سه اشتباه در روانکاری بلبرینگها
اصطکاک در همهجا وجود دارد. بدون آن، دویدن، راه رفتن و حتی ایستادن روی دو پای خود امری بسیار دشوار خواهد بود. ما برای رانندگی با ماشین و پرواز با هواپیما به اصطکاک نیاز داریم؛ و برای اینکه موتورهایمان پمپها را به پمپاژ وا دارند هم به اصطکاک نیاز داریم. اما وقتی صحبت از ماشینآلات و تجهیزات کارخانه میشود، اصطکاک تومامان هم دوست است و هم دشمن.
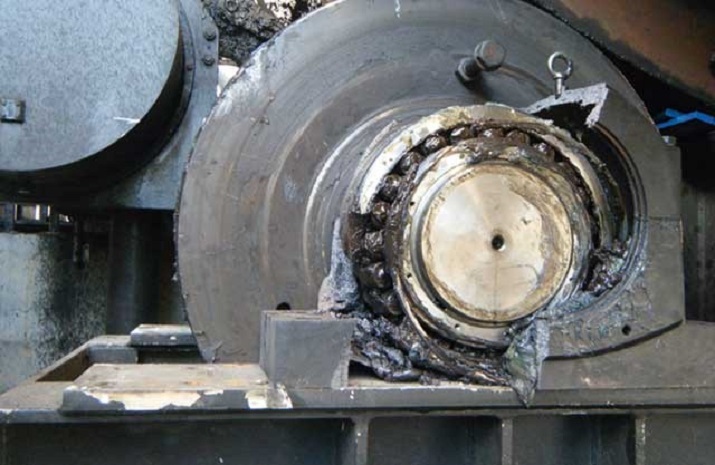
بیشتر بخوانید: ۱۰ دلیل خرابی بلبرینگها (یاتاقانها)، حالات خرابی آنها و روشهای پیشگیری
اگر بخشی از کار شما روغنکاری یا روانکاری ماشینآلات و تجهیزات کارخانه باشد، به خوبی از مبارزه با نیروهای اصطکاکی که عمر مفید بلبرینگهای غلتشی را تهدید میکنند، آگاه هستید. روانکاری بلبرینگهای غلتشی یکی از کارهای پر ابهام و پر از سوءتفاهم در صنعت است. آیا این موضوع حقیقت دارد که که ۴۰ درصد از بلبرینگها هرگز به چرخه عمر مهندسی خود نمیرسند و شیوههای نادرست روانکاری علت اصلی این جوانمرگی آنها است؟
بلبرینگها برای کاهش سطح اصطکاک به گریس وابسته هستند. با اجتناب از سه اشتباه رایج هنگام روانکاری بلبرینگها، میتوانید زمان مناسب برای روغن کاری را پیشبینی کنید، میزان گریس مورد نیاز را بدانید و از سلامت کلی بلبرینگ اطمینان حاصل کنید.
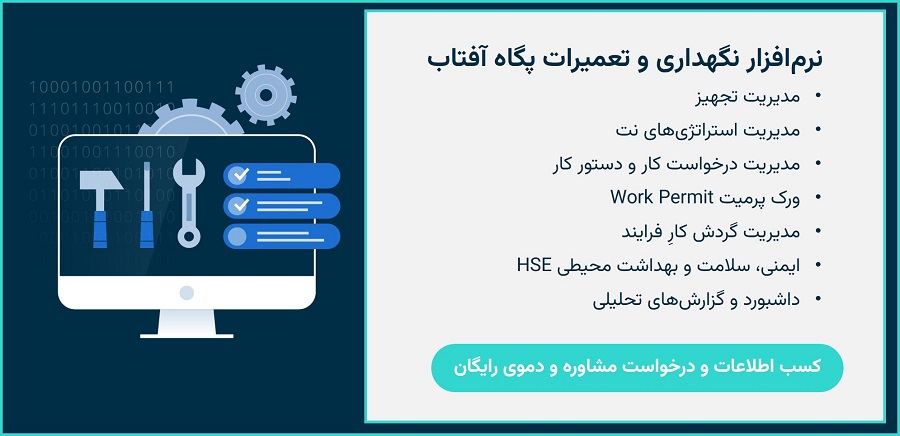
اشتباه ۱: روانکاری بر مبنای دورههای زمانی به جای شرایط و وضعیت بلبرینگ
روانکاری یک بلبرینگ یک بار در هفته یا یک بار در ماه ممکن است کار معقولی به نظر برسد. همچنین قرار گرفتن چنین وظایفی مبتنی بر دورههای زمانی یکی از پدیدهها و مفاهیم عمیقی و ریشهدوانده در نگهداری و تعمیرات بابرنامه است.
بلبرینگها فقط به یک دلیل به گریس نیاز دارند، و آن هم کاهش اصطکاک است. تا زمانی که روانکننده به خوبی این وظیفهٔ حیاتی خود را انجام میدهد، نیازی به تعویض یا اضافه کردن آن نیست. با این حال، اغلب این کار توسط تیمهای برنامهریز و یا کارکنان نگهداری و تعمیرات انجام میشود که نتایج فاجع آمیزی به دنبال دارد.
اولین اشتباه این است که بر اساس تقویم و یک زمانبندی از پیشمشخصشده اقدام به روانکاری بلبرینگها کنیم. چرا؟ چون تقویم گفته است.
اقدام درست اما این است که با استفاده از تکنیکهای پایش اولتراسونیک زمان مناسب برای گریسکاری را مشخص کنید، سطح اصطکاک را کنترل، اندازهگیری و پایش کنید و روندهای تغییرات آن را مشخص و ثبت کنید.

هنگامی که سطح روانکاری ایدهآل به دست آمد، مقدار دسیبل میکروولتها به سطح طبیعی خود باز میگردد. این در هدفون، در بازتولید سیگنال دینامیک کاملاً قابل شنیدن است و روی صفحه دستگاههای آنالیز اولتراسونیک کمپانی SDT قابل مشاهده است.

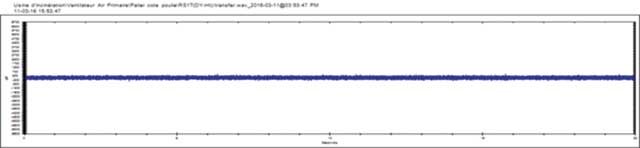
اشتباه ۲: روانکاری بیش از حد یا کمتر از حد نیاز
دومین اشتباهی که باید از آن اجتناب کنیم، اضافه کردن گریس به خیلی کم یا خیلی زیاد است. گریس بیش از حد فشار ایجاد میکند، عناصر غلتشی را از طریق فیلم سیال و به سمت رینگ بیرونی هل میدهد. در این صورت بلبرینگ باید خیلی سختتر کار کند تا عناصر غلتشی را از میان باتلاقی از گریسها عبور دهد.
افزایش اصطکاک و فشار ناشی از گریس بیش از حد، دمای داخل بلبرینگ را بالا میبرد. گرمای بیش از حد میتواند اثربخشی روانکننده را کاهش دهد و باعث جدا شدن روغن از تغلیظ کننده شود. اضافه نکردن گریس کافی نیز همین اثر کوتاه شدن عمر را به دنبال دارد.
اما چگونه میتوان فهمید که مقدار مناسبی گریس به بلبرینگ اضافه شده است؟ با کنترل سطح اصطکاک به وسیلهٔ آنالیز اولتراسونیک در حین روانکاری جدید.
به بلبرینگ گوش دهید و افت اصطکاک را با ورود گریس به بلبرینگ اندازهگیری کنید. با نزدیک شدن سطح دسی بل به حداقل مقدار و تثبیت شدن، به دفت توجه کنید. شاتهای تکخوان (single shots) را اضافه کنید. اگر سطح دسی بل کمی شروع به افزایش کرد، متوقف شوید! کار تمام شده است.
اشتباه ۳: تکیهٔ صرف به ابزارهای شنیداری اولتراسونیک و خلاء آنالیز آنها
مانند هر شغلی، یک راه درست و یک راه غلط برای انجام کارها وجود دارد. گوش دادن تنها به امواج التراسونیک ساطعشده از بلبرینگها با یک دستگاه اولتراسونیک که بازخورد سنجش التراسونیک را ارائه نمیدهند و همه چیز را به گوشهای شما حواله میدهند، دستورالعملی فاجعهآمیز است.
استفادهٔ صرف از بازخورد صوتی برای نتیجهگیری و مقایسهٔ شزایط مطلوب با نامطلوب امری بسیار ذهنی و انتزاعی و پر از خطاهای احتمالی است. هیچ یک از کارکنانی که این وظیفه را بر عهده دارند به طور یکسان نمیشنوند و هیچ راهی برای به خاطر سپردن صدای بلبرینگ در یک ماه گذشته وجود ندارد.
سومین اشتباه اتکای صرف بر صدای اولتراسونیک به صورت ذهنی و انتزاعی است، در حالی که دادههای کمّیِ دقیق در دسترس هستند. بنابراین، همیشه از یک ابزار اولتراسونیک با قابلیت اندازهگیری و نمایش دیجیتال دسی بل استفاده کنید. راهکار بهتر از آن این است که از دستگاهی استفاده کنید که چندین شاخص وضعیت کارکرد بلبرینگ را همزمان به نمایش بگذارد.
اندازه گیریهای حداکثر RMS و پیک دسی بل نشاندهنده سطوح هشدار و فواصل روانکاری هستند، در حالی که ضریب قله اولتراسونیک بینشی در مورد وضعیت بلبرینگ در رابطه با روانکننده آن ارائه میدهد. ضریب قله به ما کمک میکند تا بین بلبرینگهایی که نیاز به گریس دارند و بلبرینگهایی که نیاز به تعویض دارند تمایز قائل شویم.
مزایای آشکار اجتناب از سه اشتباه مهم در روانکاری بلبرینگها
روانکاری تجهیزات کارخانه با کمک فناوری اولتراسونیک، مزایای قابل توجهی را ارائه میدهد که روانکاری بر اساس تقویم و زمان بندی از پیشمشخص نمیتواند ارائه دهد. وظیفه اصلی روانکاری ایجاد یک لایه نازک از روانکننده بین عناصر غلتشی و لغزشی را بر عهده دارد تا اصطکاک را کاهش میدهد. بنابراین منطقی است که بهترین راه برای تعیین نیاز روانکاری یک دستگاه، نظارت بر سطوح اصطکاک است، نه زمان کارکرد.
بهینهسازی روانکاری ماشین آلات و تجهیزات کارخانه با استفاده از فناوری اولتراسونیک منجر به کاهش قابل توجه مصرف گریس میشود. داشتن یک برنامه آنالیز اولتراسونیک به ایجاد فرهنگ بهتر نگهداشتی شامل شیوههای انبارش اصولیتر، نمونهگیری و اجتناب از مخلوط کردن گریسها کمک میکند.
ماشین آلاتی که به درستی روغنکاری شدهاند برای کار به انرژی کمتری نیاز دارند. تصور کنید که کاهش هزینه صرف شده برای گریس در واقع منجر به کاهش قبوض انرژی میشود. ماشینآلات و تجهیزاتی که برق کمتری مصرف میکنند خنکتر کار میکنند و ماشینهایی که خنکتر کار میکنند عمر طولانیتری دارند.
دلیل اصلی بهینهسازی روانکاری بلبرینگها، افزایش طول عمر بلبرینگها با اطمینان از داشتن مقدار مناسب گریس در آنها است، حد متعادلی که نه بیش از حد باشد و نه کمتر از حد مورد نیاز. هنگامی که همه چیز طبق برنامه پیش میرود، تکنسینهایی که وظیفهٔ روانکاری را برعهده دارند، زمان کمتری را صرف روغنکاری بلبرینگها میکنند و دیگر به اشتباه سراغ تجهیزاتی که فعلا نیاز به این کار ندارند نمیروند. بنابراین، هنگام محاسبه مزایای دخیل کردن یک برنامه سنجش و آنالیز اولتراسونیک برای روانکاری، فراموش نکنید که «کاهش نیاز به نیروی کار» را نیز به لیست بلند خود اضافه کنید.
در نهایت، با نظارت بر وضعیت روانکاری ماشین آلات خود، همزمان دادههای ارزشمندی در مورد وضعیت تجهیز جمعآوری میکنید. دادههای اولتراسونیکِ دینامیک و استاتیک همراه با شاخصهای وضعیت مانند Overall RMS، Max RMS، Peak و Crest Factor همگی نشانگر سلامت بلبرینگها هستند.
0 پاسخ
ممنونم از ارائه این توضیحات که واقعا درست وبجا می باشد .