پایش وضعیت چیست؟
پایش وضعیت به اندازه گیری پارامترهای خاصی از تجهیزات، مانند سنجش ارتعاشات در یک ماشین یا تجهیز، دمای تجهیز یا وضعیت روغن آن گفته میشود که با توجه به هر تغییر قابل توجهی که میتواند نشاندهنده خرابی قریب الوقوع تجهیز باشد، تعریف میشود. نظارت مداوم بر وضعیت و شرایط تجهیزات و توجه به هر گونه نقصانی که به شکل معمول میتواند طول عمر یک تجهیز را کوتاه کند، باعث میشود تا نگهداری و تعمیرات یا سایر اقدامات پیشگیرانه (پیشگیری از خرابی تجهیزات) برای رسیدگی به مشکلات مرتبط، قبل از اینکه این نقصانها و مشکلات به خرابیهای جدیتر تبدیل شوند، برنامهریزی شوند.
پایش وضعیت عنصر مهمی در استراتژی نگهداری و تعمیرات پیشبینانه است. دادههای جمعآوریشده از پایش وضعیت در طول زمان اطلاعات ارزشمندی در مورد وضعیت فعلی و تاریخچهای یک تجهیز ارائه میدهد. این سیر اطلاعات در خصوص یک ماشین یا تجهیز را میتوان در پیشبینی نحوه عملکرد تجهیز در طول زمان و سناریوهای ممکن خرابی آن استفاده کرد و امکان برنامهریزی و زمانبندی اقدامات نگهداری و تعمیرات بر اساس این پیشبینیها را فراهم کرد. این مر در دنیای نگهداری و تعمیرات به عنوان نت پیشبینانه (predictive Maintenance) معروف است. به این معنا که نگهداری و تعمیرات بر اساس این که چه خرابیهایی ممکن است در آینده رخ دهد و چه تعمیراتی باید برنامهریزی شود تا از وقوع چنین خرابیهایی جلوگیری شود، طراحی میشود.
از تکنیکهای پایش وضعیت معمولا در تجهیزات دوار (گیربکسها، تجهیزات دوار، تجهیزات گریز از مرکز و غیره)، سیستم های پشتیبان یا ثانویه، و ماشین آلات و تجهیزات دیگری چون کمپرسورها، پمپها، موتورهای الکتریکی، پرسها و موتورهای احتراق داخلی استفاده میشود.
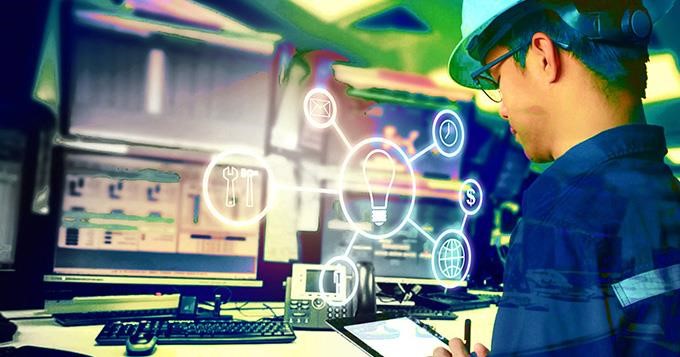
دو روش رایج برای پایش وضعیت وجود دارد که در ادامه به آنها میپردازیم:
۱. پایش روند:
پایش روند وضعیت تجهیز به معنی اندازهگیری و تفسیر مداوم و منظم دادههای مرتبط با وضعیت تجهیز است. این کار شامل انتخاب یک نشانه مناسب و قابل اندازهگیری از خرابی تجهیز یا قطعه و بررسی این روند برای تعیین زمانی است که خرابی از یک حد بحرانی فراتر میرود. به عنوان مثال، در موتور هوایپما معمولاً دادههای موتور هواپیما به صورت روتین مورد پایش قرار میگیرد تا ناهنجاریها و نقصانهای جزئی عملکردی موتور شناسایی شده و با این کار از آسیبهای ثانویه و پرهزینهتر جلوگیری شود.
۲. چک کردن وضعیت تجهیز:
چک کردن وضعیت تجهیز شامل اندازهگیری وضعیت تجهیز در حال کار به وسیلهٔ تعیین یک شاخص مناسب قابلاندازهگیری در طول چکهای دورهای است. اطلاعات حاصل از این روش سپس برای سنجش وضعیت تجهیز در یک زمان مشخص استفاده میشود. یک مثال از چک کردن وضعیت تجهیز میتواند استفاده از یک شیشه رویت روغن (Oil Sight Glass) مانند یک پادِ پایش وضعیت (CMP) برای چک کردن وضعیت روغنکاری تجهیز در لحظه و به صورت آنی باشد.
پایش وضعیت از طریق این دو روش، نگاهی درونی به نحوه عملکرد تجهیزات و اجزای سازنده آنها میاندازد و در طول زمان، گزارشی تاریخچهای از سلامت تجهیزات ارائه میدهد.
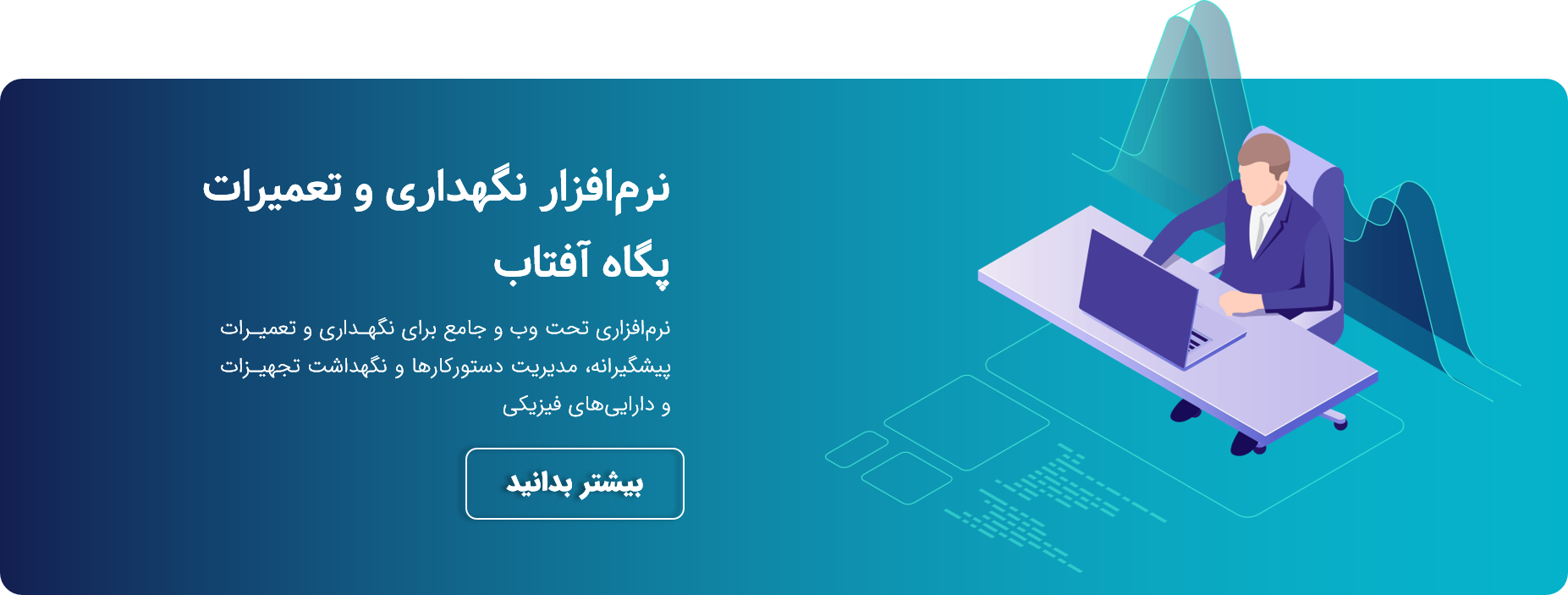
انواع پایش تجهیزات
انواع مختلفی از انواع و تکنیکهای پایش وضعیت تجهیزات وجود دارد که هر کدام نقش متفاوتی را در جمع آوری دادهها بازی میکنند. در ادامه به مهمترین این روشها پرداختهایم:
۱. پایش وضعیت آفلاین
پایش وضعیت آفلاین معمولاً برای داراییها و تجهیزات کمتر بحرانی یا نیمه بحرانی استفاده میشود که در آن اسکن دورهای برای اطلاع از وضعیت فعلی تجهیز کفایت میکند. پایش آفلاین وضعیت تجهیز، معمولاً در آنالیز ارتعاش کاربرد دارد. به خصوص زمانی که چک و بررسیهای دورهای برای تجهیزاتی با درجه بحرانیت کم کفایت میکند. همچنین این نوع پایش وضعیت برای آنالیز روغن زمانی که روغن برای آزمایش به آزمایشگاه فرستاده میشود، استفاده میشود. به همراه آنالیز آفلاین روغن، برخی از سازمانها از کیتهای نمونهبرداری برای آزمایش ویسکوزیته و میزان آب موجود در روغنهای خاص در محل برای نتایج اولیه استفاده میکنند. تجهیزات آزمایش داخلی نیمه خودکار نیز برای آزمایش مواردی مانند سایش فلزات، نیتراسیون، اکسیداسیون و تخلیهٔ مواد افزودنی موجود است.
۲. پایش وضعیت آنلاین
پایش وضعیت آنلاین، به معنی سنجش و اندازهگیری مستمر شاخصهای از وضعیت یک تجهیز مانند آنالیز ارتعاش، تست انتشار امواج صوتی، آنالیز فراصوت و دمانگاری یا ترموگرافی مادون قرمز با اتصال حسگرهای مشخصی روی آن است، به شکلی که دادههای پایششده از این حسگرها بلادرنگ و بیوقفه در سیستمهای یکپارچهٔ نرمافزاری استقراریافته در سازمان به نمایش درآید. پایش وضعیت آنلاین به کمک انواع حسگرها و سیستمهای نظارتی می تواند بسیار قابل سفارشیسازی باشد و تنظیمات متعددی را روی آن اعمال کرد. عواملی مانند نوع ماشین، نوع بلبرینگ، سرعت ماشین، اجزای ماشین و عناصر ماشین باید هنگام انتخاب یک سیستم نظارت آنلاین در نظر گرفته شوند.
اگر حسگرهای مناسب بر روی تجهیز و در نقطه درستی از آن نصب شوند، میتوان این حسگرها را به صورت بیسیم به یک سیستم نرمافزاری پایش وضعیت از راه دور متصل کرد که در آن دادهها را به صورت ریل تایم و آنی به نمایش درآید. اکثر سیستمهای پایش وضعیت میتوانند انواع مختلفی از دادههای استخراجشده از انواع حسگرها (اعم از ارتعاش، ترموگرافی، امواج صوتی و غیره) را ادغام کنند، تا فرد مسئول بر روی یک داشبورد بصری و در لحظه وضعیت فعلی تجهیز مورد نظر خود را دریافت و مشاهده کند. پایش وضعیت آنلاین همچنین به شما این امکان را میدهد تا هشدارهای فوری را برای ارسال بر روی موبایل به صورت نوتفیکیشن و یا در قالب یک ایمیل تنظیم کنید.
۳. پایش وضعیت مبتنی بر مسیر
پایش وضعیت مبتنی بر مسیر تکنیکی است که در آن یک تکنسین دادهها را به طور متناوب با استفاده از یک دستگاه دستی مانند دوربین تصویربرداری مادون قرمز ثبت میکند. اغلب از این روش برای ایجاد یک الگوی روند و تعیین اینکه آیا به تجزیه و تحلیل پیشرفتهتری نیاز است یا خیر، استفاده میشود.
تکنیکهای پایش وضعیت
پایش وضعیت با بازرسیهای پایهای شروع میشود. تغییرات کوچکی مقل افزایش دما یا فشار غیرطبیعی، صداهای غیرمعمول، ارتعاشات بیش از حد، یا ساطع شدن بوهای غیرمعمول، اغلب نشانههایی هستند که حاکی از رخدادی برای تجهیز است. تکنیکهای متعددی برای پایش وضعیت ماشینآلات و تجهیزات وجود دارد که از آنها برای ارزیابی وضعیت تجهیزات استفاده میشوند.
۱. پایش دما
پایش دما از دهههای گذشته به عنوان روشی برای ارزیابی سلامت تجهیز پذیرفته شده است. روشهای مختلفی برای پایش دما وجود دارد، که از پایش منفعل دما (Passive)، پایش بدون تماس (با استفاده از دوربینهای حرارتی) تا اسکن مادون قرمز بر پایهٔ حسگرهای فعال، را شامل میشود. روشهایی که هر کدام در جای خود میتوانند نمای کلی خوبی از وضعیت ماشینآلات و تجهیزات را نشان دهد و مشکل افزایش دما و داغ شدن تجهیز یا قطعه را گزارش دهد. دمانگاری به روش تماسی برای تشخیص زودهنگام مشکلات مربوط به روانکاری بسیار مفید است، اما برای تشخیص آسیبهای فیزیکی مانند ترکخوردگی و خراشیدگی یاتاقانها چندان مفید نیست.
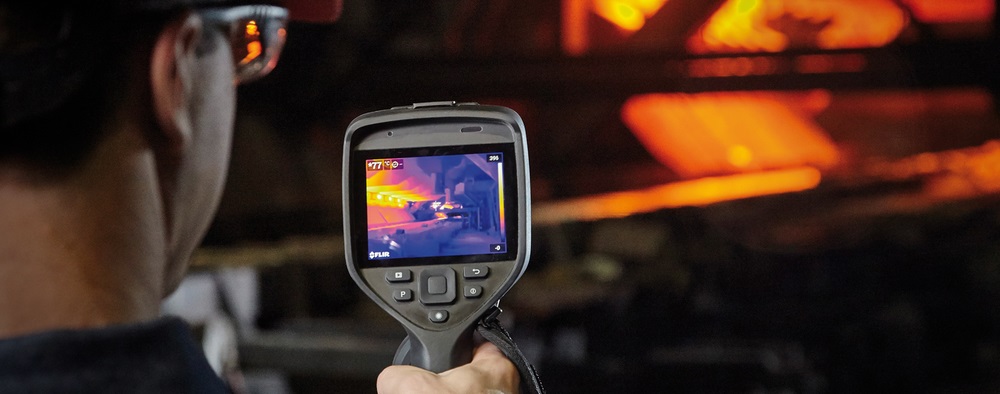
ترموگرافی مادون قرمز اما شیوهای آسان برای استفاده است و درک اطلاعات آن نیز ساده اشت. ترموگرافی مادون قرمز تکنیک نظارتیای است که میتوان آن را مکمل آنالیز ارتعاش برشمرد. و میتوان از آن برای غنیسازی اطلاعات جمعآوری شده و تشخیص بهتر وضعیت قطعات مکانیکی استفاده کرد، و با استفاده از دادههای آن پشتیبان برنامههای پیشگیری از خرابیهای الکتریکی یا خطر وقوع آتش سوزی در محیطهای صنعتی بود.
۲. پایش ارتعاش
پایش ارتعاش و آنالیز ارتعاش، روشی بسیار قدیمی و از رایجترین شیوههای ارزیابی وضعیت تجهیزات است. این روش به ما در تشخیص خرابی و درک علل ریشهای بروز خرابی کمک میکند. شتابسنجها برای پایش و مانیتور کردن تغییرات دامنه در یک محدوده فرکانسی گسترده استفاده میشوند. پایش ارتعاش به شما اجازه میدهد تا پدیدههایی مانند عدم تعادل، شلی و لقی تجهیز یا قطعه، مشکلات چرخدندهها یا سایش را قبل از خرابی قطعه یا تجهیز متوجه شوید و اقدام به اعمال برنامههای اصلاحی کنید.
آنالیز ارتعاش نیز فرایندی برای سنجش میزان ارتعاش و بسامد ارتعاش ماشینآلات و تجهیزات و سپس استفاده از این اطلاعات برای تجزیه و تحلیل سلامت تجهیز است. آنالیز ارتعاش میتواند موضوعاتی مانند عدم تعادل، خرابی یاتاقان، شلی مکانیکی، ناترازی، فرکانسهای تشدیدی و طبیعی، خطاهای موتور الکتریکی، خمیدگی شفتها و حتی کاویتاسیون (cavitation) یا حفرهزایی را تشخیص دهد.. به صورت تخمینی و تجربی گفته میشود که معمولاً بین هشدارهای مبتنی بر پایش و آنالیز ارتعاش تا وقوع یک خرابی جدی و واقعی سه ماه فاصله است.
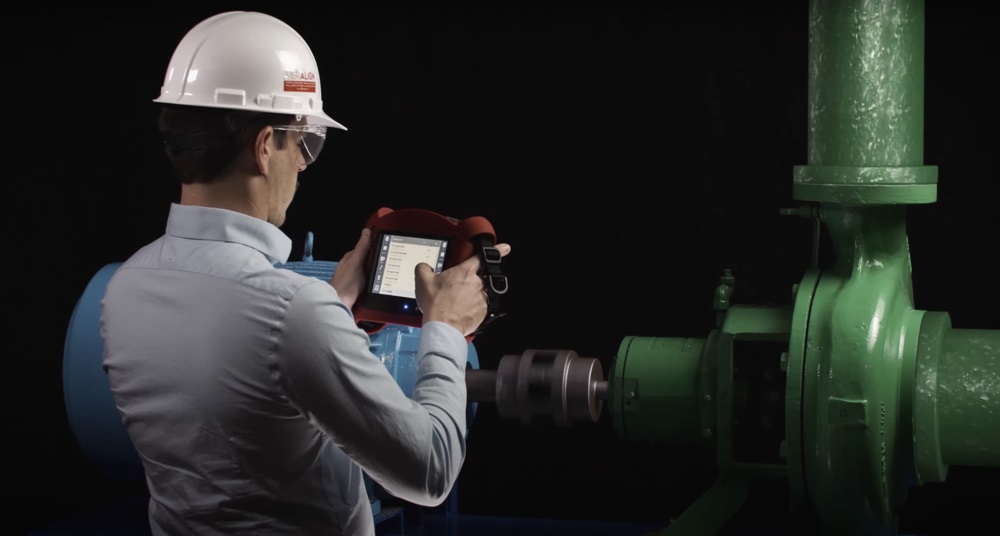
۳. انتشار امواج صوتی (Acoustic Emission)
در سالهای اخیر استفاده از حسگرهای انتشار امواج صوتی برای پایش وضعیت تجهیز، به دلیل مزایای زیادی که برای تشخیص زودهنگام خطاها و نقصانهای تجهیزات و قطعات دارند، بیشتر و بیشتر شده است. اما به دلیل مشکل ذخیرهسازی دادههای حجیم به دلیل عملکرد در فرکانس بالا (چند کیلوهرتز تا مگاهرتز) و قیمتهای بالا این حسگرها در مقایسه با سایر راهکارهای موجود در بازار، روش مناسبی برای پایش دائمی نیست.
۴. تست فراصوت (Ultrasound Testing)
آزمون فراصوت، یک فناوری بسیار مقرون به صرفه است که به ویژه برای پاسخ به این سوال پایهای، که آیا دستگاه سالم است یا خیر، استفاده میگردد. آشکارسازها و حسگرهای فراصوت به طور معمول امواج فشار صوتی را در محدوده فرکانسی بین 30 کیلوهرتز تا 40 کیلوهرتز اندازهگیری میکنند. امواج فشار با استفاده از یک حسگر رزونانت اندازهگیری میشوند که امواج را به یک بار الکتریکی (electrical charge) کوچک تبدیل میکند. آزمونهای فراصوت معمولاً همراه با تکنیکهای پایش و آنالیز ارتعاش استفاده میشوند. تکنسینها معمولاً از آزمون فراصوت برای فیلتر کردن تجهیزات خوب از تجهیزات بد استفاده میکنند و سپس با انجام آنالیز ارتعاش عمیق بر روی تجهیزات بد علت اصلی مشکلات این تجهیزات را پیدا میکنند.
۵. پایش و آنالیز روغن
پایش روغن تکنیکی است که معمولاً در آزمایشگاهها و با استفاده از آزمایشهای شیمیایی با هدف تعیین وضعیت روغنکاری تجهیز انجام میشود. امروزه حسگرهای سودهشناسی یا تریبولوژی برای نظارت دائمی کیفیت روغن وجود دارد. نتایج پایش و آنالیز روغن نشان میدهد که آیا روغن باید تعویض شود یا نه. این فناوری به ندرت برای ارزیابی وضعیت دارایی استفاده میشود و بیشتر بر روی تعیین وضعیت روانکنندهها (ویسکوزیته، پایه و غیره) متمرکز است. با این حال، کنترل و نظارت بر سطح روغن و کیفیت آن برای جلوگیری از تعمیرات پرهزینه بسیار مهم است.
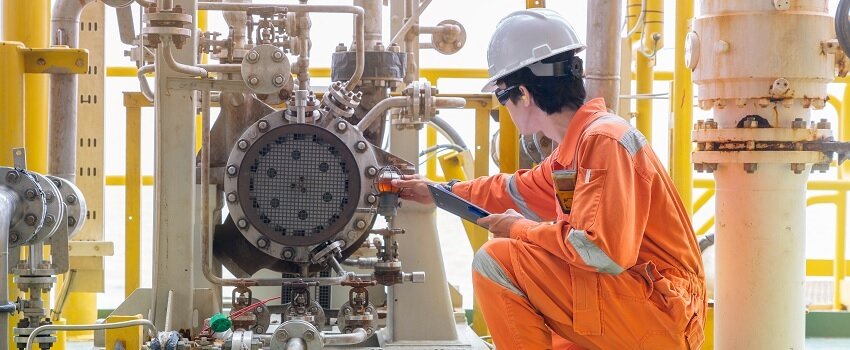
علاوه بر اینها دهها تکنیک دیگر پایش وضعیت تجهیز وجود دارد. که با انتخاب درست این تکنیکها میتوان راندمان تجهیزات مکانیکی را به شکل معناداری افزایش داد. انتخاب سیستم و تکنیک مورد نظر پایش وضعیت تجهیز، به درجه بحرانیت آن تجهیز، هزینه جایگزینی/شکست، امکانات دسترسی به تجهیز، هزینه نظارت و نرخ پیشرفت خطا مورد انتظار بستگی دارد.
سیستمهای پایش وضعیت قابل حمل و معمولاً کمهزینه معمولاً برای تجهیزات غیر بحرانی با هزینههای تعویض قطعهٔ پایین و نرخ جلوروی خطای آهسته استفاده میشوند.
با این وجود، اخیرا پیشرفتهای بزرگ در فناوری باعث شده است که راهکارهای پایش وضعیت دائمی نیز بسیار مقرون بهصرفهتر از قبل شوند. و امروزه بسیاری از سازمانها و واحدهای تولیدی تجهیز محور به دلیل کاهش هزینه، قابلیت اطمینان بالاتر و کارایی بیشتر، خیلی بیشتر از قبل به سمت سیستمهای دائمی پایش وضعیت اقبال نشان میدهند.
تشخیص عیوب با استفاده از پایش وضعیت
این سناریو را در نظر داشته باشید: خودروی خود را برای انجام نگهداری و تعمیرات برنامهریزیشده به طور منظم چکاپ میکنید. دو هفته اما خودروی شما به دلیل یک موضوع کاملاً متفاوت خراب میشود. درست مانند اتومبیلها، تجهیزات نیز در برابر این خرابیهای تصادفی و غیرقابل پیشبینی آسیب پذیر هستند. انواع خاصی از نگهداری و تعمیرات، مانند نگهداری و تعمیرات مبتنی بر قابلیت اطمینان و نگهداری و تعمیرات پیشبینانه، بر این اصل استوار است که خرابیها همیشه خطی نیستند و نیازمند آنالیز و تحلیل چندین جنبه از تجهیز برای شناسایی نشانههای خرابی احتمالی آن است. به همین دلیل پایش وضعیت امری بسیار مفید است و به شما امکان میدهد بر چندین جنبه از وضعیت تجهیز را به طور همزمان با استفاده از تکنیکهای اشارهشده در بالا نظارت و پایش کنید.
پایش وضعیت، منحنی P-F و فاصلهٔ P-F
منحنی P-F نموداری است که سلامت دارایی و تجهیز را در طول زمان نشان میدهد تا فاصله بین خرابی بالقوه و خرابی عملی تجهیز را تعیین کند. خرابی یا شکست بالقوه به عنوان نقطهای آغازین تعریف میشود که در آن شروع خرابی تجهیز حادث میشود و معمولاً با نشانهای قابل تشخیص است. به عنوان مثال، تاریخچه ثبتشدهٔ خرابیهای یاتاقان میتواند نشان دهد که معمولاً اگر دمای یاتاقانها به بالای ۷۰ درجه سانتیگراد برسد، دچار خرابی میشوند.خرابی عملی یا کارکردی (Functional Failure) هم نقطهای است که در آن یک تجهیز دیگر مفید واقع نشود و کارکرد عملیاتی نداشته باشد. برای مثال، شما حدود پنج روز از زمانی که دمای یاتاقان از ۷۰ درجه فراتر میرود تا زمانی که آن یاتاقان دچار خرابی عملی می شود، فرصا دارید. منحنی P-F بر روی محور X زمان را نشان میدهد و در محور Y با شاخصههای کمی وضعیت تجهیز را به نمایش میگذارد. در این مثال، شما باید هر دو تا سه روز یک بار یاتاقان را بررسی کنید.
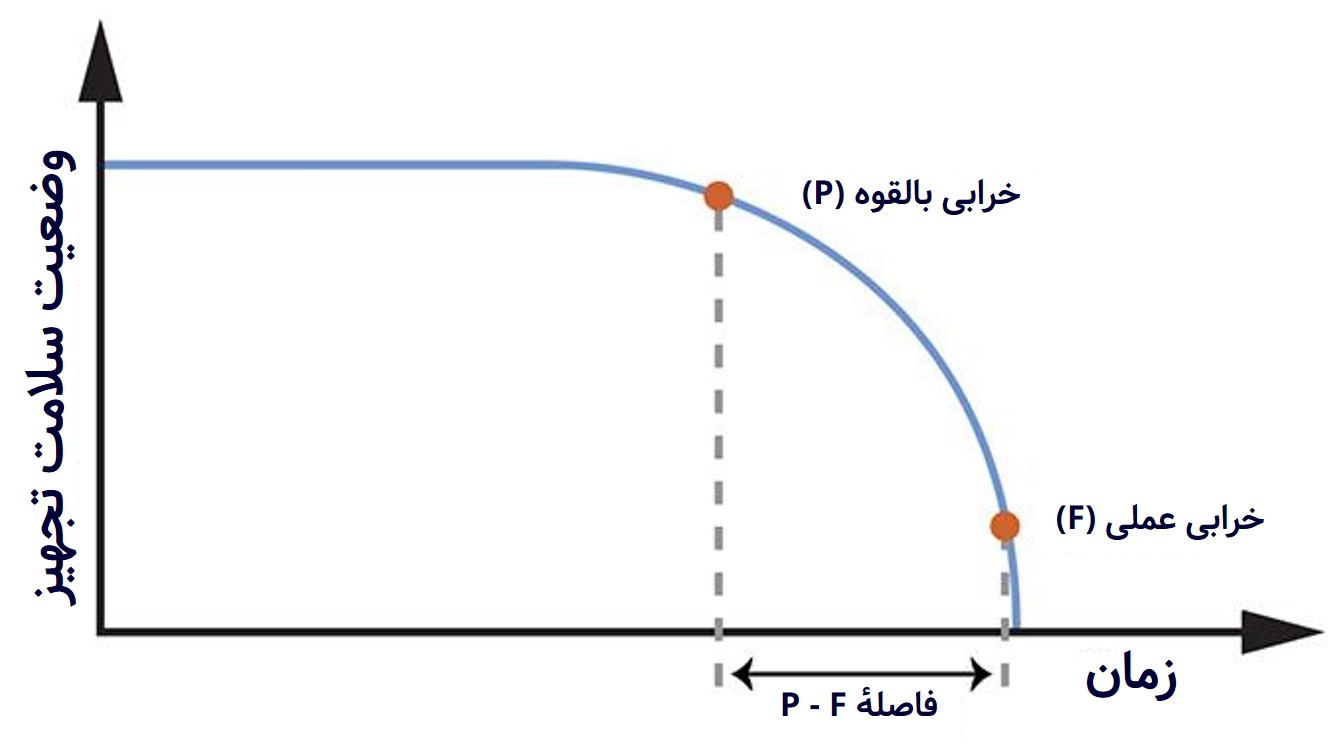
پایش وضعیت نقش مهمی در تشخیص فاصله ٔ P-F در منحنی P-F ایفا میکند. فاصله P-F زمان بین خرابی بالقوه یک تجهیز و خرابی پیشبینیشدهٔ عملیاتی آن است. مهم این است که فاصله بازرسیهای شما باید کوچکتر از فاصلهٔ P-F باشد تا قبل از وقوع خرابی، مشکل را تشخیص دهید. استفاده از پایش وضعیت به شما امکان میدهد وضعیت دارایی را مورد سنجش قرار دهید و فاصله P-F را به حداکثر برسانید. نظارت بر مواردی مانند نمونهبرداری و آنالیز روغن، تست انتشار صوتی، آنالیز ارتعاش و دمانگاری مادون قرمز، همگی تکنیکهای مبتنی بر پایش وضعیت هستند که به شما چشماندازی گسترده از وضعیت فعلی تجهیز خود ارائه میدهد.
به گفته دیل بلان (Dale Blann)، مدیر عامل موسسه مارشال، روش و بازههای زمانی نظارت و پایش باعث ایجاد تفاوتهای معنادار در فاصلهٔ P-F میشود. بلان میگوید پایش وضعیت آنلاین مبتنی بر فناوری بیشترین فواصل P-F را نوید میدهد و نسبت به سایر انواع بازرسیها مانند بازرسیهای آفلاین که در آن ماشینها معمولاً برای بازرسی باید خاموش شوند، اختلال کمتری ایجاد میکنند.
پایش وضعیت و اینترنت اشیای صنعتی
اینترنت اشیای صنعتی (IIoT) اصولاً به شبکهای از دستگاههای متصل به هم که بر روی ماشینآلات و تجهیزات مکانیکی و دیجیتال نصب شدهاند و به شما توانایی انتقال دادهها بر روی یک شبکه بزرگ بدون نیاز به تعامل انسان – انسان یا انسان – کامپیوتر را میدهد، اطلاق میشود.امروزه سیستمهای مدرن پایش وضعیت از اینترنت اشیای صنعتی (IIoT) استفاده میکنند تا انواع متعددی از نرمافزارهای پایش را در یک سیستم ریل تایم، در هر مکانی از هر جای دنیا و مورد استفاده در دستگاههای متعدد بکار گیرند.
سیستمهای پایش وضعیت مبتنی بر فناوری اینترنت اشیای صنعتی سازمانها را قادر میسازد تا به راحتی با نظارت دائمی بر چندین جنبه از وضعیت هر تجهیز و کنترل عملکرد آن، مسائل و مشکلات هر تجهیز را شناسایی کنند، مسائل را تشخیص دهند و حتی به طور خودکار نگهداری و تعمیرات را براساس محدودیتهای از پیش تعیین شده برنامهریزی کنند. برخی از بزرگترین مزایای پایش وضعیت مبتنی بر IIoT عبارتند از:
۱. فضای ذخیره سازی ابری
اینترنت اشیای صنعتی (IIoT) از پردازش ابری بهره میبرد و به شرکتها اجازه میدهد تا برخلاف ذخیرهسازی دادهها در محل یا مرکز دادهٔ فیزیکی خود شرکت، مقادیر زیادی از دادههای خود را به سادگی در فضای ابری ذخیره کنند. این موضوع به دلیل جریان مداوم دادههای تولید شده توسط ماشینهای متصل به سیستمهای پایش وضعیت آنلاین و حجم عظیم این دادهها مزیتی بزرگ به حساب میآید. به عنوان مثال، تحقیقات نشان میدهد که بر روی یک توربین بادی 2000 لاگ در دقیقه برداشته میشود که این حجم پردازش برابر با تولید حدود یک ترابایت داده در هر هفته است.
۲. تجزیه و تحلیل پیچیده
سیستمهای پایش وضعیت مبتنی بر IIoT از الگوریتمهای یادگیری ماشین برای نتیجهگیری در مورد مواردی مانند سلامت تجهیزات و روشهای بهبود دقت تشخیص عیوب و مشکلات استفاده میکنند.
۳. امکان استفاده از دادهها از چندین ماشین
الگوریتمهای یادگیری ماشین برای خلق یک مدل پیشبینی به میزان قابل توجهی از داده نیاز دارند. به عنوان مثال به منظور ایجاد یک مدل پیشبینیکننده برای شناسایی میزان ارتعاشی که منجر به خمیده شدن شفتها میشود نیاز به بررسی و پایش وضعیت نزدیک به 100 مورد از شفتهای خمیده است که این موضوع احتمالا سالها به طول خواهد انجامید.
جمعآوری دادههای ارتعاش از چندین تجهیز یکسان به طور همزمان به تکنسینها این امکان را میدهد که همان مقدار داده را در زمان بسیار کمتری جمعآوری کنند. علاوه بر این، جمعآوری دادهها از بسیاری از تجهیزات و ماشینآلات در طول زمان باعث افزایش دقت و بهبود موفقیت مدل پیشبینی میشود.
۴. نیاز کمتر به فعالیت نیروی انسانی
سیستمهای مبتنی بر IIoT امکان پایش از راه دور صدها تجهیز صنعتی را از هر مکانی و توسط دستگاههای متعدد را فراهم میکنند. این امکان یک مزیت قابل توجه برای صنایعی مانند تولید و توزیع برق و نفت و گاز است، زیرا در این صنایع نظارت از راه دور بر تاسیساتی چون خطوط لوله، دکلهای حفاری دریایی و تاسیسات تولید برق را آسانتر میکند. سیستمهای مبتنی بر اینترنت اشیای صنعتی، میتوانند به صورت خودکار دادههای تجهیز را به صورت ریلتایم جمعآوری و تجمیع کرده و به دست افرادی که باید دسترسی به این اطلاعات داشتند در هر کجا که قرار دارند برسانند.
هنگام طراحی یک سیستم پایش وضعیت مبتنی بر فناوری IIoT، و قبل از خرید حسگرها و سایر تجهیزات باید به چند نکته توجه داشت. یکی از این نکات مهم این است که هنگام انتخاب حسگر به نوع تجهیزاتی که میخواهید مورد پایش قرار دهید، متغیرهای داده (نوع اطلاعاتی که میخواهید جمعآوری کنید) و نحوه استفاده از دادهها توجه داشته باشید.
همچنین مهم است که بدانید هر چند وقت یک بار قصد دارید این دادهها را بررسی کنید؟ زیرا به طور کلی، هر چه بیشتر نیاز به بررسی دادههای خود داشته باشید، پهنای باند و میزان حافظهٔ مورد نیاز برای ذخیره دادهها نیز بیشتر خواهد شد. همچنین میتوانید سیستمی خریداری کنید که به شما امکان میدهد زمانهایی از پیش تعیینشده را برای بازبینی دادهها تنظیم کنید. به عنوان مثال، شاید بخواهید یک تجهیز خاص را فقط در ابتدای یک شیفت کاری بررسی کنید و دادههای آن را دو بار در روز مرور کنید.
نکتهٔ دیگر این است که آیا در نزدیکی تجهیز خود امکان امکان اتصال به اینترنت وجود دارد؟ اگر این دسترسی وجود ندارد، باید هزینهٔ رساندن اینترنت به آن نقطه را نیز در هزینههای کلی خود لحاظ کنید.
نکتهٔ دیگر توجه به محل استقرار تجهیزات شما است: آیا این در فضای سربسته قرار گرفتهاند یا در فضای باز هستند؟ تجهیزات نصبشده در فضای باز ممکن است محدودیتها و اختلالاتی در امکان اتصال به اینترنت داشته باشند. علاوه بر این، محدودیتهای فضای باز شرایط سختتری را برای تنظیمات حسگرها و سایر تجهیزات پایش وضعیت به آنها تحمیل میکند که ممکن است همین موضوع باعث شود به سراغ حسگرهای ضد آب یا مقاوم در برابر آبوهواهای خاص بروید و در کل به دنبال حسگرها و تجهیزات مقاومتر باشید.