عبارتند از:
۳.۱ ذخیرهسازی و ردیابی موجودی:
ذخیرهسازی مناسب موجودی تضمین میکند که محصولات در دسترس هستند، زمان بازیابی را کاهش میدهد و کارایی عملیاتی را افزایش میدهد. از سوی دیگر، ردیابی کارآمد، بهروزرسانیهای بیدرنگ در مورد سطوح موجودی را تضمین میکند، پیشبینیهای دقیق تجدید موجودی را امکانپذیر میکند و احتمال کمبود موجودی یا موجودی بیش از حد را کاهش میدهد. ذخیرهسازی و ردیابی مؤثر منجر به سطوح موجودی بهینه، انجام سریعتر سفارش و کاهش ضایعات ناشی از موجودی منقضی شده یا منسوخ میشود.
۳.۲ نظارت بر موجودی:
نظارت بر موجودی شامل نظارت بر سطوح موجودی فعلی و درک الگوهای حرکت موجودی است. درک واضح از اینکه کدام محصولات به سرعت حرکت میکنند (و کدام حرکت نمیکنند) به مدیران انبار اجازه میدهد تا استراتژیهای ذخیرهسازی را تنظیم کنند و اطمینان حاصل کنند که اقلام با گردش مالی بالا در دسترستر هستند. نظارت مناسب بر موجودی منجر به کاهش هزینههای نگهداری و کاهش احتمال موجودی بلااستفاده میشود.
۳.۳ ایجاد و اعتبارسنجی سفارشات خرید:
سفارشات خرید (PO) تعیین میکنند که چه موجودی وارد انبار میشود. ایجاد POهای دقیق تضمین میکند که فقط موجودی لازم سفارش داده میشود. اعتبارسنجی این سفارشات تضمین میکند که مغایرت بین کالاهای سفارش داده شده و دریافت شده به حداقل میرسد و سطوح موجودی دقیق نگه داشته میشود.
۳.۴ دریافت و قرار دادن:
فرایند دریافت تعیین میکند که چگونه موجودی جدید در موجودی موجود ادغام میشود. قرار دادن کارآمد تضمین میکند که اقلام در مکآنهای مناسب ذخیره میشوند و بازیابیهای بعدی را سریعتر و دقیقتر میکند. یک فرایند انبارداری منظم و بدون خطا در دریافت و قرار دادن، تضمین میکند که سطوح موجودی در سیستم مدیریت با موجودی فیزیکی در انبار مطابقت دارد.
مدیریت موجودی مانند یک رقص هماهنگ است، جایی که هر عامل نقشی در تضمین جریان بیوقفه حرکت ایفا میکند. از دانستن محل نگهداری اقلام، تا اطمینان از موجود بودن اقلام مناسب، تا سفارش و دریافت کارآمد موجودی جدید – هر مرحله بر کارایی کلی، دقت و سودآوری سیستم کلی مدیریت انبار تأثیر میگذارد.
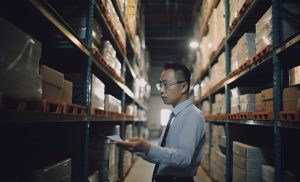
۴. مدیریت نیروی کار
نیروی کار اغلب بزرگترین هزینه در یک انبار محسوب میشود و بهرهوری آن بهطور مستقیم بر سود نهایی تأثیر میگذارد. این امر شامل اطمینان از کافی بودن تعداد کارکنان برای انجام کارها، آموزش مناسب، حفظ بهرهوری، و جبران منصفانه زحمات آنها میشود.
۴.۱ هماهنگی نیروی کار با تقاضا
نیازهای نیروی کار ممکن است بر اساس تقاضاهای فصلی، فعالیتهای کمپینی و سایر متغیرهای بازار متغیر باشد. برنامهریزی صحیح تضمین میکند که در هر زمان کمبود یا مازاد نیروی کار وجود نداشته باشد. با تطبیق اندازه نیروی کار با تقاضای عملیاتی، هزینهها بهینه میشوند، اضافهکاری کاهش مییابد و خستگی کارکنان به حداقل میرسد، که در نهایت منجر به افزایش بهرهوری کلی میشود.
۴.۲ توسعه مهارتها و آموزش
با پیشرفت فناوریها و فرایندهای انبار، کارکنان باید مهارتهای خود را بهروزرسانی کنند تا کارآمد و مرتبط باقی بمانند. کارکنان آموزشدیده خطاهای کمتری مرتکب میشوند، بهرهوری بیشتری دارند و قادرند طیف وسیعتری از وظایف را انجام دهند.
۴.۳ تخصیص مؤثر وظایف
همه وظایف انبار یکسان نیستند؛ برخی به مهارتها یا تخصص خاصی نیاز دارند، در حالی که برخی دیگر عمومیتر هستند. بهعنوان مثال، کار با لیفتراک ممکن است به آموزش و تخصص بیشتری نسبت به استفاده مؤثر از اسکنرهای بارکد نیاز داشته باشد.
تطبیق صحیح وظایف با کارکنان بر اساس مهارتها و نقاط قوت آنها بهرهوری را بهینه میکند. همچنین تخصیص هوشمندانه و پیوسته وظایف باید سطح بهرهوری فردی کارکنان را در نظر بگیرد تا عملکرد یکنواختی حفظ شود.
۴.۴ ایمنی و رفاه
یک انبار ایمن نه تنها یک الزام قانونی است، بلکه به افزایش بهرهوری نیز کمک میکند. کاهش تعداد حوادث به معنای کاهش زمان از دست رفته، هزینههای کمتر غرامت و افزایش روحیه کارکنان است. توجه به رفاه کارکنان همچنین میتواند نرخ ترک کار را کاهش داده و هزینههای مربوط به استخدام و آموزش را کم کند.
۴.۵ تعامل در انبارداری
فناوریهایی مانند سیستمهای مدیریت انبار (WMS) ، ابزارهای پوشیدنی، و نرمافزارهای مدیریت نیروی کار میتوانند فعالیتهای انبار را سادهتر کرده و به تخصیص وظایف کمک کنند. این فناوریها همچنین میتوانند عملکرد کارکنان را پایش کرده، گلوگاهها را شناسایی کرده و منابع را در زمان واقعی باز تخصیص دهند.
بااینحال، باید تعامل بینقصی بین فناوریهای انبار و کارکنان وجود داشته باشد تا اثربخشی آنها در اکوسیستم انبارداری به حداکثر برسد.
۵. ایمنی و انطباق
ایمنی یک نگرانی حیاتی در انبارها است که اغلب شامل کالاهای سنگین و ماشینآلات میشود. انبارها باید با در نظر گرفتن ایمنی طراحی شوند و تجهیزاتی مانند لیفتراک و نوار نقاله باید به درستی نگهداری و به طور صحیح استفاده شوند.
۵.۱ پیشگیری از حوادث و آسیبها
انبارها میتوانند محیطهای پرخطری باشند، با ماشینآلات سنگین، سکوهای مرتفع و حرکت مداوم کالاها. پرداختن پیشکنشی به مسائل ایمنی و ارائه آموزش کارگری، دفعات حوادث را کاهش میدهد و منجر به حوادث کمتر در محل کار و حداقل اختلال در عملیات میشود و در نتیجه باعث افزایش روحیه در بین کارکنان انبار میشود.
۵.۲ افزایش بهرهوری
یک محیط انبار ایمن تضمین میکند که کارکنان میتوانند بدون ترس از آسیبدیدگی کار کنند. هنگامی که آنها اطمینان داشته باشند که ایمنی آنها یک اولویت است، روحیه و بهرهوری بهبود مییابد. طبق یک نظرسنجی توسط موسسه YouGov، ۴۷ درصد از پاسخدهندگان که در صنایع تولید، انبارداری، ساخت و ساز و حمل و نقل کار میکنند، در شغل فعلی خود احساس استرس میکنند.
۵.۳ انطباق با مقررات و جلوگیری از جریمهها
انطباق با مقررات نیز بسیار مهم است و کسبوکارها باید به مقررات مربوط به جنبههایی مانند ایمنی آتشسوزی، مواد خطرناک و حفاظت از کارگران پایبند باشند. انطباق از جریمههای پرهزینه، پیامدهای قانونی و تعطیلیهای احتمالی جلوگیری میکند. علاوه بر این، یک مرکز سازگار با مقررات اغلب میتواند در شرایط بهتری را با بیمهها مذاکره کند و منجر به کاهش حق بیمه شود.
فعالیتهای مختلف در مدیریت انبار
در حالی که فعالیتهای زیادی بهطور همزمان در یک انبار انجام میشود، میتوان آنها را در چهار دسته اصلی گروهبندی کرد:
۱. عملیات ورودی
۱.۱ دریافت کالا
مرحله ابتدایی است که در آن کالاها از تأمینکنندگان یا تولیدکنندگان دریافت میشوند. این مرحله شامل بررسی تعداد صحیح کالاها و اطمینان از آسیبندیدگی آنها است.
۱.۲ کنترل کیفیت (QC)
پس از دریافت، اقلام اغلب از فرایند QC عبور میکنند تا اطمینان حاصل شود که استانداردهای موردنیاز را برآورده میکنند.
۱.۳ مدیریت محوطه
این مرحله شامل هماهنگی و مدیریت جریان وسایل نقلیه در محوطه اطراف انبار است. این فرایند برای برنامهریزی کارآمد دربهای بارگیری و کاهش زمان انتظار کامیونها ضروری است.
۱.۴ انتقال
پس از اتمام کنترل کیفیت، اقلام به مناطق ذخیرهسازی تعیینشده در انبار منتقل میشوند.
عملیات ورودی کارآمد اطمینان میدهد که کالاها بهسرعت و بهدرستی در سیستم مدیریت انبار یکپارچه میشوند. اشتباهات یا تأخیر در این مرحله میتواند تأثیرات منفی بر کل عملیات انبار داشته باشد، از جمله کاهش دقت موجودی و زمآنهای طولانیتر انجام سفارشها.
۲. عملیات ذخیرهسازی
۲.۱ تخصیص مکان:
اقلام بر اساس عواملی مانند فراوانی تقاضا، اندازه، یا فسادپذیری به مکانهای خاصی اختصاص داده میشوند.
۲.۲ مدیریت موجودی:
شامل ردیابی منظم سطح موجودی برای حفظ سطوح بهینه است.
۲.۳ شمارش دورهای:
انجام ممیزیهای منظم برای تأیید دقت موجودی.
۲.۴ انتقال موجودی:
انتقال محصولات در داخل یا بین انبارها برای بهینهسازی فضا و اطمینان از فرایندهای کارآمد برداشت سفارشها.
عملیات ذخیرهسازی مؤثر استفاده از فضا را به حداکثر میرساند، زمان برداشت را به حداقل میرساند و دقت موجودی را حفظ میکند. این عوامل مستقیماً بر سرعت پردازش سفارشها و کارایی کلی انبار تأثیر میگذارند.
۳. عملیات خروجی
۳.۱ برداشت سفارش:
برداشتن اقلام از مناطق ذخیرهسازی برای تکمیل سفارشهای مشتری.
۳.۲ بستهبندی:
بستهبندی ایمن اقلام برای حملونقل بهمنظور اطمینان از تحویل بدون آسیب.
۳.۳ مرتبسازی:
سازماندهی بستهها بر اساس مسیرهای تحویل یا روشهای حملونقل.
۳.۴ حملونقل:
تکمیل سفارشها برای تحویل، که ممکن است شامل بارگیری روی کامیونها، چاپ برچسبهای حملونقل، یا تحویل آنها به شرکتهای حملونقل ثالث باشد.
عملیات خروجی آخرین مرحله در ارائه ارزش به مشتری است. سرعت و دقت در این فرایند انبار زمانهای انجام سفارش را تعیین کرده و به طور مستقیم بر رضایت مشتری تأثیر میگذارد. عملیات خروجی کارآمد همچنین میتواند هزینههای حملونقل را کاهش دهد.
۴. لجستیک معکوس
۴.۱ پردازش بازگشتها:
دریافت کالاهای بازگشتی از مشتریان که ممکن است به دلایل نقص، اشتباه در سفارش، یا سایر مسائل باشد.
۴.۲ دریافت و کنترل کیفیت:
اقلام بازگشتی برای تعیین وضعیت آنها تحت بررسی کیفیت قرار میگیرند.
۴.۳ بازگشت به موجودی یا تعویض:
بر اساس گزارش کنترل کیفیت، اقلام ممکن است دوباره ذخیره شوند، تعویض شوند، یا در صورت آسیبدیدگی غیرقابلجبران، دور ریخته شوند.
مدیریت بازگشت کارآمد میتواند ارزش کالاهای بازگشتی را بازیابی کرده و بینشهایی در مورد مشکلات مکرر ارائه دهد. این فرایند همچنین نقش مهمی در حفظ اعتماد و رضایت مشتری دارد.
اصول مدیریت حرفه ای انبار
سؤال مهم اینجاست: چه عواملی برای مدیریت کارآمد و حرفهای عملیات انبار در مقیاس بزرگ لازم است؟ برای اینکه مدیریت کارآمد مؤثر باشد، هر راهحل یا سیستم مدیریت انبار باید توانایی پشتیبانی از اجزا و فعالیتهای مختلفی که تا اینجا مطرح شد را داشته باشد.
۱. بهینهسازی فرایندها
یکی از قابلیتهای اصلی هر راهحل مدیریت انبار، سادهسازی فرایندهای ورودی و خروجی است؛ از دریافت و ذخیره کالاها گرفته تا برداشت سفارش، بستهبندی و ارسال.
چرا مهم است؟
بهینهسازی فرایندها برای بهرهوری حداکثری از نیروی کار، منابع و زمان حیاتی است. این کارایی بالا در دنیای پرسرعت تجارت امروزی که عملیات دقیق، سریع و بدون خطا ضروری است، اهمیت ویژهای دارد.
۲. تحلیل عملکرد در لحظه
قابلیت ردیابی و اندازهگیری عملکرد در لحظه به مدیران انبار این امکان را میدهد که تصمیمات آگاهآنهای بگیرند. شاخصها میتوانند در سطوح مختلف، از کل انبار تا محصولات یا عملکرد فردی کارکنان، مشاهده شوند.
چرا مهم است؟
دستیابی به آگاهیها عمیق در سطوح انبار، ایستگاهها، کارکنان، کانالهای فروش و محصولات، مشکلات و گلوگاهها را بهسرعت شناسایی کرده و به مدیران اجازه میدهد تا بهصورت پیشگیرانه مشکلات را مدیریت کنند.
۳. بهرهوری نیروی کار
نیروی انسانی قلب عملیات انبار است. تضمین کارایی و اثربخشی کارکنان و شناسایی نقاط قابل بهبود ضروری است.
شاخصها و معیارهای کلیدی بهرهوری نیروی کار:
- نرخ برداشت: تعداد اقلام برداشتشده در هر ساعت
- زمان توقف: مدتزمان از دریافت سفارش تا ارسال
- نرخ بهرهوری: درصد زمانی که یک کارمند واقعاً مشغول کار است
چرا مهم است؟
بهرهوری نیروی انسانی تأثیر مستقیم بر توان عملیاتی، هزینهها و سودآوری انبار دارد.
۴. اتوماسیون نرمافزاری و رباتیک
اتوماسیون در بیشتر صنایع انقلابی ایجاد کرده و در مدیریت انبار اهمیت بیشتری یافته است. فرایندهای مدیریت انبار که به طور سنتی نیروی کار زیادی نیاز داشتند، اکنون به کمک اتوماسیون در مقیاس وسیع بهینهسازی میشوند.
چرا مهم است؟
- با خودکارسازی وظایفی مانند ورود دادهها و ردیابی موجودی، دقت دادهها افزایش یافته، پردازش سریعتر انجام میشود و خطاهای انسانی کاهش مییابد.
- راهحلهای رباتیک مانند سیستمهای ذخیرهسازی و بازیابی خودکار(ASRS) ، رباتهای برداشت، رباتهای متحرک خودکار (AMR) و نوار نقالهها پرسرعت، دقت و ایمنی را بهبود میبخشند. این سیستمها مکمل نیروی انسانی هستند و با ایجاد همافزایی، بهرهوری بیشتری ایجاد میکنند.
۵. استفاده بهینه از فضا
فضای انبار گرانقیمت است و به حداکثر رساندن استفاده از آن برای سودآوری ضروری است.
چرا مهم است؟
یک راهحل هوشمند مدیریت انبار میتواند راهحلهای ذخیرهسازی بهینه را با در نظر گرفتن عواملی مانند تقاضای محصول، اندازه و فسادپذیری مشخص کند. همچنین میتواند طرح و طراحی انبار را تحلیل کرده و مسیرهای برداشت و توصیههای ذخیرهسازی هوشمند را برای حداکثر سرعت و کارایی ارائه دهد.
۶. کاهش هزینهها و سربارها
با توجه به رقابت شدید و حاشیه سود کم در لجستیک، کارایی هزینهها اهمیت ویژهای دارد.
چرا مهم است؟
به لطف بهرهوری نیروی کار، اتوماسیون و استفاده بهینه از فضا، یک سیستم مدیریت انبار مدرن بهطور مستقیم باعث کاهش چشمگیر هزینههای عملیاتی میشود.
۷. تواناییهای اکوسیستم
انبارها بهصورت مستقل عمل نمیکنند. آنها بخشی از یک اکوسیستم بزرگتر زنجیره تأمین هستند. یک راهحل مدیریت انبار میتواند با نرمافزارهای ERP، TMS یا BI یکپارچه شود تا بینشی درباره وضعیت فرایندهای مدیریت انبار ارائه دهد. این شامل موارد زیر میشود:
- پیشبینی سطح موجودی
- پیشبینی تقاضا
- راهنمایی درباره شیوههای ذخیرهسازی
- پشتیبانی از برداشت و بستهبندی
چرا مهم است؟
یک سیستم مدیریت انبار موفق باید بهطور یکپارچه با دیگر سیستمهای زنجیره تأمین و تجارت هماهنگ شود. همگامسازی لحظهای موجودی، سفارشات، نیروی کار، صورتحسابها و اسناد حملونقل باعث میشود کل اکوسیستم در هماهنگی کامل عمل کرده و خطاها، تأخیرها و هزینهها کاهش یابند.
وظایف یک سیستم مدیریت انبار
- کنترل موجودی: نظارت و مدیریت سطوح موجودی، مکانها و گردش موجودی.
- انجام سفارش: رسیدگی به کل فرایند سفارش تا حمل، از جمله برداشت، بستهبندی و ارسال.
- دریافت و قرار دادن: مدیریت ورود کالاها، بازرسی آنها و قرار دادن آنها در مکانهای ذخیرهسازی مناسب.
- مدیریت نیروی کار: تخصیص و بهینهسازی منابع انسانی برای وظایف مختلف انبار و پایش بهرهوری آنها.
- استفاده از فضا: بهینهسازی فضای ذخیرهسازی برای قرار دادن و بازیابی کارآمد محصول.
- مدیریت محوطه: هماهنگی حرکت و ذخیرهسازی وسایل نقلیه و حملکنندهها در محوطه انبار.
- گزارشدهی و تجزیه و تحلیل: ارائه بینش و اطلاعات مفید در مورد عملیات انبار، شاخصهای کلیدی عملکرد (KPIها) و روندها.
- قابلیتهای یکپارچهسازی: یکپارچهسازی با سایر سیستمها مانند ERP، TMS و پلتفرمهای تجارت الکترونیک برای رسیدن به چشماندازی گسترده و پیوسته در انجام سفارش.
- ایمنی و انطباق: اطمینان از رعایت تمام عملیات با مقررات صنعت و استانداردهای ایمنی.
- لجستیک معکوس: مدیریت فرایند برگشت، تعمیر، بازیافت و دفع.